Advancements in Resins Impacting Product Design
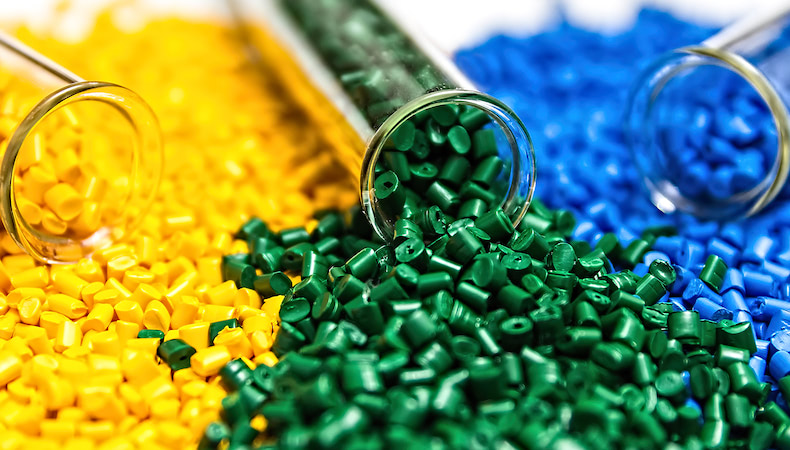
Polymer science has made tremendous strides over the years, rapidly advancing the ability to compound a variety of resins with fillers and reinforcements that provide a vast amount of structural and chemical integrity.
Proper material selection paired with design optimization means plastics can be as strong as metal and weigh far less. Additionally, plastics provide manufacturers with the opportunity to work with more than 25,000 engineering grade resins for wide-ranging industrial applications, which also means choosing the right material can take some time, depending on the project, expertise of your injection molding partner, and desired outcome.
Considerations for Selecting Resins
A molder’s in-depth materials expertise combined with your detailed design knowledge in the following areas will guide you to the most efficient, cost-effective, and performance-appropriate resins and processes for your industrial applications:
Project Specs
The first step in resin selection has less to do with materials than it does with knowing the ins-and-outs of your application. Understanding exactly what the component will be exposed to and must withstand within a system will help you identify and prioritize the needed resin properties such as strength, rigidity, and appearance — along with factors like chemical, temperature, impact, and flame resistance.
When discussing your product design with an injection molder, ask and answer these questions:
- What is the expected physical load for the product?
- What is the mechanical function?
- Will the product be used under conditions of fluctuating and extreme temperatures?
- Will there be any exposure to chemicals?
- Will dissimilar materials be used?
- Does the part require high-heat resins?
Using this information, an injection molder can help align materials with your needs.
Consider the manufacturer, for example, that decided on using polyether ether ketone (PEEK) for a product because of its ability to withstand high temperatures. The injection molder identified complications that would arise in production because PEEK is not as fluid as other resins. Design changes were made that accommodated both the particular resin and moldability, resulting in a successful, durable solution.
Resin Attributes
Evaluating your project needs will narrow the breadth of materials appropriate for the job, but a resin’s attributes will determine the correct material for the job. There are several attributes to consider, including durability, tight tolerance, high temperature, and conductivity:
Durability
Durability determines a product’s ability to withstand wear, pressure, or damage, such as in the case of rugged electronic equipment that must perform in challenging real-life conditions and survive impact, shock, and vibration.
Elastomeric polymers can be added to a resin-melt to increase impact resistance. Because these additives are elastic in nature, they deform upon impact without failing, and then recover their original shape even after stretching, compression, or twisting — an ideal solution for products that face these risks, such as device housings or mounting structures.
Almost all elastomeric materials bend under impact at low hardness levels, but they tend to become more brittle as they are engineered for higher hardness. Polyurethane elastomers retain the most flexibility and are a good choice when design specifications require high hardness in addition to ruggedness/impact resistance.
Similarly, thermoplastic elastomers can be overmolded on the product exterior to improve impact resistance, and on the product interior to further protect delicate components from shock and vibration.
Tight Tolerance
Different resins can produce inconsistent tolerances for the same part, so sometimes a tradeoff must be made between tolerance expectations and the physical properties of the resin. Holding tight tolerances can be a challenge with many resins because they have different shrink rates and high thermal expansion rates, will absorb moisture, and — in crystalline materials — may continue to grow crystals after the molding process.
While plastic components can be held to tight tolerances in a climate-controlled environment, that doesn’t necessarily mean they will maintain these dimensions as the temperature or humidity levels change. This must be considered when plastics are combined with fillers, must adhere to other material types such as metals, or temperature and humidity levels greatly fluctuate in their end-use environment.
High Temperature
Highly engineered, heat-resistant thermoplastics offer an expanded range of physical characteristics that make advanced industrial applications possible. These characteristics include strength, flexibility, low fire, smoke, and toxicity emissions, along with temperature, chemical, and wear and abrasion resistance.
One of the biggest challenges in using high-temperature resins is that melt temperatures are extremely high — exceeding 700°F in most applications. Molten resins behave differently at high temperatures, introducing the potential for polymer degradation and inferior parts that need to be scrapped.
Conductivity
Plastics manufacturers are developing some unique injection-molding resins that have superior conductivity. These manufacturers use nanotechnology to produce tiny metal fibers and strands that are incorporated into the polymer matrix to influence the performance of the composite material.
Molding Performance
Just like you’re an expert on the intended performance of your applications, experienced complex injection molders have a deep understanding of how resins are expected to perform during production. Molders are specifically trained to control the molding processes and other factors that influence successful outcomes. These include the tool steel used for molding, the necessary injection molding machine size, the moisture content of the plastics (along with its impact on avoiding dimensional problems), and the proper cooling time to prevent negative outcomes such as inconsistent warp.
An Array of New Resin Solutions
The plastics industry has experienced rapid growth since 2015. There have been numerous improvements to the materials, technology, and processes used, benefiting both manufacturers and consumers. In addition to recycled plastics and greener processes, the development of stronger, more lightweight plastics and thermoplastics has been one of the driving forces of growth.
To further explain the growing demand for plastics, let’s look at a few key trends and advancements with specific types of plastic materials and resins:
Thermoplastics
High-performance thermoplastics (HPTPs) and engineering-grade thermoplastics (ETPs) have seen many advancements in strength, quality, and durability over the past few years, sparking an increased demand in numerous markets as a viable replacement for more costly, higher-weight metals. Likewise, HPTPs and ETPs offer more design flexibility for manufacturers, which can often help shorten development time.
From the medical industry to aerospace, automotive, and military applications, many of today’s complex products require high-performance materials, and heat resistant thermoplastics have proven to be an ideal choice. PEEK, for example, is a linear thermoplastic that’s processed at a temperature near 750°F, and offers incredible chemical resistance and mechanical strength.
Thermoplastic materials are often used in simple applications such as commercial washers, seals, and valves; impact-resistant housings and cases; and food-safe applications like milk jugs, bottle caps, and even baby bottles.
Liquid Silicone Rubber (LSR) Thermoset Resins
Not to be confused with a thermoplastic elastomer (TPE), liquid silicone rubber (LSR) has also seen increased use across many applications and industries. Its resistance to high temperatures rivals that of thermoplastics while offering high tear strength, chemical resistance, and biocompatibility.
LSR is often used in parts for circuit board and wire harness materials, electronic interfaces on device keyboards and touchpads, medical implants and devices, and gaskets in consumer appliances.
Carbon Fiber Composites
Manufacturers’ demand for lighter, stronger materials has brought about significant advancements in carbon fiber composites, and as a result, special polycarbonate-based, carbon fiber-reinforced thermoplastics are now being used in a broader variety of applications. The automotive and aerospace industries have been the biggest drivers of increased use, as carbon fiber composites are about 40% lighter than the typical materials, and offer significant fuel savings advantages. Despite being half the weight of steel, carbon fiber composites have shown to be four times as strong.
Outside of automotive applications, progress in material science is also making it easier for manufacturers in other industries to incorporate composites into their plastic part designs for everything from medical equipment to airplane fixtures, aerospace components, military equipment and safety gear, electronics, bicycle frames and parts, and even luggage. Carbon fiber composites are now available to OEMs at a relatively low cost compared to similar materials, and can be used in production to shorten cycle times and produce high yield rates.
Further, new technologies are being developed that slash energy use in carbon fiber production by 75%. Technologies have also been developed to reduce the cost of producing carbon fiber so that it’s 50 to 60% less expensive than current competing materials; they are expected to be more widely available sometime this year.
Bioplastics
As the demand for plastics continues to grow, many eco-minded manufacturers are turning to environmentally-friendly bioplastics and recycled plastics to use in their applications, including plastics derived from natural materials like corn starch, soy, and seaweed. In fact, the global market for bioplastics is predicted to grow by 20% over the next five years, fueled by stronger policy support and increased consumer awareness and demand for more sustainable products and packaging.
Biopolymers like polylactic acid (PLA) and polyhydroxyalkanoates (PHAs) are key drivers of demand, along with bio-based, non-biodegradable plastics like polyethylene (PE), along with bio-based polyamides (PA) and polyethylene terephthalate (PET). While packaging makes up nearly 60% of all current bioplastic applications, improvements to bioplastic quality are allowing it to be more frequently used in textiles, consumer goods, automotive applications, and in the agriculture sector. Future bioplastics will perform more like today’s conventional plastics, and have even less environmental impact than they currently offer.
Bioplastics are commonly used in the food and packaging industry, electronic device casings and parts, automotive parts and panels, wearable devices, and personal hygiene products.
Though the resin options are virtually limitless for OEMs today — and can provide numerous advantages to applications — plastics research will continue to develop new compounds. While the sheer number of choices can be overwhelming, when the injection molder and OEM ask the right questions, they can make decisions that lead to manufacturing plastic parts and components that meet the needs of the marketplace as a whole. Our comparison infographic, Thermoplastic Elastomer (TPE) v. Liquid Silicone Rubber (LSR), demonstrates how materials insights and characteristics are applied in determining the best resin for a project. Click the button below to access your copy now.
Subscribe
TO OUR BLOG
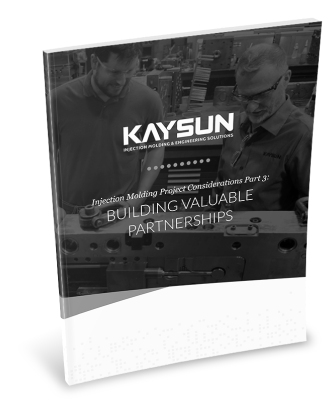
How Do Injection Molder Partnerships Influence Project Costs?
You Might Also Like...
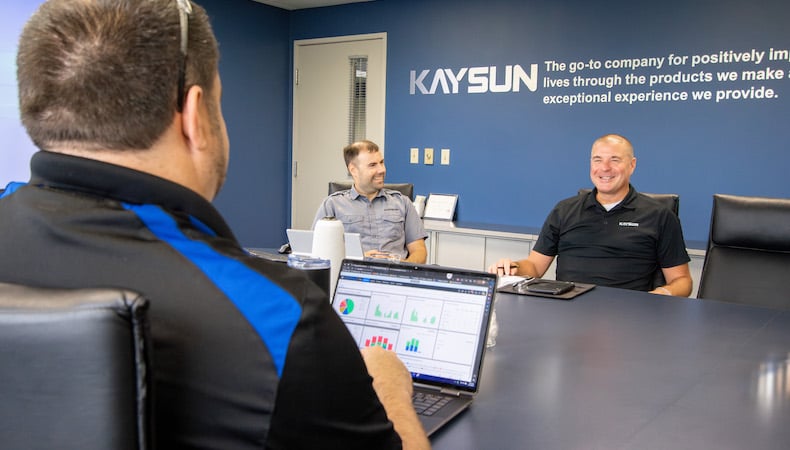
Top 3 Custom Injection Molding Trends to Watch in 2025
Despite being considered more energy efficient and producing less waste than other…
READ MORE
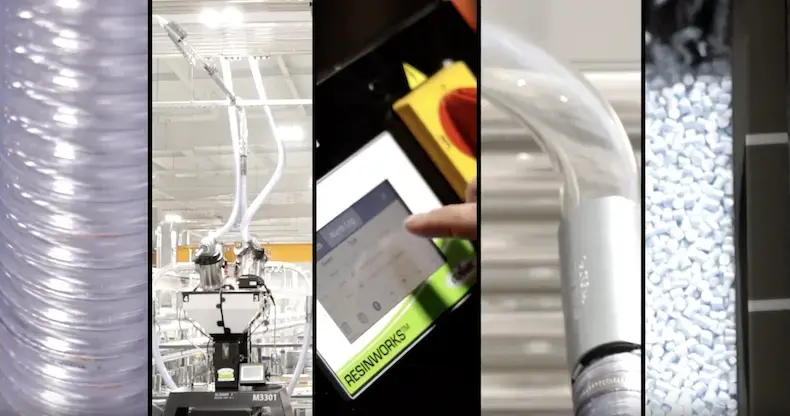
How Centralized Material Handling Streamlines Injection Molding
We consistently look for new ways to deliver timely service and top-quality parts …
READ MORE
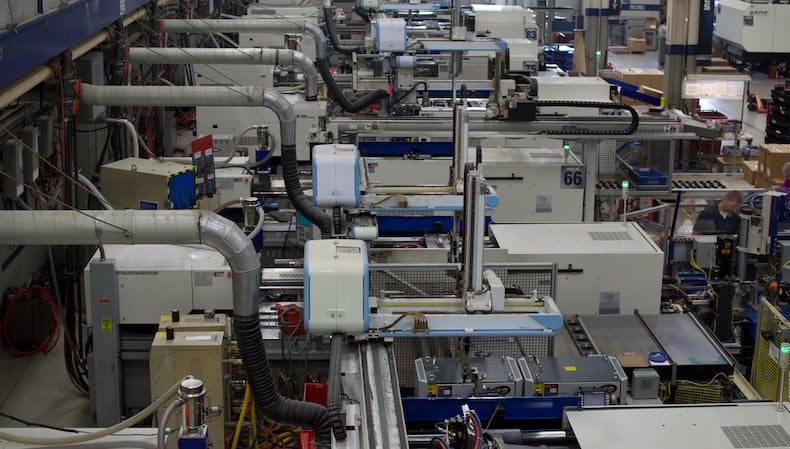
Top 14 Benefits of Injection Molding
OEMs across many industries enjoy the benefits of injection molding. It’s ideal fo…
READ MORE