How Kaysun’s Culture of Sustainability Benefits OEMs and The Planet
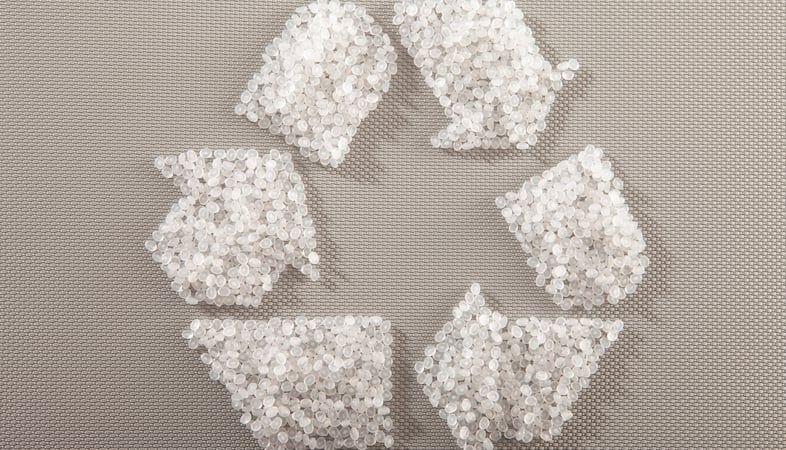
Injection-molded parts and products are staples for OEMs in industries ranging from automotive and medical to industrial and consumer goods. Consistent demand has pushed annual valuations of the injection molding market to roughly $300 billion, and an estimated 5 million tons of plastic parts are made and distributed worldwide each year.
The statistics are impressive, but they also concern certain environmental groups championing the need for responsible plastics use, waste reduction, and recycling in an increasingly fragile ecosystem. Competing priorities of serving customers and protecting the planet can put manufacturers and injection molders in a tough spot, but those embracing sustainable practices are setting precedents that strike balance and signal transformative change.
As a leading custom injection molder and preferred partner to a global network of OEMs, Kaysun is sensitive to the detrimental environmental effects of plastics misuse. We are also passionate about doing our part to minimize the impact.
Guided by our internal Green Team and supported by leadership dedicated to social responsibility, the entire Kaysun team truly invests in — and lives — the tenets of a dynamic culture of sustainability.
Coming Full Circle
Principles of a circular economy — resource optimization, waste reduction, and leveraging the energy efficiencies of state-of-the-art technologies — are mirrored in many injection molders’ approaches to sustainability, including Kaysun’s.
Aligning those broad principles with our philosophy of continuous improvement has brought about fundamental changes to how we apply more sustainable thinking and behaviors to operations, energy efficiencies, and waste reduction and handling.
Building Operations Around Sustainable Injection Molding
Operationally, we continue to keep sustainability highly visible throughout the facility. Placement and use of recycling bins for various types of waste and ongoing training reinforce employees’ “green thinking,” along with regular sustainability-focused team huddles led by shift supervisors.
On a customer level, we scrutinize every aspect of projects from the perspective of sustainability. Our quoting process emphasizes the most cost-effective and sustainable solutions available, including processes such as hot runners and regrind to effectively minimize scrap and waste. In sustainable injection molding design, the Kaysun engineering team employs scientific molding and also incorporates a comprehensive recycling plan for every resin used in projects, whether its newly introduced or a common material.
Knowing upfront how the plastic will be handled, reused, and recycled helps guide what happens on the production floor.
Adopting and Supporting Sustainable Manufacturing Practices
On the production floor, sustainability is interwoven into every project.
There’s big picture thinking in how we proactively recycle every component of packaging from shipped materials — including plastic wrap, metal banding, and pallets.
We also leverage advanced technologies to gain efficiencies that support sustainable manufacturing practices. One of the most recent and impactful additions is our Central Material Handling System (CMHS), which allows for efficient product flow from receipt to press to finished goods, meaning less spillage and chance of human error — which would otherwise contribute to waste.
Further, the CMHS allows us to include regrinding and blending processes with drying, which is a boon for sustainability. The interconnectedness reduces the number of dryers required and the energy needed to power them, and fewer equipment starts-and-stops reduces the carbon footprint of the machinery and overall facility.
The installation of the CMHS alone reduced Kaysun’s annual energy consumption by 1.5 million kilowatt hours, and our use of 54 energy-efficient electric presses further supports these efficiencies.
Our recent facility expansion points to just what these savings mean in practical terms.
We increased our manufacturing floor space by 59% and increased the number of injection molding machines on the floor by 32% — yet our net energy consumption dropped by 1%.
Kaysun’s achievements were recognized by the state of Wisconsin in awarding us the Focus on Energy 2024 Energy Efficiency Excellence Award and a grant to fund future conservation efforts.
Landfill Diversion Extends the Kaysun Culture of Sustainability
Kaysun’s closed loop manufacturing is foundational to how we exercise corporate social responsibility. Reuse and recycling practices minimize waste during production, and our waste-to-energy initiatives expand our stewardship.
The Green Team has set ambitious goals for landfill waste diversion and ultimately zero-waste to landfills. We’ve already successfully diverted more than 2.7 million pounds of plastic waste from landfills — putting us on track for our 2025 goal of 3 million pounds.
Key partnerships significantly factor into our landfill diversion efforts and amplify our waste-to-energy initiatives.
By working with renewable fuel and power producer Convergen Energy to convert plastic waste to clean energy, Kaysun regrind is part of the 40% of recycled plastic used in fuel pellets utility companies substitute for coal burning during energy generation. Locally, that translates to Manitowoc Public Utilities reducing greenhouse gasses by 55% while powering community homes and businesses.
Changing the Future
Kaysun’s sustainability culture thrives because we firmly believe that sustainable practices define our operations, mindset, and goals. Along with our commitment to continuous improvement, we build a better future that balances OEM needs, injection molding excellence, and responsible environmental stewardship.
Let’s talk about how we can align to make your next project successful and sustainable. Request a consultation with the Kaysun experts today.
Subscribe
TO OUR BLOG
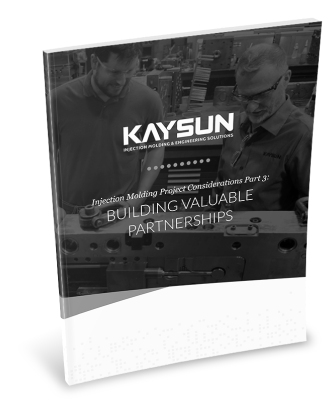
How Do Injection Molder Partnerships Influence Project Costs?
You Might Also Like...
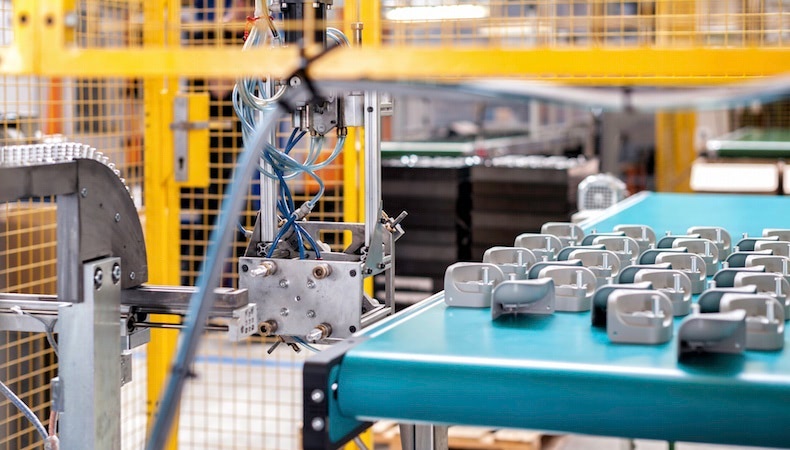
The Impact of Non-Uniform Injection Molding Wall Thickness
Shrink rates for plastic parts vary depending on the materials used and the unifor…
READ MORE
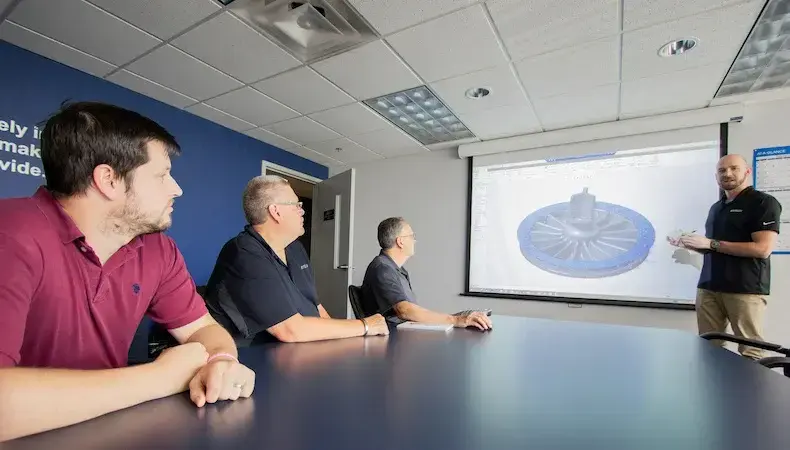
5 Engineering Factors That Improve Your Injection Molding Project
In many complex industries, decisions about which injection molder to use for cust…
READ MORE
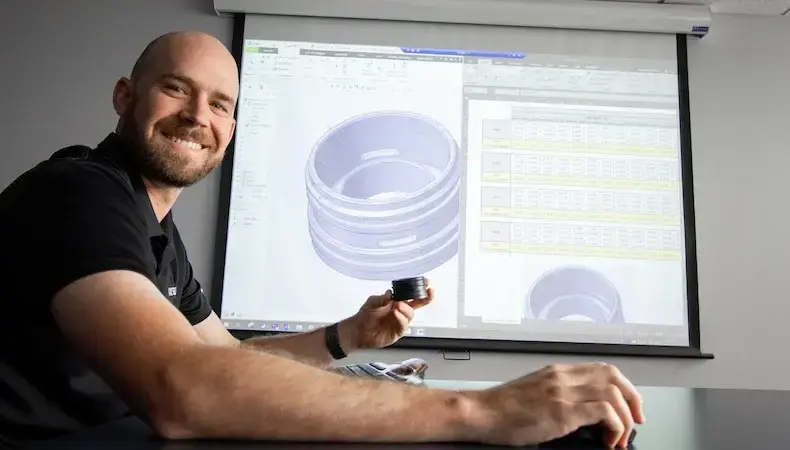
Why Continuing Plastic Engineering Education Matters to OEMs
Technologies, product needs, and customer expectations are rapidly advancing. OEMs…
READ MORE