The 5 Types of SPI Mold Classifications and Standards
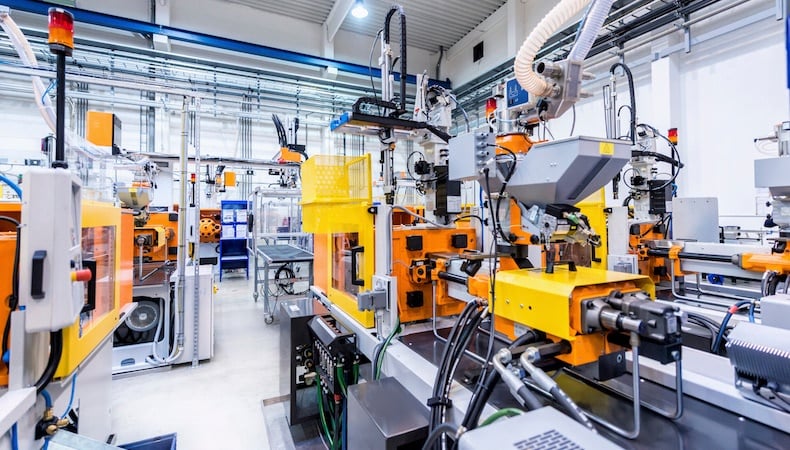
The first step when you approach a custom injection molder to produce complex plastic parts or components is determining if the product is suitable for a streamlined injection molding process
Experienced injection molders ask questions to better understand your project needs from multiple perspectives: design, purpose and objectives. First to determine overall moldability, and then to confirm the best type of mold. Mold classification helps determine the correct mold type and is crucial to achieving quality, production and cost objectives.
The Plastics Industry Association (formerly known as the Society of Plastics Industry or SPI mold classifications) has mold standards categorized into five classifications to guide quotes and orders into uniform mold class types:
Cycles |
Production level |
Uses |
Investment |
|
Class 101 Mold |
1 million or more | Extremely high | Extremely high production and fast cycle times | Class 101 molds are the highest priced and made with only the highest quality materials |
Class 102 Mold |
Not exceeding 1 million | Medium to high | Good for parts with abrasive materials and/or tight tolerances | Class 102 molds are fairly high priced and made with materials of high quality |
Class 103 Mold |
Not exceeding 500,000 | Medium | A very popular mold for low to medium production parts | Class 103 molds fall within common price ranges |
|
Not exceeding 100,000 | Low | Good for limited-production parts with non-abrasive materials | Class 104 molds fall within low to moderate price ranges |
Class 105 Mold |
Not exceeding 500 | Very low | Prototype only | Class 105 molds are built inexpensively to produce a very limited number of product prototypes |
Simply reviewing an injection mold classification chart isn't enough, however, since each mold classification has unique parameters. It’s essential that you partner with a molder that is knowledgeable on these mold standards and the classification spectrum. The molder's guidance can determine the best type of mold that meets your production life, cost and quality objectives.
Because of the complex nature of our customers’ products, Kaysun typically deals with applications that fall within Classes 101 and 102 for long-life production. Yet, our broad-based experience in custom injection molding makes us the preferred choice for consulting on all projects for which high-quality and high-volume tools are required.
Find out how tooling design plays an essential role in achieving desired injection molding outcomes – from the different stages of the tooling process to the key components of tooling design – in our whitepaper, Tooling Design for Injection Molding. Click the button below to download your free copy.
Subscribe
TO OUR BLOG
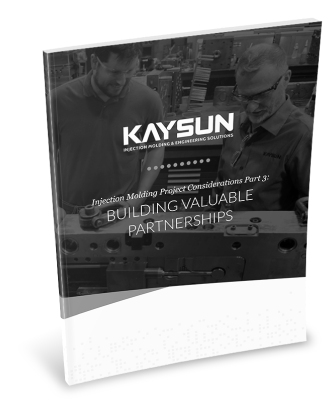
How Do Injection Molder Partnerships Influence Project Costs?
You Might Also Like...
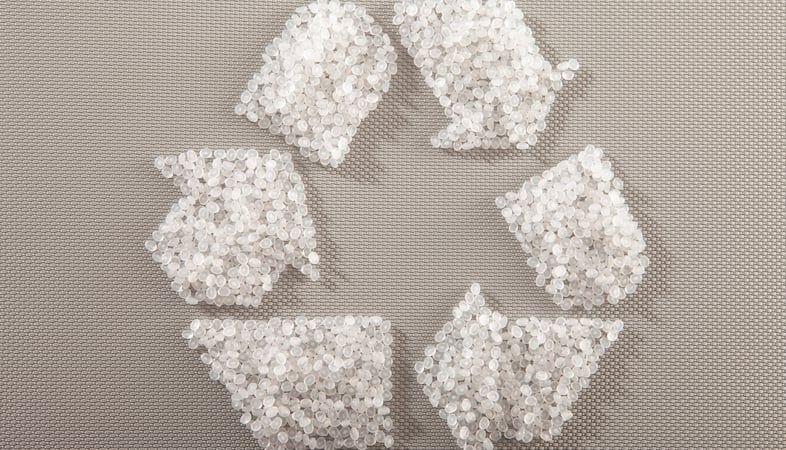
How Kaysun’s Culture of Sustainability Benefits OEMs and The Planet
Injection-molded parts and products are staples for OEMs in industries ranging fro…
READ MORE
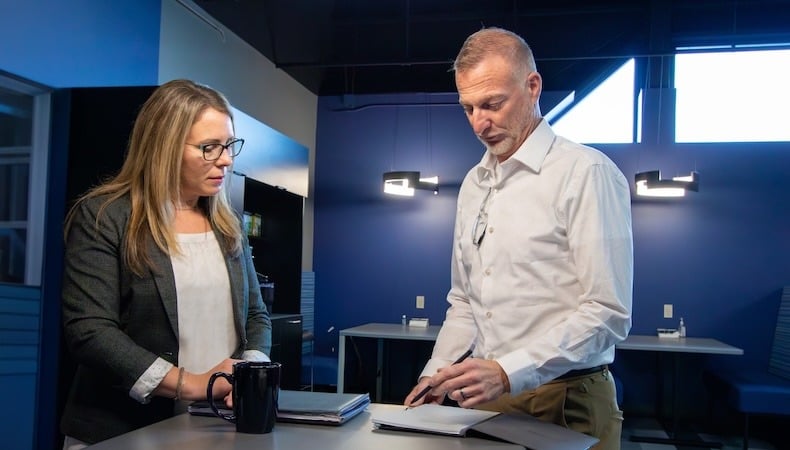
12 Common Injection Molding Questions — Answered!
Injection molding is a versatile and precise process, making it ideal for OEMs tha…
READ MORE
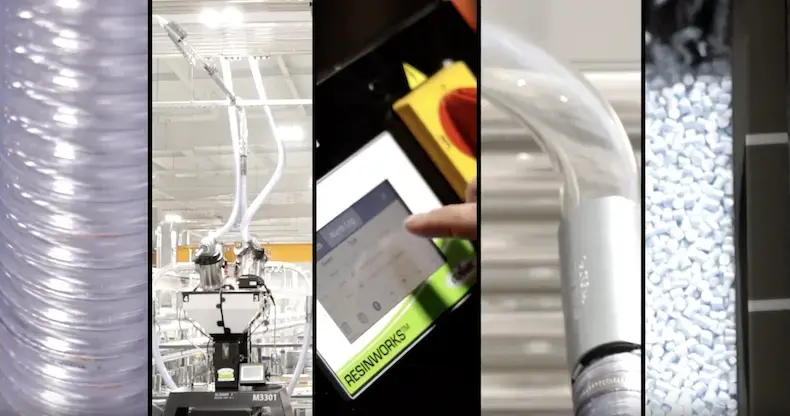
How Centralized Material Handling Streamlines Injection Molding
We consistently look for new ways to deliver timely service and top-quality parts …
READ MORE