Tight Tolerance Molding and Product Design
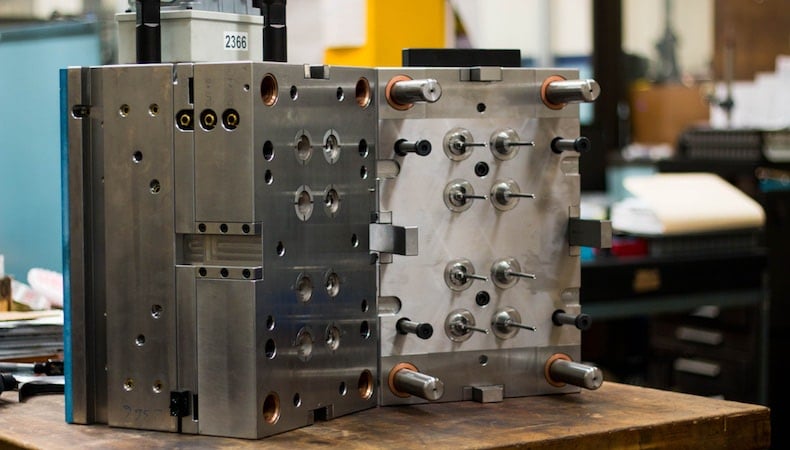
There are many factors that impact injection molding tolerances—all of which need to be controlled with precision to meet final part specifications. The greater the number of factors, the harder it is to achieve tight tolerances consistently. That’s why it is so important to consider tight-tolerance requirements during the plastic part design process, where factors can be addressed through design modifications without impacting quality or performance. In fact, working with an experienced injection molder like Kaysun could actually result in even tighter tolerances, if needed, through expert alignment of design, materials, tooling and production process parameters.
Product Design and Tight Tolerances
Product design is the single biggest factor in controlling tight tolerances. Making improvements during the design phase will not only achieve repeatable tight tolerances but also improve manufacturability, quality, and customer satisfaction—all while reducing costs. Selecting who gets involved in design, then, is critical for overall project success.
Product designers seem like a natural choice, but few have in-depth injection molding experience. They know the basics, but usually not enough to oversee when and how injection molding gets factored into the design and production process.
Similarly, companies sometimes contract a design house for their products. This option can work, but more often than not, the design house focuses on visual appeal of the final product and cost, with ease of manufacturing and tolerance specs being afterthoughts.
Knowing "the basics" or focusing on aesthetics often results in flawed designs that complicate production from an injection molding perspective—for example, die lock conditions, poor areas of fill with abrupt changes in wall thickness, sharp corners, and impossible tolerances. This doesn’t happen with an experienced injection molder like Kaysun. Our 60-plus years of experience in tight tolerance injection molding gives us a thorough understanding of tolerance limits and how to support product design to make specified tight tolerances a reality.
Right Questions, Right Design
Before forging ahead with a plastic part design containing tight tolerances, an experienced injection molder will take the time to explore all aspects of the design, asking specific questions that could impact the degree of injection molding tolerance identified:
Is tight tolerance necessary for part performance, longevity, or appearance?
Many designers automatically set a tolerance in the CAD drafting software and all dimensions are toleranced to that number, when in reality the product may not need such a tight tolerance. Achieving tight tolerance is a more expensive process, so if it not required, loosen it up to reduce production costs.
What is the size of the part?
Physical part size also affects tight tolerance capability. Large parts are difficult to hold to tight sizes consistently. Local areas within the large part, however, are easier to manage and can be dimensioned accordingly from a local datum. Plastic material manufacturers also have charts to assist with choosing appropriate tolerance based on part size and wall thickness.
How will material type influence plastic behavior and tolerance?
Plastics typically have large thermal expansion coefficients; as a result, tight-tolerance parts may have to be measured at a consistent temperature. For example, crystalline plastics tend to shrink more (move away from tolerance) as time goes on because they become more and more crystalline. This is especially true with acetal-type plastics. This shrinkage also occurs when plastics are exposed to an environment that promotes crystal growth, such as high temperatures. Also, if these plastics are molded in cold molds that don’t allow much initial crystal growth, the tendency for this growth is stronger than if a plastic was molded in a hot mold. These points all need to be considered when selecting materials and mold processing.
Will temperature and part wall thickness variations impact outcome?
Temperature is important to consider during design. If the tight-tolerance part will be exposed to high/low temperature extremes in normal operation, it may expand or contract in such a way that tight tolerance is not necessary. Likewise, variances in part wall thickness can create uneven crystallinity that needs to be accounted for (i.e., some plastic parts—especially those made from nylon—lose some of their tight tolerance when they leave a tightly controlled atmosphere and are used in environments with a higher moisture content).
Asking and answering these questions early on during the design phase is critical for quality outcomes. So is getting an experienced injection molder partner like Kaysun involved to leverage plastics engineering expertise and advanced capabilities, like our in-house tooling, that aide in the achievability of tight tolerances.
For more, read our whitepaper, Tight Tolerance is Critical for Top Quality and Superior Performance. Click the button below to access your free copy.
Subscribe
TO OUR BLOG
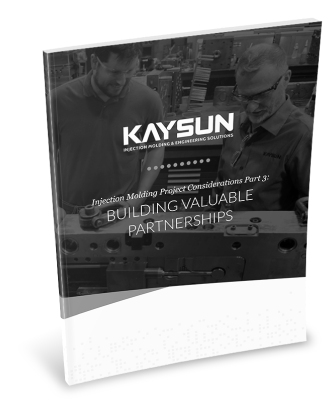
How Do Injection Molder Partnerships Influence Project Costs?
You Might Also Like...
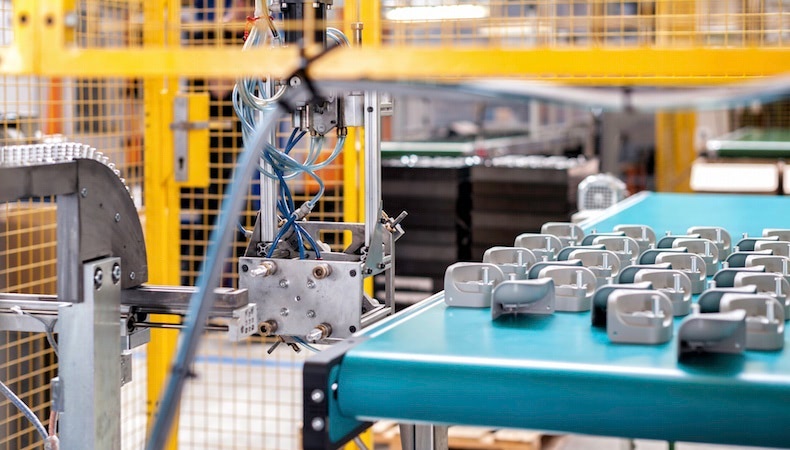
The Impact of Non-Uniform Injection Molding Wall Thickness
Shrink rates for plastic parts vary depending on the materials used and the unifor…
READ MORE
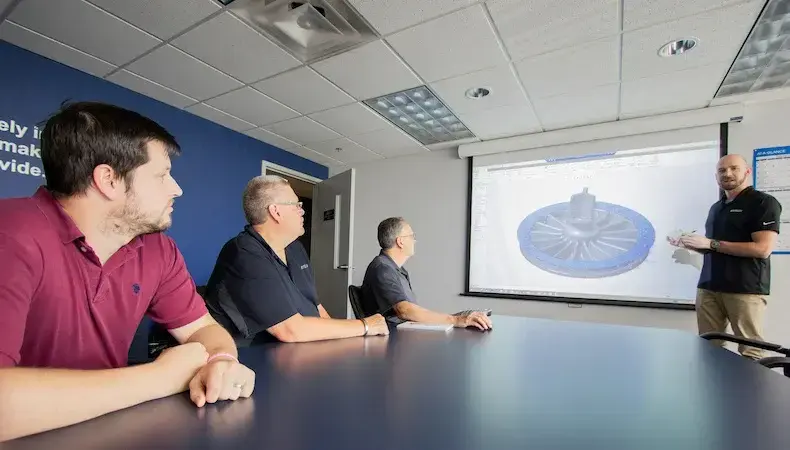
5 Engineering Factors That Improve Your Injection Molding Project
In many complex industries, decisions about which injection molder to use for cust…
READ MORE
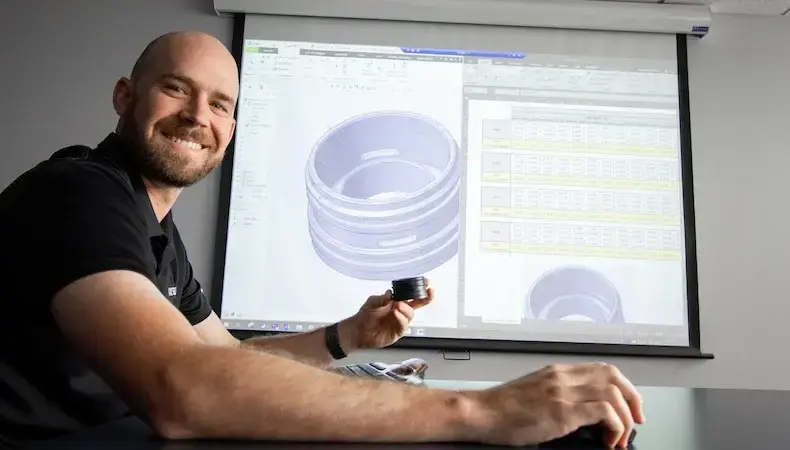
Why Continuing Plastic Engineering Education Matters to OEMs
Technologies, product needs, and customer expectations are rapidly advancing. OEMs…
READ MORE