How Injection Molders Help OEMs Maintain Quality Standards
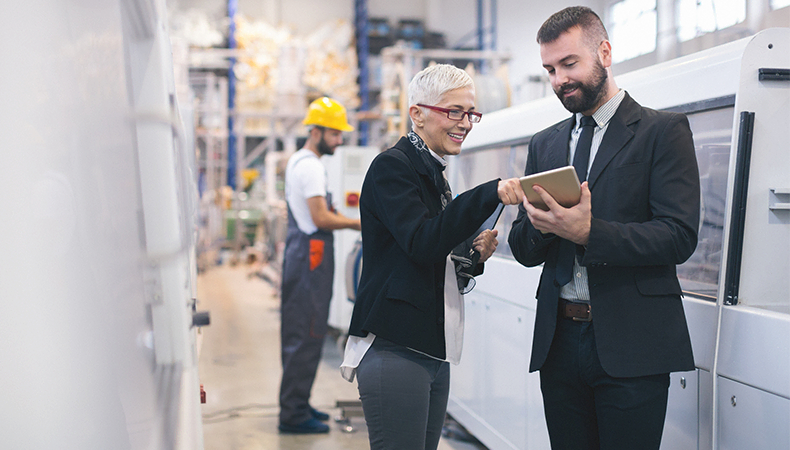
Quality is an important benchmark in all aspects of plastic injection molding, and rightfully so. Producing high-quality plastic parts is always the goal, but how often do you stop to consider what a supplier misstep, a materials mix-up, or a process miscalculation could do to the project overall?
Poor quality — in any form and to any degree — can have far-reaching impact. The solution is partnering with an experienced custom injection molder that can help you maintain standards that keep quality at the forefront of every project.
Materials Cost
Scrapping a project or making mid-development modifications to the plastics used could quickly upend a materials budget. Likewise, the changes could trickle down to the final cost of the injection-molded part, possibly jeopardizing profits or market competitiveness.
Selecting plastics with specific performance characteristics or application alignment is already complicated by the more than 25,000 choices available. Add in relying solely on specs from injection molding plastic suppliers and the potential outcome is all the more dicey. Input from an experienced custom injection molder at the project outset gives you insight about the materials and how they respond to different combinations of process variables. In turn, you'll have greater confidence in the overall quality of the end product.
Redesign
Discovering a design is not manufacturable or flawed after production begins is an expensive reckoning. Worse still is not knowing design defects exist until end users bring them to your attention in the form of warranty claims or lawsuits. Complex injection molded plastic parts are highly nuanced, and ignoring factors that influence cycle time — wall thickness, plastic type, mold material, mold cooling, etc. — will likely contribute to poor end product quality.
Working with a custom injection molder that has an engineering team specially trained in Design for Manufacturability (DfM) is key. Involving the team early in the design phase often results in defect detection and correction long before a part is in production — streamlining processes and improving quality without time-consuming rework. There is also the added benefit of having the molder’s engineers weigh in on tool design which, if not optimized for injection molding, could cause part defects and ultimately sabotage product quality.
Unnecessary secondary operations
Poor product quality can result from having too many unnecessary production steps. Secondary operations, for example, provide an opportunity to introduce ill-fitting parts or sophisticated procedures that can add time, expense, and labor to a project.
Depending on the application and provided the custom injection molder is in the loop on design, plastic injection molding is versatile enough to eliminate some secondary operations. For example, plastic overmolding may be the appropriate solution for seamlessly combining multiple materials into a single product or part. In addition to lowering production costs and labor requirements, plastic injection overmolding increases shelf appeal and boosts product performance — both factors in high-quality plastic parts.
Delays
Time is money, and there are few places where that’s more true than on a production line. Without input from an experienced custom injection molder on a project from design through completion, there is a higher likelihood of compromised part quality. Further, an injection molder with expert scientific molding engineers can optimize plastic injection molding process steps to ensure consistent part repeatability across machines, operators, lines, and runs to leverage production efficiencies and minimize delays.
Taken in total, quality is both a goal and expectation for injection-molded plastic parts. How you prioritize quality when choosing an injection molding partner will influence results, as will other factors detailed in Critical-Use Plastic Parts: Key Design and Injection Molding Considerations. Click the button below for your copy of this valuable whitepaper now.
Subscribe
TO OUR BLOG
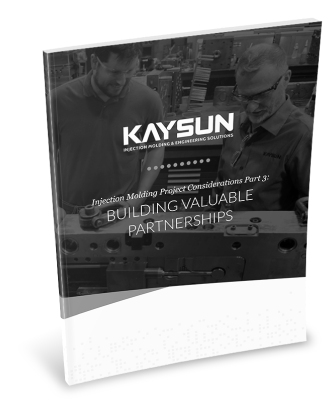
How Do Injection Molder Partnerships Influence Project Costs?
You Might Also Like...
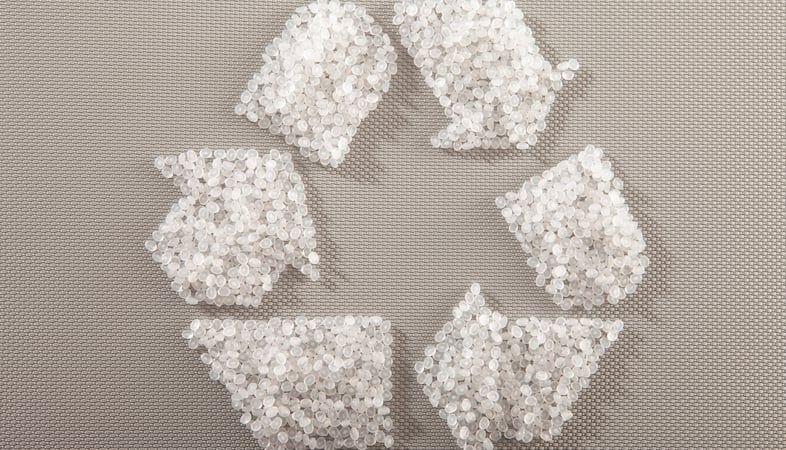
How Kaysun’s Culture of Sustainability Benefits OEMs and The Planet
Injection-molded parts and products are staples for OEMs in industries ranging fro…
READ MORE
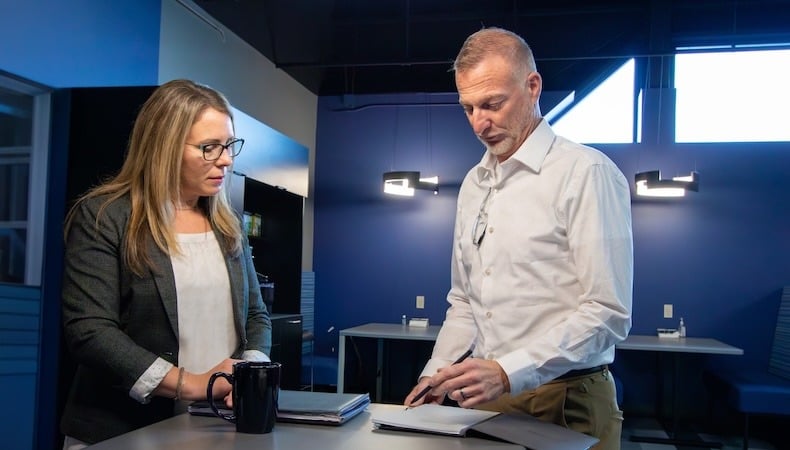
12 Common Injection Molding Questions — Answered!
Injection molding is a versatile and precise process, making it ideal for OEMs tha…
READ MORE
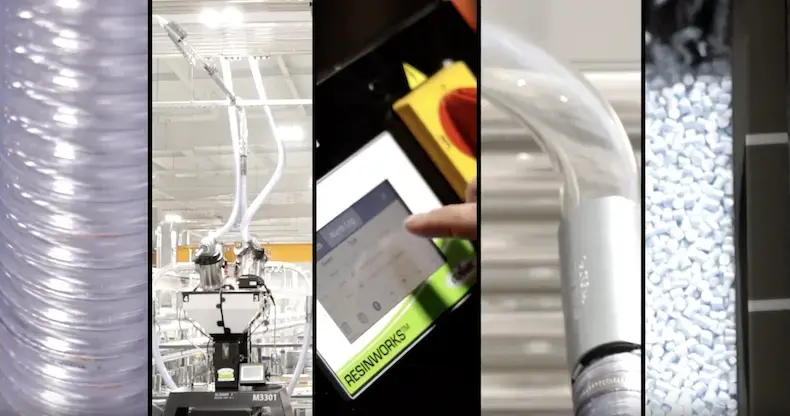
How Centralized Material Handling Streamlines Injection Molding
We consistently look for new ways to deliver timely service and top-quality parts …
READ MORE