Insert Injection Molding: How to Ensure Consistent Outcomes
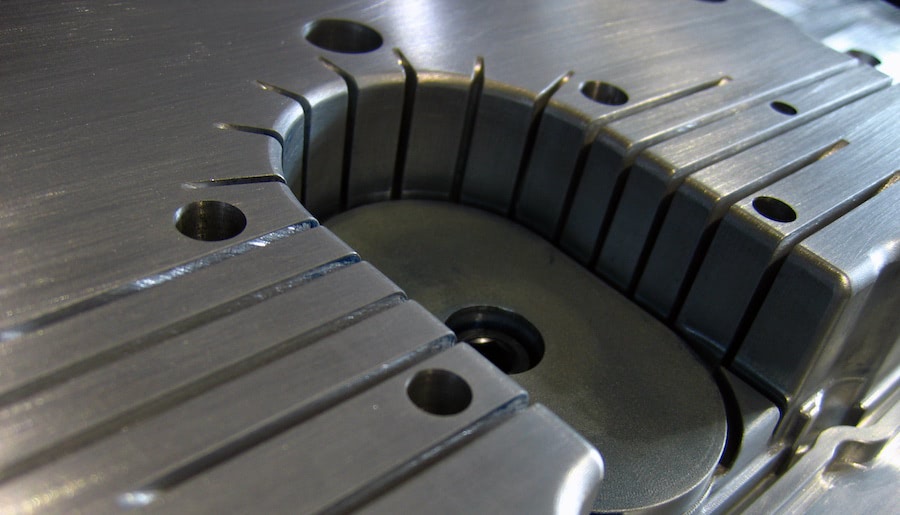
Insert molding is one of several injection molding processes that can provide effective solutions for a wide range of design and production needs.
Whether insert injection molding or another multi-material injection molding technique, such as overmolding, is the best option for you depends on factors including the component’s application, design, materials, and complexity. These factors have implications for consistency in molding across all injection molding processes.
Insert Molding Steps
The first step in insert molding is to custom-build a tool to accept a solid component or part as an insert. That insert is placed into the tool, and a thermoplastic elastomer (TPE) is injected into the tool cavity, coating the insert in a smooth layer of plastic. After cooling, the tool is opened and the part is removed and inspected.
The insert can be a single part or component, or a combination of individual components that are carefully configured inside the tool and then sealed together with the plastic during the insert-molding process.
This method of insert injection molding can actually result in greater strength, flexibility, or functionality, compared to attaching the individual parts separately during post-production assembly operations. Secondary steps can often be reduced or eliminated entirely with insert molding, saving time and reducing production costs.
Suitable Applications for Insert Molding
Many people think insert injection molding is limited to standard compression limiters — metal cylinders that are insert-molded to create plastic-covered parts and are bolted to other components, such as brackets or mounts (the compression limiter maintains the load of bolted joints, preventing plastic creep or hoop stress over time).
However, other components that can be insert-molded include bearings, custom stampings, flexible circuits, and parts made from powdered metal or rubber.
Benefits of Insert Injection Molding
Insert molding provides several cost and design benefits. Sometimes insert injection molding improves manufacturability by replacing some post-tool assembly operations such as snap fits, gluing, and the use of screws or other fasteners. It can also provide some cost savings due to reductions in the number of parts, supplier consolidation, and part tracking and shipping.
Regarding durability, encapsulating a component with plastic using insert injection molding often results in a much stronger part and joint than what could be created through secondary assembly operations.
Injection Molding Automation Improves Consistency
For some, minimizing the risk of part defects while ensuring timely speed to market is a challenge. It is still common in the injection molding industry to manually perform insert molding, requiring operators to load and unload inserts into a horizontal machine. Cycle times can vary drastically from one run to the next, potentially causing variations in thermal conditions and other factors, which can lead to inconsistent insert molding outcomes.
Some injection molders — like Kaysun — use automation technology and both horizontal and vertical machines for insert molding to help minimize human error, improve efficiencies, and ensure optimal outcomes in the injection molding process.
RELATED: Injection Molding Automation in Action [Video]
For example, our vertical machines are ideally suited for loading inserts. We also use automation and end-of-arm tooling to ensure that parts are always inserted correctly. Missing an insert can cause several problems, ranging from downtime or mold damage to quality issues and field failures for the customer. It is essential to have high-precision controls and processes in place to manage the insert molding operation and maximize quality — especially for meaningful and effective Design Failure Mode and Effects Analysis (DFMEA).
People Behind the Insert Molding Process
Each design is different and presents unique insert-molding challenges — especially for loading, holding, and filling around inserts. Loading and holding components can be quite complicated, and that complexity depends on interacting part characteristics and factors such as material, geometry, and function.
The expertise of operators and engineers remains crucial in an age of automation. Creativity and flexibility are often required to develop the best solutions for production challenges and achieve optimal cycle times. Methods that can be used to hold a component can range from clamps to vacuum to magnets, and selecting the most appropriate method requires expertise and experience.
The takeaway: The insert molding process can be highly effective and work with a variety of materials and part geometries. In most cases, it can result in cost savings and design improvements for parts that maximize manufacturability and improve customer satisfaction. To help you determine materials and the factors that need to be considered, such as thermal conditions, chemical exposure, physical loads, and more, view our Rise Above the Competition: Multi-Material Injection Molding infographic below.
Subscribe
TO OUR BLOG
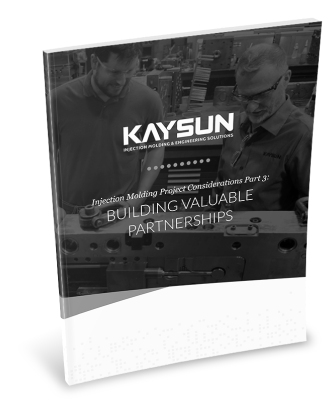
How Do Injection Molder Partnerships Influence Project Costs?
You Might Also Like...
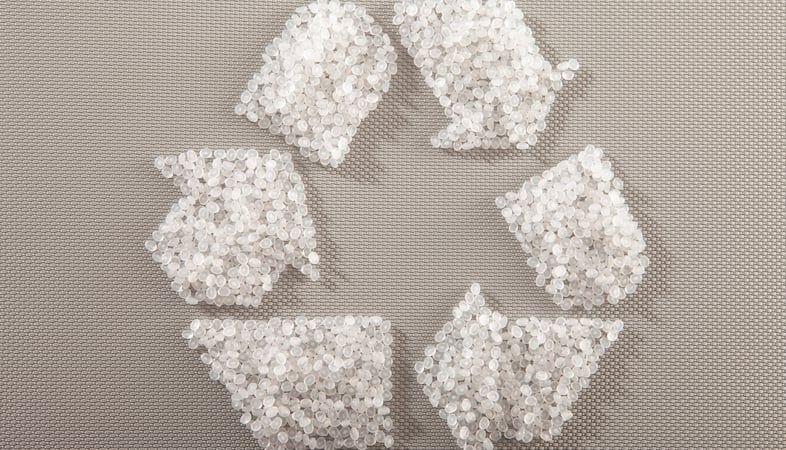
How Kaysun’s Culture of Sustainability Benefits OEMs and The Planet
Injection-molded parts and products are staples for OEMs in industries ranging fro…
READ MORE
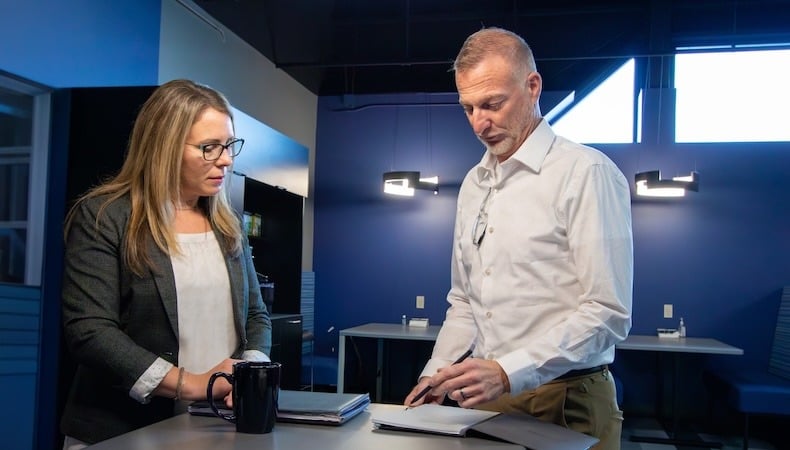
12 Common Injection Molding Questions — Answered!
Injection molding is a versatile and precise process, making it ideal for OEMs tha…
READ MORE
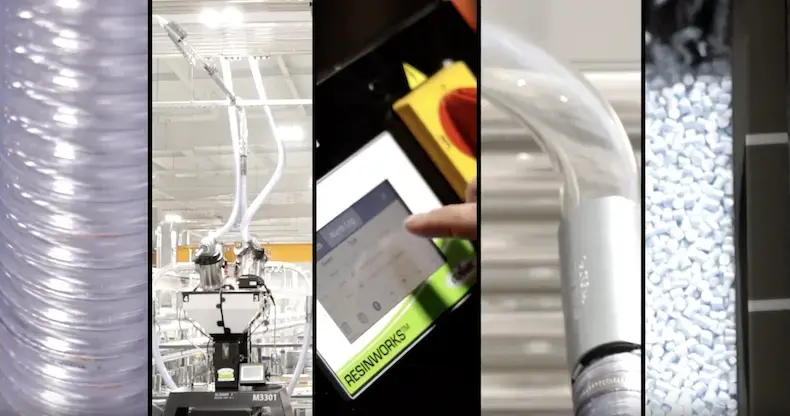
How Centralized Material Handling Streamlines Injection Molding
We consistently look for new ways to deliver timely service and top-quality parts …
READ MORE