Avoiding Hoop Stress and Other Challenges During Insert Injection Molding
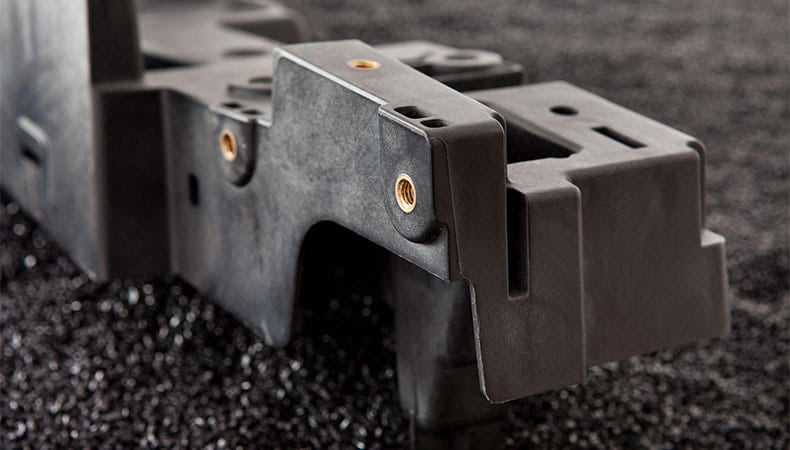
Insert injection molding is a process that requires an insert — typically metal — to be pre-placed in the tool for injected plastic to flow around. Encapsulating the metal insert with plastic creates a single molded plastic piece that’s generally stronger than one created using secondary assembly.
Insert molding can be accomplished through two methods:
- Manual metal insert loading: The generally more cost-effective way to approach very low-volume applications or extremely complex part geometries
- Automated metal insert molding: A better choice for part consistency. It minimizes human error, improves efficiencies, and ensures optimal cycle times.
Securing an insert in plastic requires precision and a thorough knowledge of how each individual substrate reacts to conditions during the injection molding process.
Use of Metal Inserts in Injection Molding
Inserts are typically hard plastic or metal, such as stainless steel. While there have been many advancements in resins to improve performance, metal parts are often preheated before inserting them into the tool because:
- Pre-heating minimizes the quenching effect when the plastic encounters the very thermally conductive metal, which will draw heat from the plastic, increasing its viscosity around the insert
-
The metal inserts are pre-expanded by the pre-heat and shrink with the plastic during cooling, which minimizes molded-in stress levels
-
Knit line strength is improved since the plastic is not quenched
Regulating temperatures during the insert injection molding process is critical. Thermal conditions that are too low or too high can both adversely affect outcomes.
Effect of Hoop Stress on Plastic Components
Engineering “homework” must be done up front (during part design) to calculate the expected hoop stress due to plastic shrinkage. Imagine a wooden barrel with metal hoops around the outside. These hoops are added to prevent the barrel from bulging outward. As pressure in the barrel increases, the hoops are stretched circumferentially.
Likewise, the melted plastic surrounding a metal insert will shrink as it cools, producing a “hoop” stress in the plastic. This hoop stress will be a constant stress on the plastic part throughout the life of the product and possibly result in cracking if the stress is not minimized during the production process.
If plastic injection molded parts are loaded with a constant force/stress, they will stretch or creep over time. The larger the force/stress, the faster the stretch/creep will occur. Over a prolonged period of time the plastic molecules simply cannot sustain the load and will rupture.
Creep rupture charts are created — based on loading and time to rupture — so that failure points can be predicted. These are also calculated at various temperatures since plastics behave differently at different temperatures. A creep rupture chart should always be consulted to determine the maximum strain/shrink rate, followed by the design of an insert-surrounding plastic hub that will control hoop stress and creep.
To learn about high-temperature plastics for your next project, be sure to read our Processing High-Temperature and Engineered-Grade Resins Whitepaper.
Subscribe
TO OUR BLOG
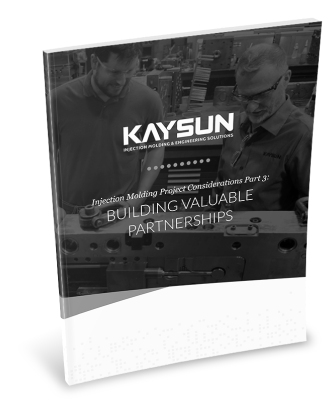
How Do Injection Molder Partnerships Influence Project Costs?
You Might Also Like...
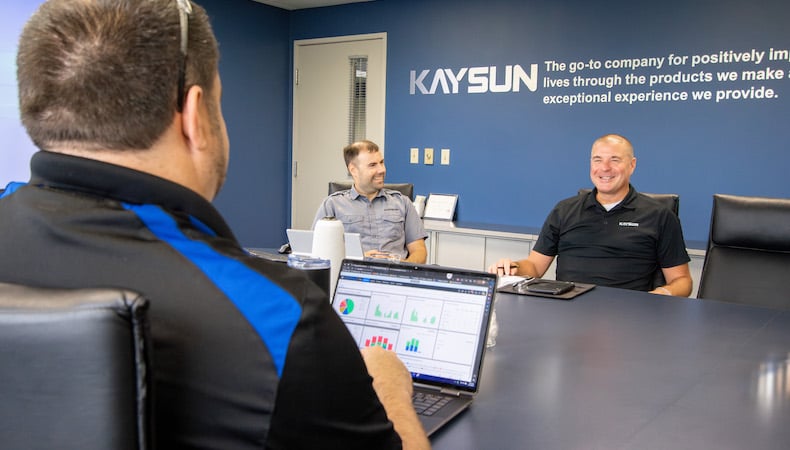
Top 3 Custom Injection Molding Trends to Watch in 2025
Despite being considered more energy efficient and producing less waste than other…
READ MORE
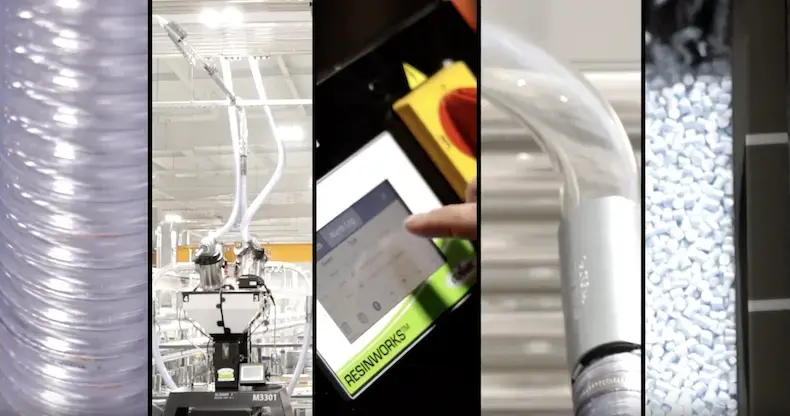
How Centralized Material Handling Streamlines Injection Molding
We consistently look for new ways to deliver timely service and top-quality parts …
READ MORE
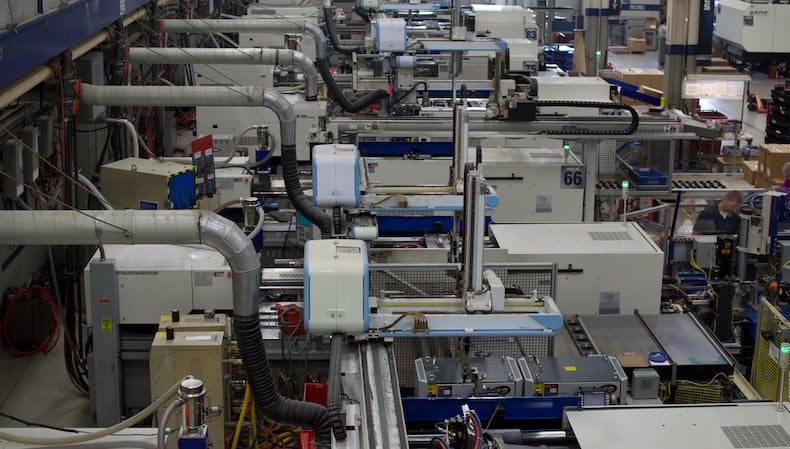
Top 14 Benefits of Injection Molding
OEMs across many industries enjoy the benefits of injection molding. It’s ideal fo…
READ MORE