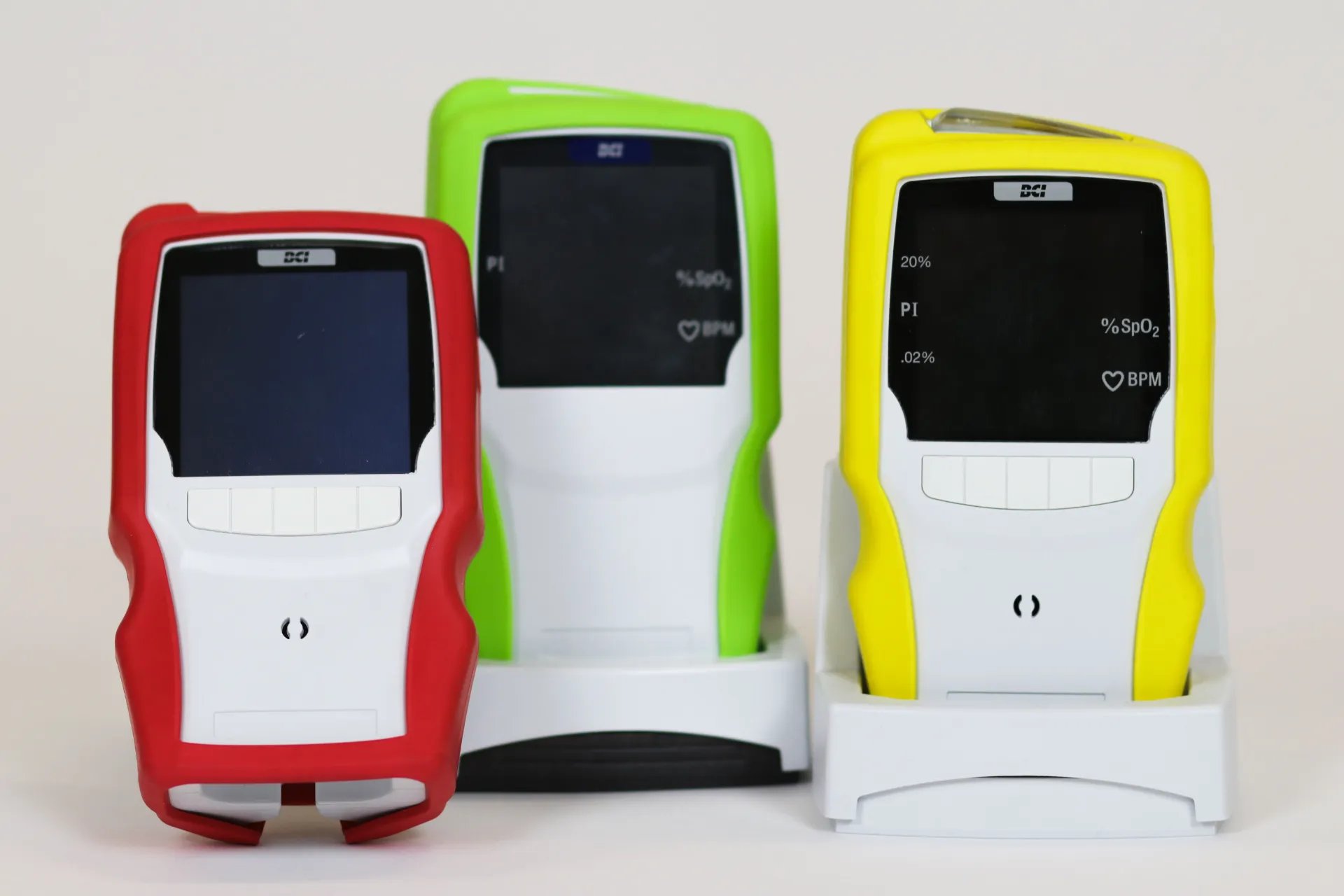
Overmolding
What is Overmolding
Overmolding is a multi-step injection molding process, overmolding combines two or more materials into one final product. Typically, a rigid substrate base is overlaid with a thin, pliable rubber-like exterior (e.g., thermoplastic elastomer (TPE).
The ultimate in multi-material injection molding, overmolding seamlessly combines multiple materials into one part or product to improve product design, performance, and aesthetics.
The plastic overmolding process involves multiple machines, one for molding the base component (or substrate) and another for applying a thin layer of thermoplastic elastomer (TPE) to the substrate. The result? Versatile application-specific solutions for manufacturers across a wide range of industries.
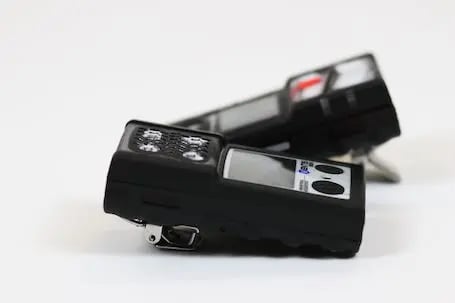
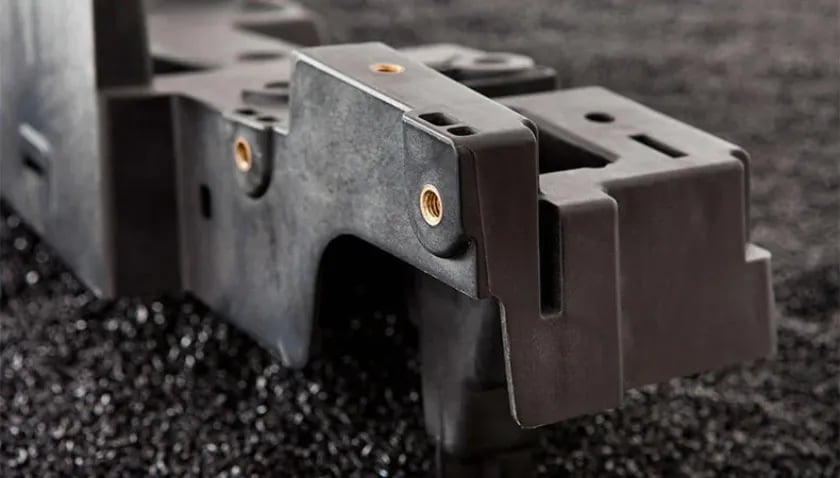
Overmolding vs. Insert Molding
Experienced injection molders such as Kaysun offer a breadth of services, including overmolding and insert molding. The two methods are similar, yet distinctly different.
In insert molding, tooling is built to hold a solid component — the insert — within another tool. TPE or thermoplastic material is injected into the second tool, surrounding the insert and yielding a finished part.
The insert can be a single part or component, or a combination of individual components that are carefully configured inside the tool and then sealed together with the plastic during the insert-molding process.
This method of insert injection molding can actually result in greater strength, flexibility, and/or functionality, compared to attaching the individual parts separately during post-production assembly operations. Secondary steps can often be reduced or eliminated entirely with insert molding, saving time, and reducing production costs.
Kaysun’s automation technology and both horizontal and vertical machines for insert molding help minimize human error, improve efficiencies, and ensure optimal outcomes in the insert molding process.
Benefits of Overmolding
In addition to eliminating assembly steps, overmolding adds value in ways that end-users look for and demand in the products they purchase:
- Reduced shock and vibration
- Effective oxygen and/or moisture barriers (seals)
- Dampened sound
- Electrical insulation
- Enhanced chemical/UV resistance
- A wide range of colorful, visually appealing exteriors
For OEMs, overmolding is a practical way to reduce production costs since it:
- Eliminates traditional injection molding process steps required for assembling individual parts
- Creates such a tight substrate-TPE bond that downstream finishing operations (priming, painting, coating, etc.) aren't needed
- Improves product quality and throughput while reducing waste
In conjunction with saving money, overmolding typically saves time — that means products get to market faster, creating valuable competitive advantages for OEMs.
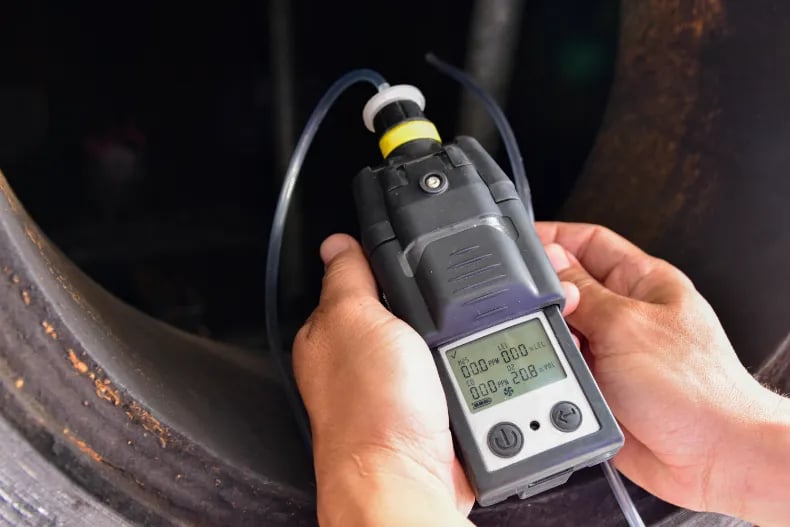
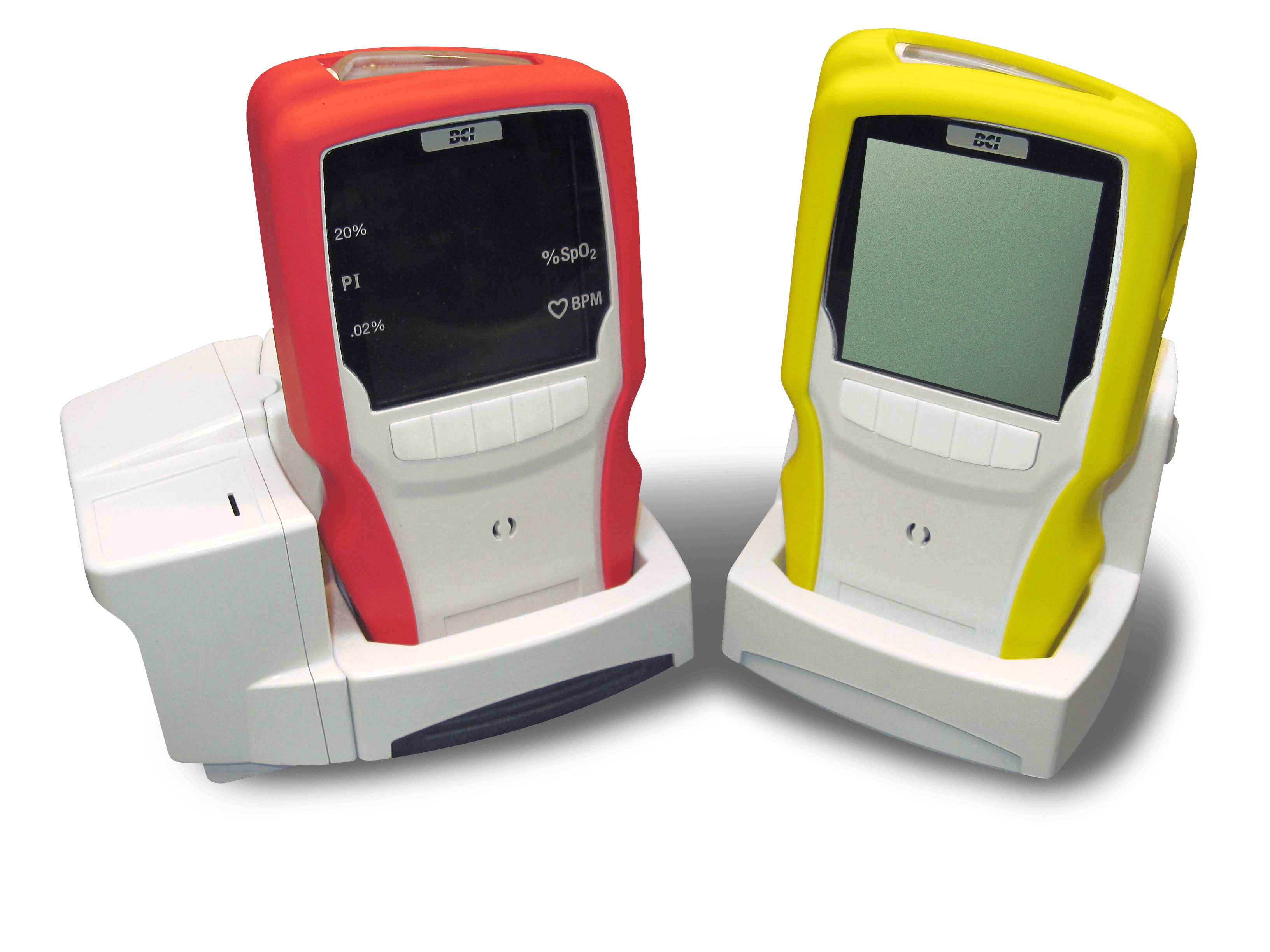
Overmolding Applications
Overmolding is extremely versatile and, therefore, very popular within a variety of industries.
In some instances overmolding materials play more of an aesthetic role, perhaps introducing a contrasting color or texture. They may also provide low-level functionality, such as improving the handle grip on a toothbrush.
Overmolding is often vital for promoting health and safety. This is perhaps best illustrated in the medical, automotive, and defense industries where overmolding protects the performance integrity of portable handheld devices, including:
- Surgical instruments and surgical suite equipment that must remain sterile and able to withstand harsh chemicals and medical environments
- Electrical applications that require weatherproofing, such as outdoor outlet covers or certain automotive wiring assemblies
- Handheld navigation and communication devices used by emergency or military personnel and subjected to extreme conditions and rough handling
Overmolding Materials and Design
For many engineers and designers, the greatest benefit overmolding provides is product “touch” or “feel.” It is also one of the most challenging parts of the overmolding part design since there are many interactive factors to consider, including:
- Friction coefficient
- Hardness
- Thickness
For example, the thinner the TPE layer is (even if the resin is very pliable), the harder it will feel since grip softness is largely determined by the thickness of the TPE layer, not material softness.
Engineers and suppliers continue to develop advanced TPE grades that expand the range of capabilities for bonding high-performing thermoplastic resins to hard plastic substrates. Why does it matter? Not all substrates and TPEs are appropriate matches, so working within compatibility parameters in an overmolding design guide is key to successful outcomes.
Compatible overmolding substrates include:
- Polypropylene
- Copolyester
- Polystyrenes
- Polycarbonate (PC)
- Acrylonitrile butadiene styrene (ABS)
- Polycarbonate ABS (PC-ABS)
- Polymethyl methacrylate (PMMA)
- High-density polyethylene (HDPE)
- Standard and modified Nylon 6
- Polyphenylene oxide (PPO)
Plastic over metal substrates, on the other hand, are inherently compatible materials. There are few — if any — chemical formulations that limit the two from producing a component that consistently performs to its intended purpose.
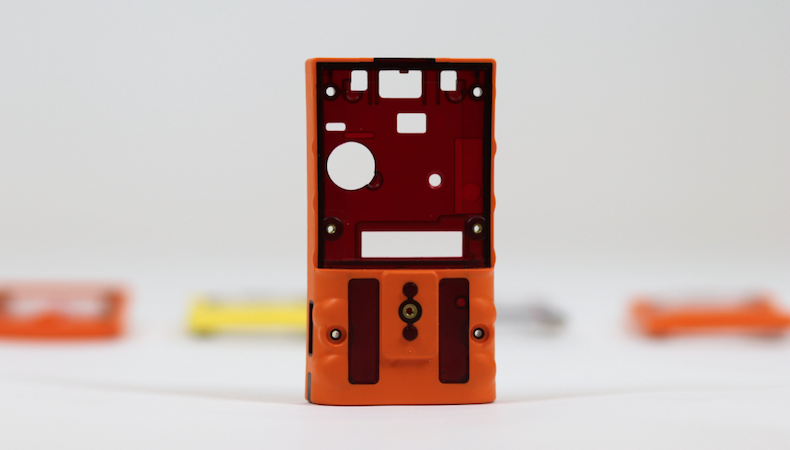
.webp?width=855&height=606&name=KSN-tool-building-13%20(1).webp)
Importance of Prototyping
Overmolding requires carefully designed, highly precise tools that can take months and hundreds of thousands of dollars to build. Factor in maintaining the perfect pressure and speed to completely fill the tool cavity and overmold the substrate without changing the substrate’s position or wasting TPE through overflow — and the need for prototyping becomes clear.
Working with an experienced custom injection molder such as Kaysun is imperative during prototyping. Tool design requires deep scientific knowledge and clear communication between designers, engineers, and production staff. In addition, frequent testing, adjusting, and retesting is necessary to meet the increasingly challenging production goals and timelines of manufacturers.
Prototyping in the earliest stages of product design and development is the most efficient way to:
- Validate performance
- Define realistic processes and schedules
- Maximize manufacturability
- Minimize expensive production tool redesign and testing
Overmolding Expertise
Not every injection molder can overmold. It requires specialized equipment, extensive training, deep knowledge of scientific molding principles, and precise control of multiple variables throughout the production run.
Even the slightest variations can affect quality, so experienced injection molding engineers, technicians, and operators are essential to establish process parameters and production design, as well as monitor in-tool conditions during overmolding.
Manufacturers that align themselves with injection molding partners that have these specialized capabilities — such as Kaysun — will enjoy the full benefits of overmolding, including quality, appealing products manufactured at lower costs.
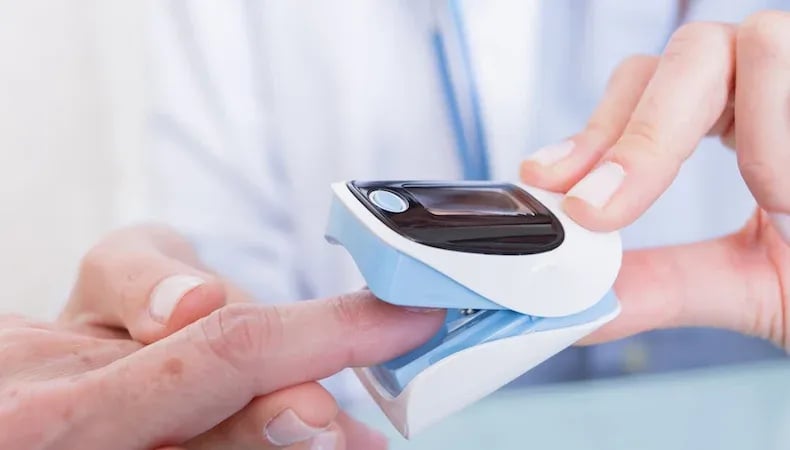
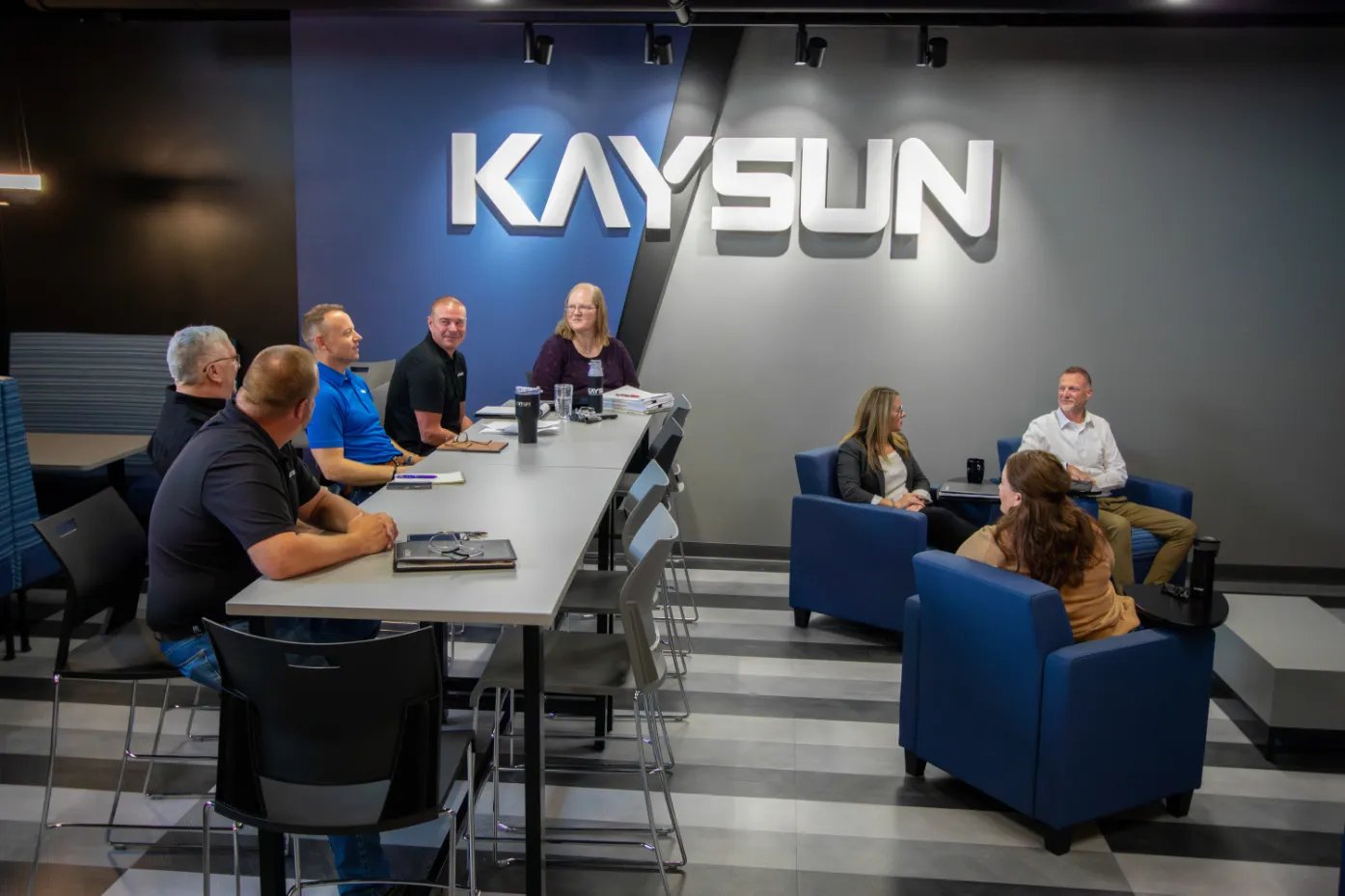
Does your company fit our ideal customer profile?
Complete the form to request a free consultation with our plastic engineering experts.