Kaysun Integrates AI on the Production Floor with RJG CoPilot
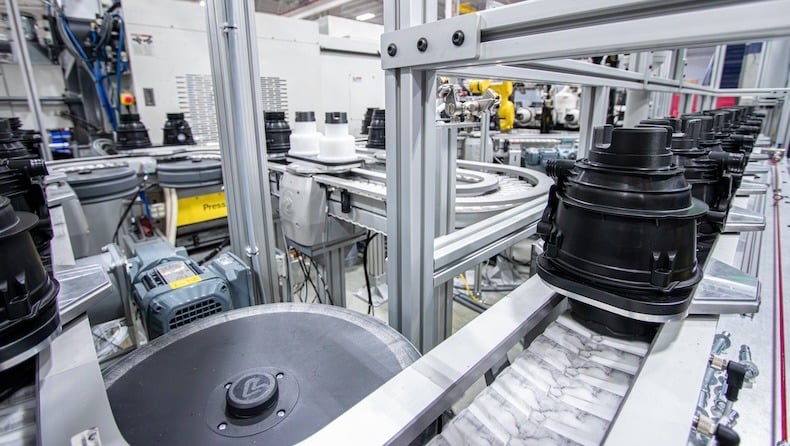
Industry 4.0 has made manufacturing more dynamic than ever before. Merging IoT, AI, and big data enables faster, more accurate, and more efficient production based on data-driven decisions. Along with progress typically comes a need to modernize and optimize technologies.
In the injection molding industry, the advancements impact the RJG Inc. eDart process control system. For a little over two decades, the vast majority of molders — including Kaysun — have relied upon eDart for monitoring injection molding processes and controlling key variables such as pressure, temperature, and fill rates.
The trusted system is still in place on many production lines, but RJG is phasing eDart out in favor of the new, more powerful RJG CoPilot and The Hub systems by 2030.
As industry leaders and early adopters, Kaysun has already implemented a plan to transition to CoPilot and The Hub in stepped intervals. In mid-2024, we purchased five CoPilot systems, five more are slated for 2025, and the balance of the 47 lines currently operating eDart will be upgraded by RJG’s 2030 deadline.
It’s not technology for technology’s sake. Our incremental CoPilot integration helps us strategically future-proof our injection molding operations to enhance production efficiency, reduce scrap, and maintain the highest quality standards.
As part of the team overseeing the CoPilot project, I have the firsthand opportunity to understand and experience the platform’s capabilities, and want to share what these enhancements mean for our customers.
Getting to Know RJG CoPilot and The Hub
RJG CoPilot is a next-generation process monitoring system. It uses AI to amplify data integration and predictive analytics to ultimately align injection molding capabilities with the demands of modern manufacturing.
Where eDart is reaching its technological limits, CoPilot provides:
- A more powerful data platform that, when combined with The Hub centralized data management system, can track production data to ensure real-time monitoring and historical traceability
- Improved machine-tooling compatibility by proactively suggesting the best machine for the tool, eliminating guesswork, and aiding in faster production cycles
- AI-driven process control through smarter alarm bands and analytics that gives molders the advantage of quickly identifying and correcting process deviation
The Hub is the Brains Behind Smart Manufacturing
The CoPilot system collects and monitors data. The Hub is a platform that works alongside CoPilot to store, monitor, analyze, and provide real-time centralized access to that molding process data.
The Hub acts as the CoPilot “brain,” allowing injection molders to:
- Manage production in real time for immediate insights into molding processes
- Store historical data for comprehensive traceability, audits, and defect analysis as granular as production run dates and specific batch information
- Access and run reports on key performance metrics using easy-reference dashboards to optimize efficiency and minimize downtime
- Seamlessly integrate CoPilot and The Hub with other smart manufacturing and ERP/MRP systems to optimize operations
MAX and the Future of Injection Molding
CoPilot and The Hub are Kaysun’s primary systems right now, but we expect MAX to be a key platform in the future as it grows to support all of Kaysun’s scientific molding needs. As an AI-powered process advisor, MAX acts as a virtual mentor supporting CoPilot and technicians on the production floor.
MAX identifies process deviations. When one occurs, MAX uses on-screen prompts to alert technicians and gives them step-by-step recommendations for adjustments. This virtual coaching gives less experienced technicians confidence to correct most issues without full reliance on engineering support, maximizing team productivity and enhancing overall process stability.
Training to Maximize CoPilot’s Capabilities
A new system requires skilled technicians to make full use of its capabilities, and Kaysun is committed to investing in our people.
Kaysun technicians, machine operators, process engineers, and Master Molders attended a 3-day intensive CoPilot training program consisting of classroom learning and hands-on exercises. The insights and experience our team gained adds more depth to the Kaysun knowledge base and adds value to our partnerships.
4 Benefits of CoPilot and The Hub
Thinking of CoPilot and The Hub as complete molding process optimization — not just a monitoring system — creates a clear link between analytics, operations, and results.
Real-time data analysis gives Kaysun a number of advantages that strengthen continuous improvement initiatives and make operations more efficient. For customers, it translates to:
1. Enhanced product quality and consistency
One of the biggest challenges in injection molding is process variation, which can lead to defects such as short shots, flash, sink marks, and warpage. RJG CoPilot provides real-time process monitoring and automated quality control, ensuring every part meets exact specifications.
For our partners this means:
- Fewer quality concerns and delays because of defects
- Cost savings and responsible environmental stewardship due to less scrap
- Greater confidence in part consistency and performance in the market
2. Faster issue resolution and improved traceability
Quality control doesn’t end when a part leaves the molding machine. If an issue arises in the future, Kaysun’s ability to trace production data back to its source is crucial for fast troubleshooting and corrective actions.
For our partners this means:
- Less downtime and greater productivity
- Reduced supply chain disruptions to streamline program flow
- Stronger quality assurance including compliance with regulatory standards
3. More reliable and predictable production schedules
One of the biggest frustrations in manufacturing is unexpected delays due to equipment failures or inconsistent production runs. CoPilot minimizes these risks by improving process reliability and enabling better machine-tooling matching for optimal efficiency.
For our partners this means:
- On-time deliveries that meet critical deadlines
- Fewer production holdups for time and cost savings
- Better supply chain planning to simplify program management
4. Lower costs and reduced waste
Scrap and rework are among the biggest cost drivers in injection molding. CoPilot helps minimize waste by ensuring optimal materials use, reliable and accurate processes, automated quality assurance, and low part rejection rates.
For our partners this means:
- More competitive pricing in the market
- Minimal risk of costly quality failures and product recalls
- Improved sustainability through scrap and waste reduction
Advancing Partnerships, Supporting Partners
Kaysun’s transition to RJG CoPilot and The Hub isn’t just a technology upgrade — it’s a commitment to delivering exceptional results to our customers. By adopting these advanced molding process monitoring systems, we help ensure:
- Top-quality, defect-free parts
- Faster turnaround times with fewer delays
- Reliable and predictable production
- Lower costs and improved efficiency
- A competitive advantage in complex injection molding
Many manufacturers depend on sophisticated and often custom injection molding solutions. Working with a molder that is proven in the industry and invests in cutting-edge process control means fewer risks, better products, and stronger supply chain confidence.
Learn more about how RJG CoPilot and The Hub directly benefit your programs and bottom line. Schedule a consultation with our experts to get the answers and information you need to achieve your goals.
Subscribe
TO OUR BLOG
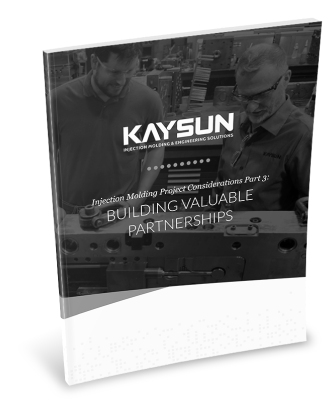
How Do Injection Molder Partnerships Influence Project Costs?
You Might Also Like...
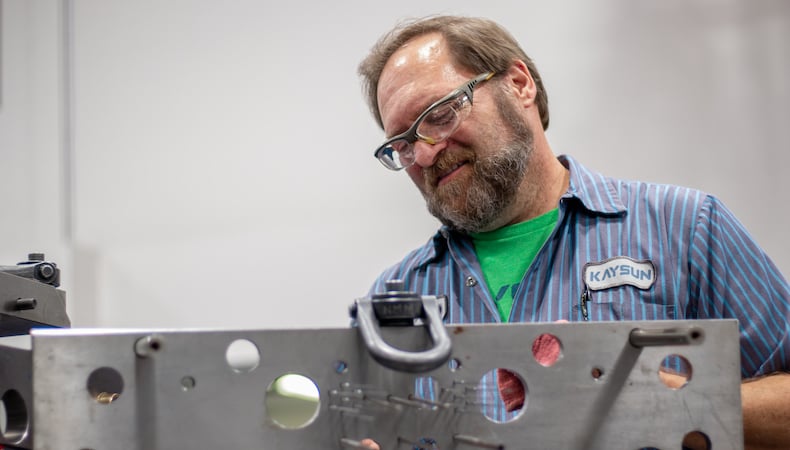
Injection Molding Quotes: 5 Tips to Help Get Tooling Right
Few things impact injection-molded part quality as much as tooling design, materia…
READ MORE
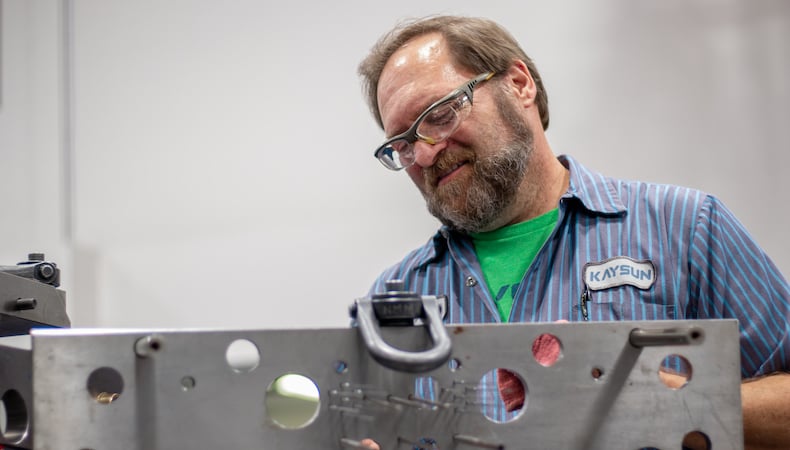
Tooling Audits & Evaluations: How Molders Help OEMs Gauge Health of Assets
When an OEM pursues an injection molding program, tooling is among the most highly…
READ MORE
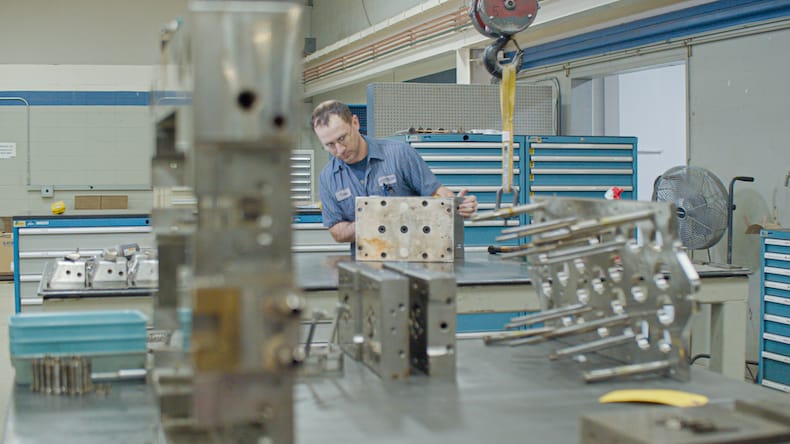
How Concurrent Design Review Aligns Injection Molding Tooling and Parts [VIDEO]
Tool design is an essential and sometimes underestimated part of injection molding…
READ MORE