This is Kaysun: Continuous Improvement Reinforces Quality Outcomes
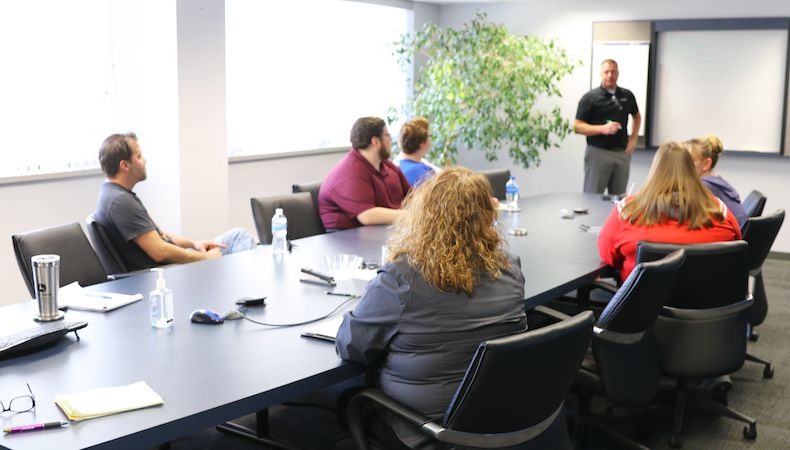
Manufacturing processes can be susceptible to inefficiencies. Continuous improvement practices counteract these shortcomings by proactively identifying and eliminating them, thereby improving process and part quality. In turn, quality parts perform better, longer which is a win-win for the injection molder and OEM.
However, as the name implies, continuous improvement isn’t a one-and-done proposition. Consistency and vigilance is required for effective injection molding continuous improvement processes.
Kaysun is deeply committed to prioritizing continuous improvement throughout our facility. We encourage our employees to observe and learn from their surroundings, and empower them to own and implement changes for the better.
The process behind the injection molding continuous improvement process
Any Kaysun team member can champion change. Cross-functional teams provide balanced problem solving, aided by interactive training that emphasizes the use of a comprehensive suite of continuous improvement tactical tools:
- Lean Leader workshops
- Single-Minute Exchange of Dies (SMED)/Quick changeover
- Managing Daily Improvements (MDI)
- Training Within Industry (TWI)
- Autonomous and preventative maintenance
- Standard work
- Scrap reduction
- A3 problem solving
- 5S housekeeping
- 80/20 Pareto charts
From a tactical tools perspective, it appears continuous improvement is relatively simple to assimilate into everyday activities. The tools are easy to understand and work with, but implementing best practices for long-term success can be trickier.
Aligning continuous improvement with certain aspects of company culture proves beneficial. For Kaysun, we emphasize core values of accountability and innovation, among others, to connect learning with quality standards and the necessity for change to help us — and our partners — grow in positive directions.
Continuous improvement and OEM partnerships
The Kaysun team does more than amass knowledge about injection molding continuous improvement processes. We apply it to our partners’ best advantage.
Some of our OEM partners in automotive, industrial, consumer, and medical markets initially began working with Kaysun because of the quality and delivery challenges they encountered with other suppliers. In 2018, a potential partner transferred a project to Kaysun and quickly discovered the added value of our focus on continuous improvement.
The OEM was struggling with finding solutions to a 29,309 ppm quality reject rating and unacceptable On-Time Delivery (OTD). Kaysun’s cross-functional teams addressed the issues using continuous improvement tools including 5S, standard work, scrap reduction, 80/20 Pareto charts, and A3 problem solving.
The result of Kaysun’s focused injection molding continuous improvement process? A sustained quality reject rate of 399 ppm and a perfect 100% OTD.
Kaysun’s mission is to make the impossible possible. Continuous improvement plays a significant role in both quality injection molding outcomes and how we forge relationships with our OEM partners. Communication and common goals help us understand our partners’ opportunities and examine how we can improve the process for them and us. Watch our short video An Inside Look at Injection Molding QA/Testing Processes to learn more about the resources, people, and processes needed for proper injection molding testing and quality assurance.
Subscribe
TO OUR BLOG
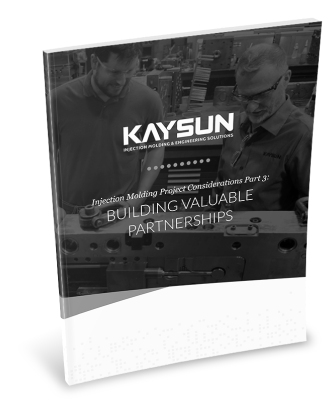
How Do Injection Molder Partnerships Influence Project Costs?
You Might Also Like...
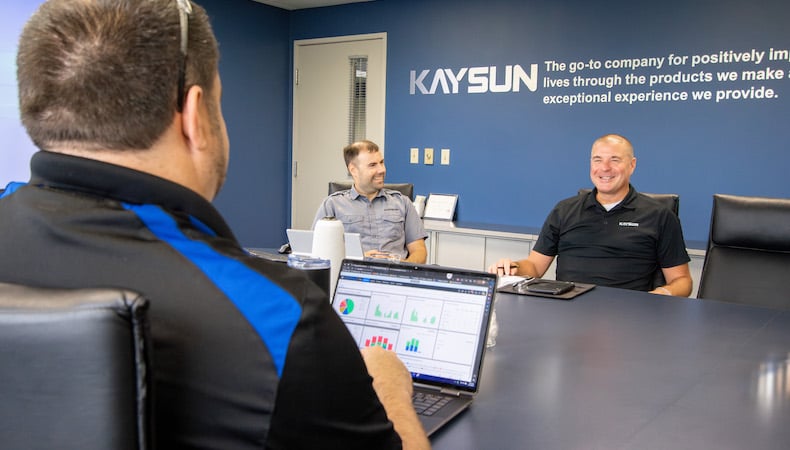
Top 3 Custom Injection Molding Trends to Watch in 2025
Despite being considered more energy efficient and producing less waste than other…
READ MORE
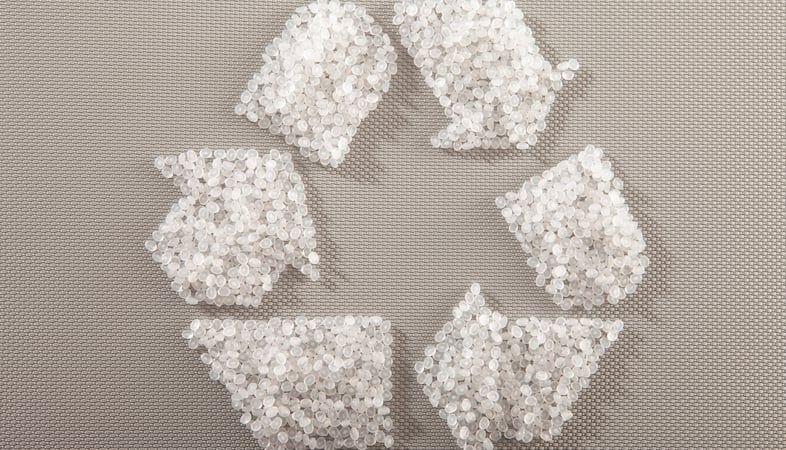
How Kaysun’s Culture of Sustainability Benefits OEMs and The Planet
Injection-molded parts and products are staples for OEMs in industries ranging fro…
READ MORE
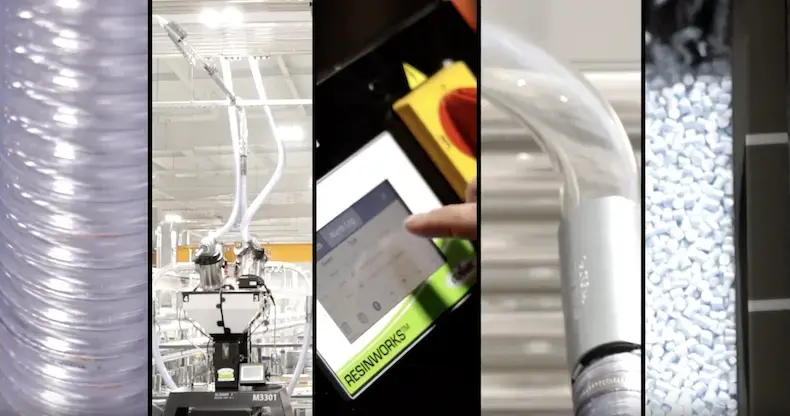
How Centralized Material Handling Streamlines Injection Molding
We consistently look for new ways to deliver timely service and top-quality parts …
READ MORE