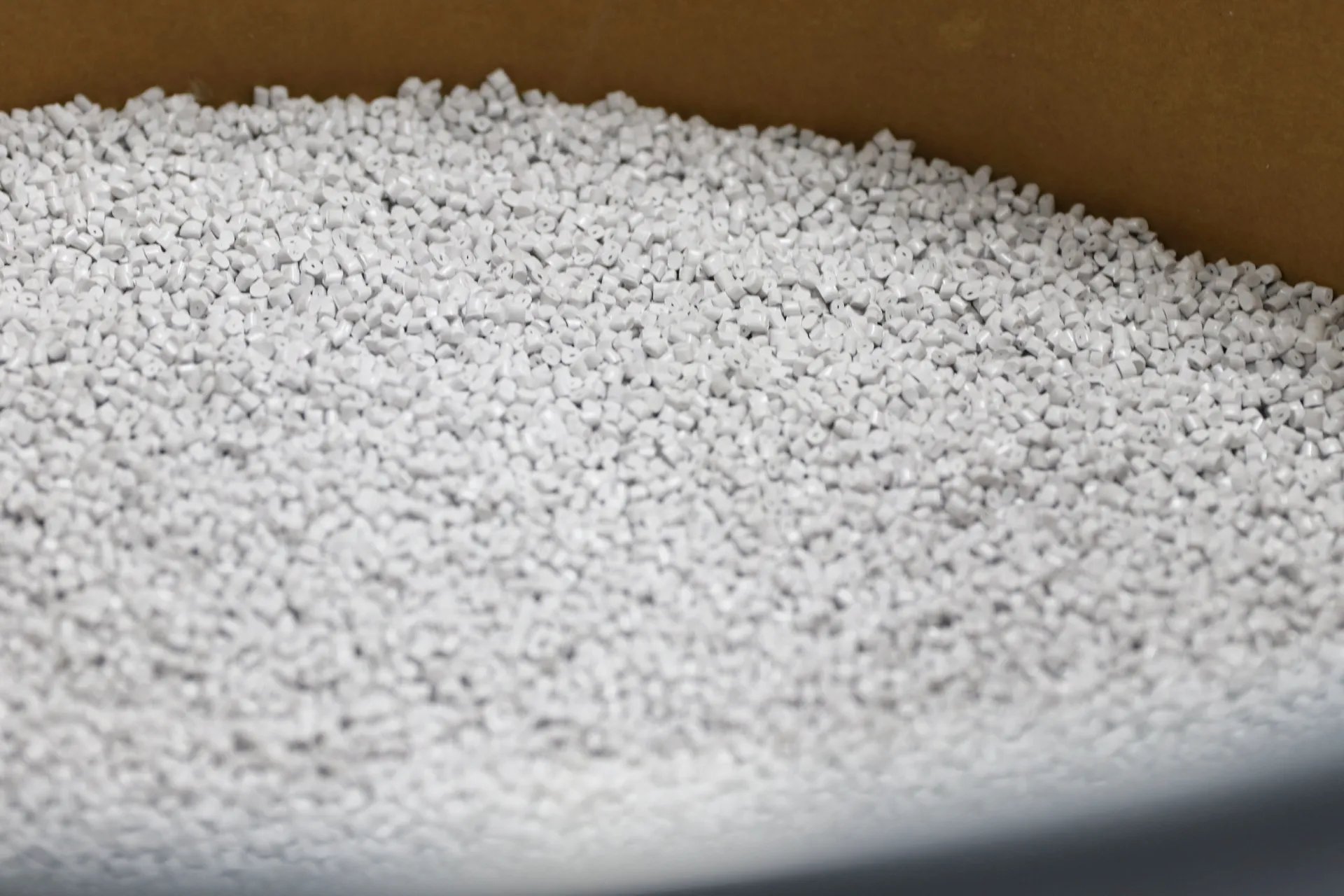
Injection Molding Material Selection
The recent global resin shortage left the plastics industry and the manufacturers that rely on it in turmoil. The infrastructure behind supply and demand, prices, and logistics was devastated — creating short- and long-term consequences, including a re-examination of how OEMs work with injection molding partners to strategically manage materials.
Kaysun established processes for qualifying and testing alternative materials using DfM analysis and physical product trials for short-term solutions. For the longer term, acting as a central point of contact for injection molding materials management and identifying multiple materials as solutions for ready part-molding streamlined otherwise problematic processes.
With more than 25,000 engineered plastic materials available, knowledge was power in overcoming resin shortage challenges. Kaysun engineers’ in-depth expertise in materials science, behaviors, and formulations was pivotal during the crisis, and remains so for everyday needs.
The wide variety of plastics available opens up a number of possibilities, but making the right choice takes a thorough understanding of your application. More specifically, it takes guidance from a proven injection molding partner.
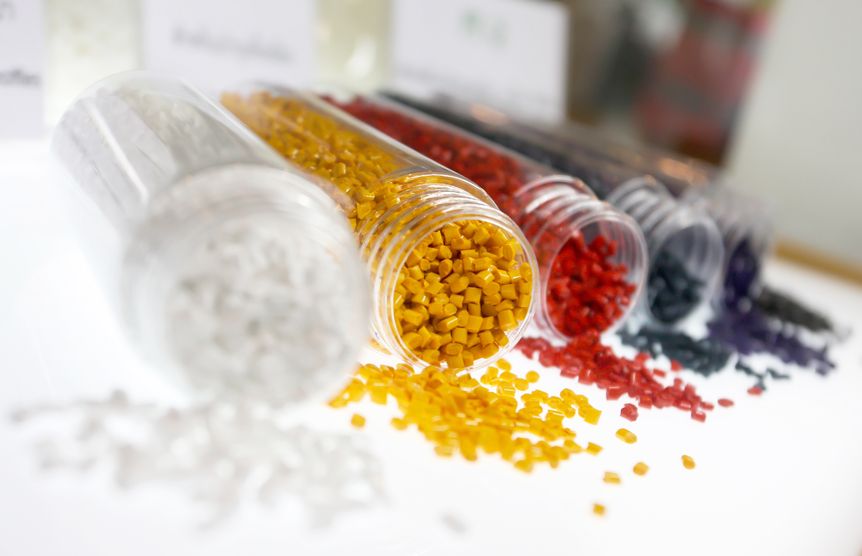
Steps to
Selecting Materials
For engineers working with the Kaysun team, the process usually entails three steps:
1. Discuss
Answering key questions during product design discussions with an expert plastics engineer helps us gain key insights into what the material needs to do:
- What is the expected physical load for the product?
- What is the mechanical function?
- Will the product be used under conditions of fluctuating and/or extreme temperatures?
- Will there be any exposure to chemicals?
- Will dissimilar materials be used in assembly?
2. Research
Project-specific answers are used as the basis for a search in our extensive in-house database — founded on several decades of injection molding work and materials knowledge — to find plastics with the appropriate characteristics, such as:
- Strength
- Rigidity
- Chemical resistance
- Temperature resistance
- Flexibility
- Impact resistance
- Appearance
- Conductivity/shielding
- Frictional properties
- Flame resistance
In conjunction with the database search, we consult with our materials suppliers to narrow the list of recommendations to the top 3 or 4 choices that best align with project performance and pricing needs.
3. Recommend
We confidently deliver a focused list of materials for engineers to consider. This robust process ensures our customers’ engineering teams save time and money in the long run since certain aspects of the part design can be modified prior to production, avoiding potentially costly rework. Our refined holistic view of the entire part strategy — design, specifications, requirements, improvements — provides far more value than if an engineer is left to decide on materials based on material specs alone.
Thermoset or Thermoplastic?
Despite the many thousands of engineered materials available, plastics fall into two main types: thermoset or thermoplastic. The terms sound similar and both are appropriate for many applications but there is a notable difference in how they behave during processing.
Thermosets
(e.g., liquid silicone rubber (LSR), epoxy, phenolic) join polymers on one application of heat and structure chemical bonds that harden permanently on cooling. The chemical reaction cannot be reversed, so thermoset parts cannot be re-shaped or re-melted. Thermosets have strength, chemical resistance, and temperature resistance that make them appropriate for medical implantables, electronic interfaces/touchpads, and wiring harnesses/housings.
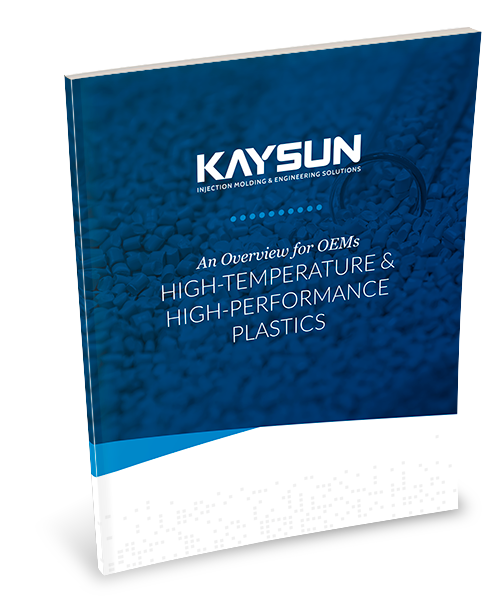
Amorphous & Semi-Crystalline
Whether designated a thermoplastic or thermoset, plastics are made up of polymers — long chains of repeated molecular units. The ways in which these chains align determine the plastic’s macroscopic properties. In turn, the macroscopic properties dictate the category in which the resins fall. Specific to thermoplastics, these resin categories are amorphous or semi-crystalline.
Amorphous
When polymer chain orientations are random, the plastic lacks a clear structure and is deemed amorphous.
General Advantages
- Softens over a broad range of temperatures
- Easy to thermoform
- Excellent bonding with adhesives and solvents
General Disadvantages
- Vulnerable to stress cracking
- Poor chemical resistance
- Appropriate for structural applications only
Characteristics
- Low cost, temperature resistance, and strength
- Good dimensional stability
- Usually transparent
Representative Resins
- Acrylic (PMMA)
- Polystyrene (PS)
- Acrylonitrile Butadiene Styrene (ABS)
- Polyvinyl Chloride (PVC)
- Polyethylene Terepthalate Glycol (PETG)
- Cellulose Acetate Butyrate (CAB)
Characteristics
- Moderate cost, temperature resistance, and strength
- Good to excellent impact resistance
- Good dimensional stability and optics
Representative Resins
- Polycarbonate (PC)
- Polyphenylene Oxide (Mod PPO)
- Polyphenylene Ether (Mod PPE)
- Thermoplastic Polyurethane (TPU)
Characteristics
- High cost, temperature resistance, and strength
- Good stiffness
- Resistant to hot water and steam
Representative Resins
- Polysulfone (PSU)
- Polyetherimide (PEI)
- Polyethersulfone (PES)
- Polyarylsulfone (PAS)
- Polyarylethersulfone (PAES)
Semi-crystalline
When polymer chains arrange themselves in an orderly, densely packed fashion, the plastic is deemed semi-crystalline.
General Advantages
- Resistant to stress cracking
- Good fatigue resistance
- Appropriate for bearing, wear, and structural applications
General Disadvantages
- Sharp melting point
- Difficult to thermoform
- Poor bonding with adhesives and solvents
Characteristics
- Low cost, temperature resistance, and strength
- Good electrical properties and toughness
- Negligible moisture absorption
- Low COF
Representative Resins
- High-Density Polyethylene (HDPE)
- Low-Density Polyethylene (LDPE)
- Polypropylene (PP)
- Polymethylpentene (PMP)
Characteristics
- Moderate cost, temperature resistance, and strength
- Good chemical resistance, and bearing and wear properties
- Difficult to bond
- Low COF
Representative Resins
- Nylon (PA)
- Acetal (POM)
- Polyethylene Terephthalate (PET)
- Polybutylene Terephthalate (PBT)
- Ultra High Molecular Weight Polyethylene (UHMW-PE)
Characteristics
- High cost, temperature resistance, and strength
- Good electrical properties and toughness
- Excellent chemical resistance
- Low COF
Representative Resins
- Polyvinylidene Flouride (PVDF)
- Polytetrafluroethylene (PTFE)
- Ethylene-Chlorotrifluroethylene (ECTFE)
- Fluorinated Ethylene Propylene (FEP)
- Polychlorotrifluroethylene (PTCFE)
- Perfluoroalkoxy (PFA)
- Polyphenylene Sulfide (PPS)
- Polyetheretherketone (PEEK)
Additives and Alloys
Plastics’ characteristics can be changed by mixing or combining different types of polymers and by adding non-plastic materials.
Additives are used to improve specific properties such as strength, rigidity, UV-resistance, and flame resistance — a versatility that’s proving particularly beneficial as more industries incorporate metal-to-plastic conversion into their production processes.
The most common categories of additives are particulate fillers and reinforcing fillers. Particulate fillers can reduce costs and improve properties such as modulus, conductivity, heat and ultraviolet light resistance. Popular particulate fillers include:
- Mineral
- Silica
- Ceramic
- Carbon powder/fiber
- Powdered metal
- Glass microspheres/fibers
Reinforcing fillers improve mechanical properties. Popular reinforcing fillers include:
- Long glass fiber additives to improve stiffness and strength, increase temperature performance (up to 150℉), and create a moderate surface appearance
- Short glass fiber additives improve stiffness, increase temperature performance, and offer better aesthetics than long glass fibers. Since the glass content is 30% or lower, short glass fibers allow parts to look comparable to unreinforced plastic parts
- Carbon, stainless steel, and Kevlar fillers improve conductive and/or shielding properties
By applying engineering, materials science, scientific molding, and Design for Manufacturability (DfM) analysis, Kaysun provides insights into how plastic injection molding materials behave when flowing and filling tools. Understanding melt temperatures, flow rates, and cooling rates is more instructive than relying solely on basic specification information provided by the plastics manufacturer.
This kind of care, knowledge, and detailed data guides us in selecting the best plastic for your project, designing the ideal tool, and developing the most efficient and cost-effective injection molding process possible — all of which makes working with Kaysun a true value-added partnership.
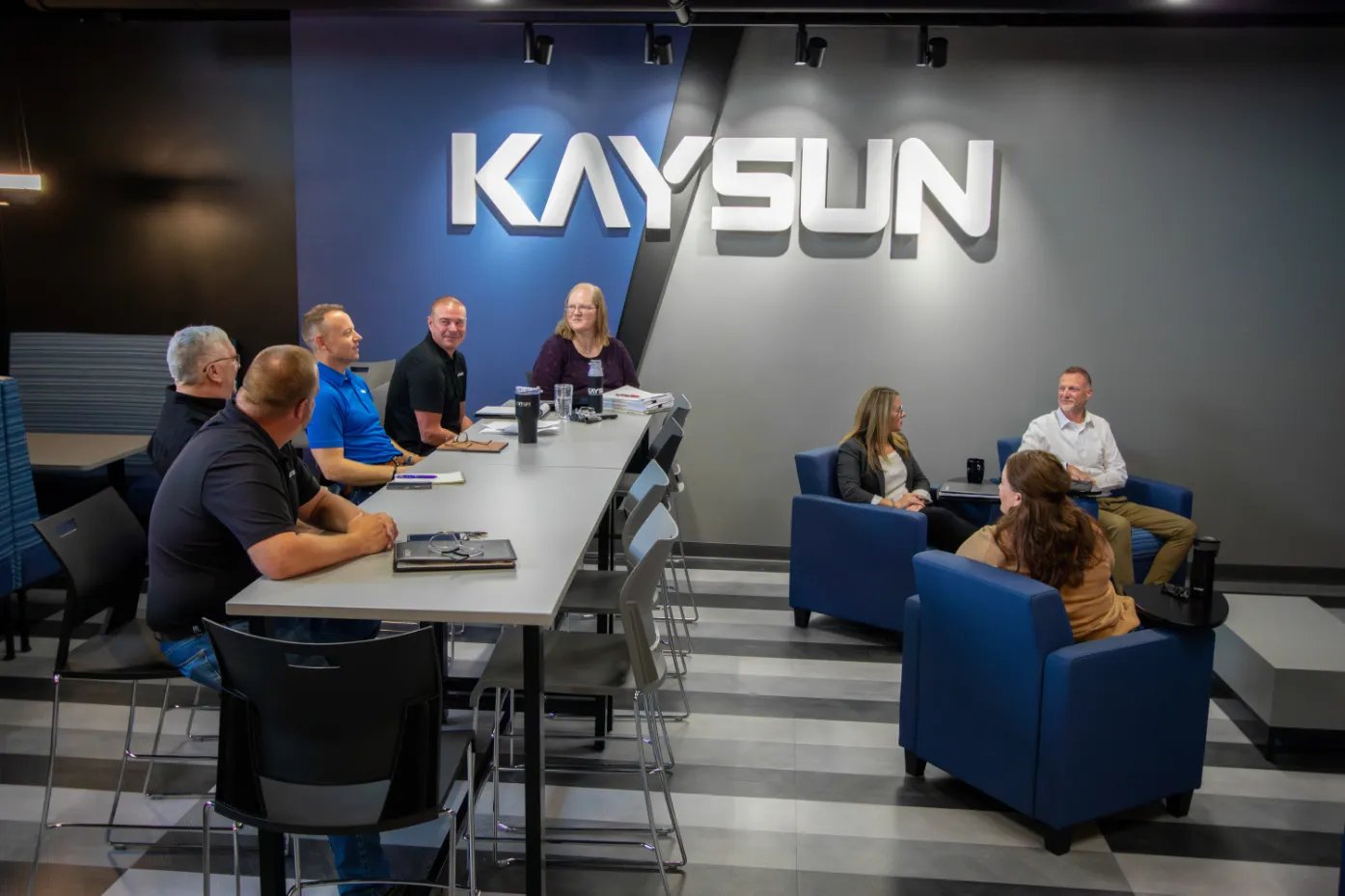
Does your company fit our ideal customer profile?
Complete the form to request a free consultation with our plastic engineering experts.