Top Reasons to Partner with an Injection Molder During Resin Selection
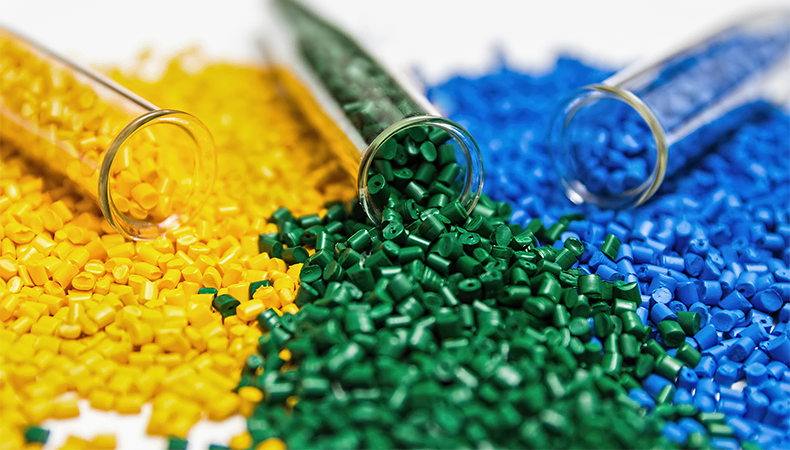
Injection molded parts and products are common in many industries, so much so in fact that commodity molders are often the go-to for injection molding projects. This can be the appropriate choice in many cases, but for industries requiring specialized devices and components, no aspect of a project can be left to chance. This is especially true in the case of resin selection, since the plastic used in production largely dictates how a part or product operates within the end-use environment. Knowing this information is imperative for critical-use applications, where risk mitigation and performance are paramount.
With more than 25,000 types of resins available, it would seem that finding the right resin for your project would be easy; however, finding the exact match that aligns with all of its necessary characteristics requires a concentrated effort.
Moreover, it requires collaboration between your team and an experienced complex injection molder early in the design phase and throughout production. In short, your team is the expert about the project — what an injection molded part will be exposed to and what it must withstand within the parameters of a critical-use application. The molder possesses the plastics and engineering expertise that will eliminate a lot of guesswork or backtracking as to which material should be selected for the part.
The practicalities of bringing in an expert complex injection molder to assist with product design and resin selection are perhaps best illustrated by reviewing unique characteristics certain industries generally require of critical-use injection molded components and devices:
- Medical applications need resins that contain antimicrobial agents, have superior chemical resistance to combat repeated sanitation, qualify as clean room compliant and impact resistance to absorb transport, in-house use and storage without breakage or performance inconsistency
- Automotive applications require resins that are strong enough to replicate metal but are much lighter weight, can maintain aesthetic integrity after repeated exposure to intense sunlight UV rays and other elements, and can withstand high heat and/or extreme temperature fluctuations that routinely occur under the hood
- Military/defense applications need resins that are impact resistant, have exceptional conductivity for electromagnetic interference (EMI) shielding, and comply with federally regulated optical quality, transparency and heat resistance
- Industrial electronics applications, like those used in the emerging LED lighting industry, require resins that can encapsulate primary and secondary optics, protect delicate semiconductor chips, and absorb/deflect repeated UV radiation
While these lists are not intended to be exhaustive or mutually exclusive, they outline just how difficult it can be to find a resin with characteristics that fulfill the specific needs of each critical-use application, especially if you’re relying solely on material specs from a plastics manufacturer. Input from a qualified complex injection molder, like Kaysun, gives you detailed information about — and greater confidence in — how resins respond to various combinations of process variables and successfully meet your project needs.
Learn more about key considerations for assessing your project from a materials perspective in Resin Selection for Industrial Applications. Click the button below to access your copy now!
Subscribe
TO OUR BLOG
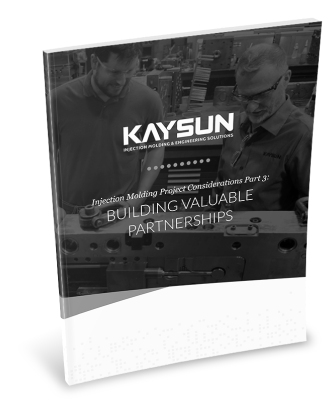
How Do Injection Molder Partnerships Influence Project Costs?
You Might Also Like...
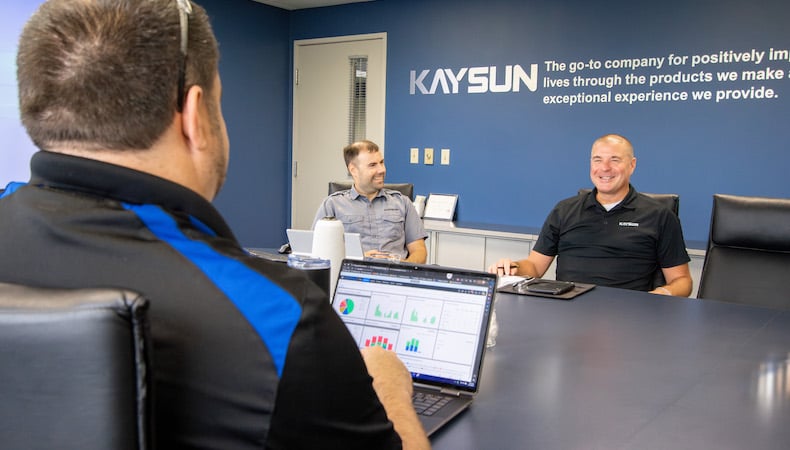
Top 3 Custom Injection Molding Trends to Watch in 2025
Despite being considered more energy efficient and producing less waste than other…
READ MORE
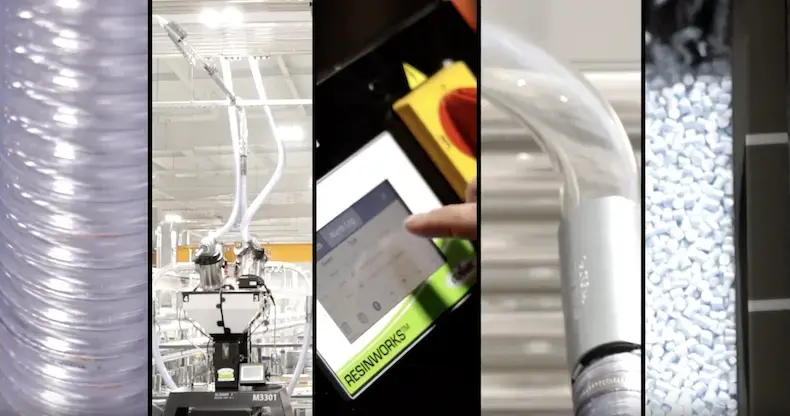
How Centralized Material Handling Streamlines Injection Molding
We consistently look for new ways to deliver timely service and top-quality parts …
READ MORE
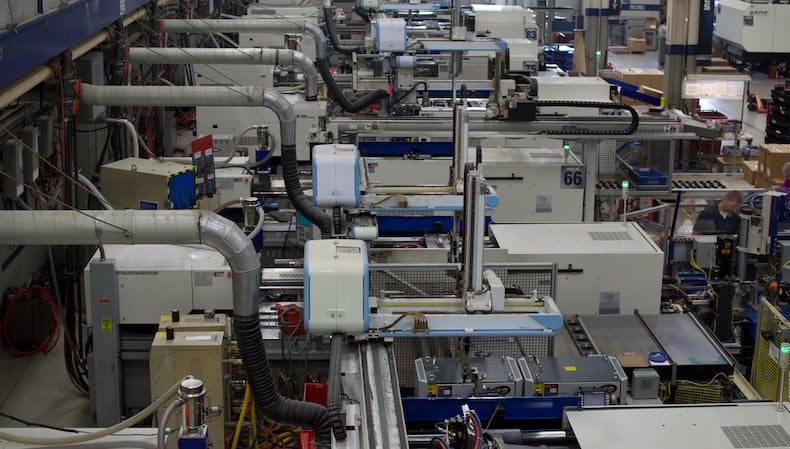
Top 14 Benefits of Injection Molding
OEMs across many industries enjoy the benefits of injection molding. It’s ideal fo…
READ MORE