Preventing Common Manufacturing Defects in Medical Applications

Manufacturers of medical devices and other medical applications often turn to a complex injection molder for help correcting defects in their engineered plastic components. At Kaysun, we actively seek to prevent defects before they even occur by using a design for manufacturability (DfM) approach that incorporates a comprehensive mold flow analysis and extensive plastics engineering experience to identify any potential issues in the design phase and determine the best strategy to produce defect-free parts.
If proper DfM and mold flow analysis aren’t utilized by your molder, or if unforeseen circumstances arise that cause defects to occur, there are corrective measures to be taken. Let’s take a look at the impact of the common injection molding defects in medical applications we introduced in Part 1 of this blog series and how experienced complex injection molders troubleshoot them:
Residual Stress occurs because, during molding, the nature of an injected plastic material and the function of the mold are at odds. The plastic wants to shrink organically and the mold restricts that shrinking.
Solution: Generally, residual stress is anticipated and a molder compensates for it by qualifying a part using the same production process and equipment time after time. If a different molder is subsequently used, that molder is responsible for re-qualifying the part and ensuring consistency in their process and equipment to prevent residual stress-related defects. This is one of the primary reasons why you need a molder who practices scientific molding so they can optimize the process and determine a tolerable amount of residual stress to prevent misshapen parts.
Warping is the direct result of residual stress acting on a plastic part that may have been prematurely ejected from a mold before full cooling and solidification. Flawed molds or materials, production changes, or liquid resin being too warm when injected are also potential causes. Freed from properly conforming to the mold, the plastic can act organically and take on a warped shape within minutes or up to 24 hours of coming out of the mold, depending on the material.
Solution: Temperature and timing are critical for warping prevention. Careful monitoring of resin temperatures and keeping them consistent prior to and during the injection process alleviates overheating, compromising of solidification properties and the risk of improper cooling at the end of the process. Likewise, the timing surrounding the release of a part from a mold must be precise to prevent warping. If ejected too soon, the part does not contain appropriate residual stress and is not properly solidified, so the plastic reverts to its natural properties which causes warpage.
Sink Marks indicate a variety of problems, from a dirty mold to changes in material properties and/or equipment pressurization. They can also be a consequence of an adjustment made to correct a separate issue within the molding process that then interferes with residual stresses.
Solution: Prevention of sink marks can range from minor fixes, like cleaning a dirty mold, to more complex solutions that start in the design phase — such as proper gate location, wall thickness and other potential design challenges revealed through mold flow analysis. Incorrect machine pressure could also be the culprit. Checking and calibrating the machine may resolve sink mark issues, but that could also mean deviating from the scientific molding process and create the need for re-qualification.
Short Shots are caused by a mold cavity being improperly filled with plastic, either through not having enough material, faulty flow or incorrect pressurization.
Solution: Short shots are avoided or resolved by maintaining the ideal pressure rate to fill out the part, as determined during the scientific molding analysis. As in other aspects of production, a moldflow analysis provides feedback that engineers can use to adjust pressures and ultimately deliver fully filled, defect-free injection molded parts for medical applications.
Flash can result from general tool wear, or when an undersized press cannot produce the force required to push the two halves of the mold together during the high-pressure fill, and the mold separates to varying degrees at the parting line.
Solution: Tooling issues and flash go hand in hand. Therefore, expert tool design is fundamental — and largely dependent upon molder engineering expertise and experience. Tooling developed based on a solid design concept and detailed specs, and backed by advanced knowledge of scientific molding practices, alleviates the tool locking issues that generally lead to resin leaks and flash during production. In addition, it’s crucial that your molder correctly calculates tonnage in order to use the right size injection molding machine to prevent flash.
Using a complex injection molder with deep engineering knowledge and experience in scientific molding practices is your best line of defense for preventing — and fixing — common injection molding defects for critical-use applications like medical devices. Learn more in Designing Plastic Parts and Products for Critical-Use Medical Applications. Click the button below to download your free copy.
Subscribe
TO OUR BLOG
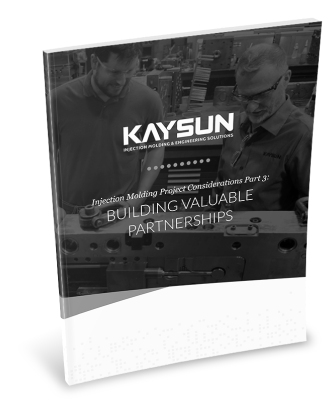
How Do Injection Molder Partnerships Influence Project Costs?
You Might Also Like...
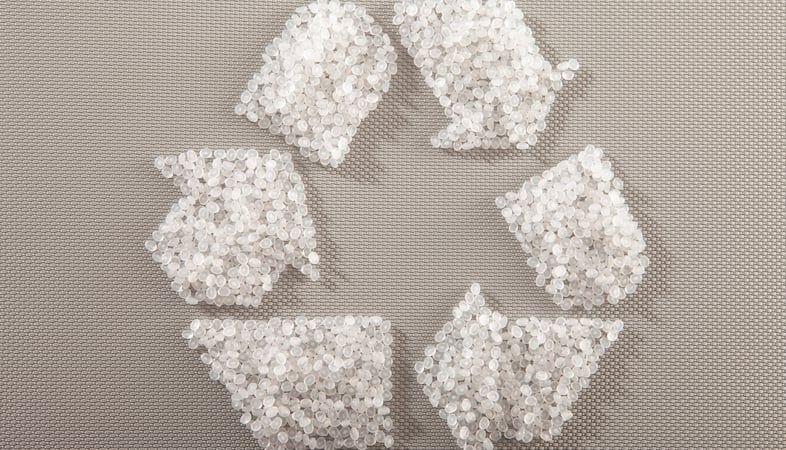
How Kaysun’s Culture of Sustainability Benefits OEMs and The Planet
Injection-molded parts and products are staples for OEMs in industries ranging fro…
READ MORE
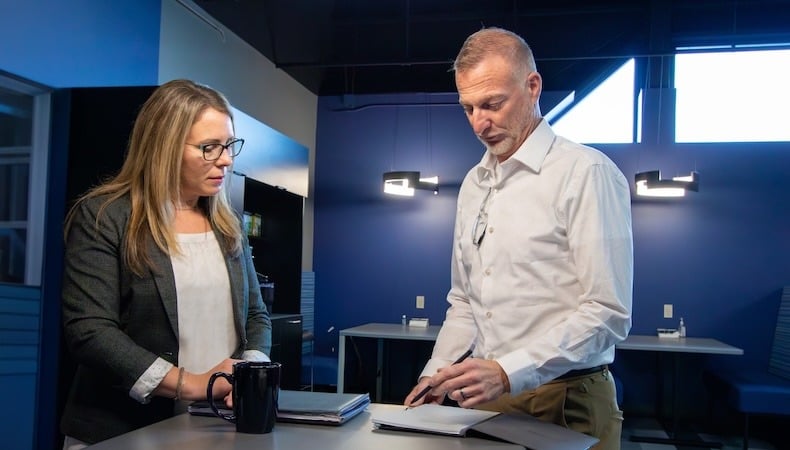
12 Common Injection Molding Questions — Answered!
Injection molding is a versatile and precise process, making it ideal for OEMs tha…
READ MORE
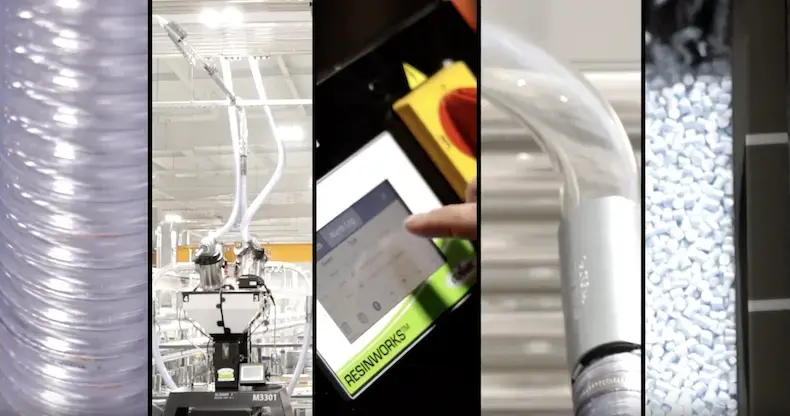
How Centralized Material Handling Streamlines Injection Molding
We consistently look for new ways to deliver timely service and top-quality parts …
READ MORE