The Top 4 Things Engineers Look at in Medical Component Design
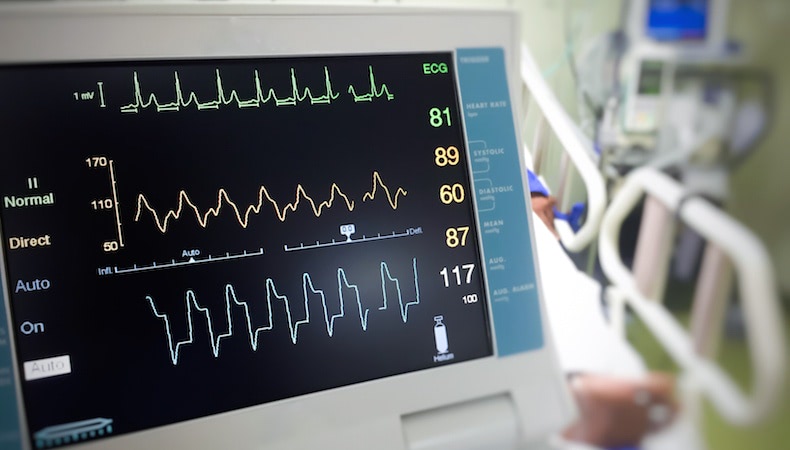
The success of a medical component project, like any other, depends on accurate communication of needs and expectations, especially in injection molding design. Engineers responsible for executing the project carefully review any initial designs submitted by the customer or potential customer, looking for specific elements that could help or hinder the medical component production.
Understanding what engineers are looking for, and what questions they may raise, will help you in refining the design and providing complete and accurate information upfront that will speed production of complex injection-molded medical components. Here are some common items engineers evaluate in the design phase:
Wall thickness
Wall thickness consistency is imperative. Introducing too many variations into one design will put your component at risk of warping, sinking and/or potential failure-inducing internal stresses.
Moldability of all features
While injection-molded plastic components are extremely versatile, there are some limitations. Certain features simply cannot be formed due to tooling constraints. For example, a particular indentation or protrusion (an “undercut”) in an injection-molded part may prohibit the use of a single pull mold because the undercut will prevent clean ejection. Likewise, ample clearance must be factored into the component design for the piece of the mold that physically forms the undercut. If that clearance is miscalculated or omitted, the medical component is at risk of deformation.
Gating
There are several facets of gating, (an orifice through which the molten plastic is injected into the mold), that impact tooling and, by extension, medical component integrity. The type of gate and location are primary factors, as they dictate part packing, gate removal, component aesthetics, part dimensions and warping. Further, gate size and shape vary depending on the plastic material being molded and the overall size of the component. While smaller gates on large pieces are more eye-pleasing, using them could actually inhibit resin flow, lengthen mold time and possibly interfere with fill pressures and proper filling.
Tolerance feasibility
It’s not uncommon for product engineers to overcompensate on tolerance requirements during design with the goal of finished part reliability. However, the stringent parameters may not be achievable in injection-molded plastic and/or are simply not required at that stringent level of a high quality medical component for a successful medical component. Infeasible tolerances generally don’t add to the design, they only add unnecessary cost to production.
Being aware of what complex injection molding engineers consider in design review for medical device manufacturing and committing to having your initial design reviewed will improve overall project results. When experienced engineers review and optimize the design upfront, both the scientific molding practices that define the molding parameters once the tool is built, and the advanced production processes that are ultimately implemented, will be more effective, efficient and highly reliable.
Find out more about optimizing the manufacture of medical devices in Designing Plastic Parts & Products for Critical-Use Medical Applications. Click the button below to download your free copy.
Subscribe
TO OUR BLOG
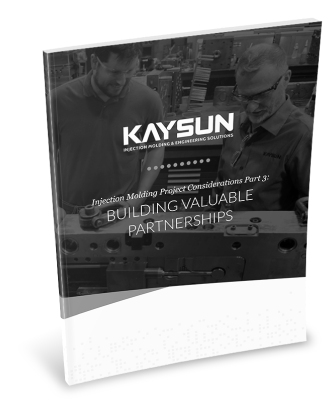
How Do Injection Molder Partnerships Influence Project Costs?
You Might Also Like...
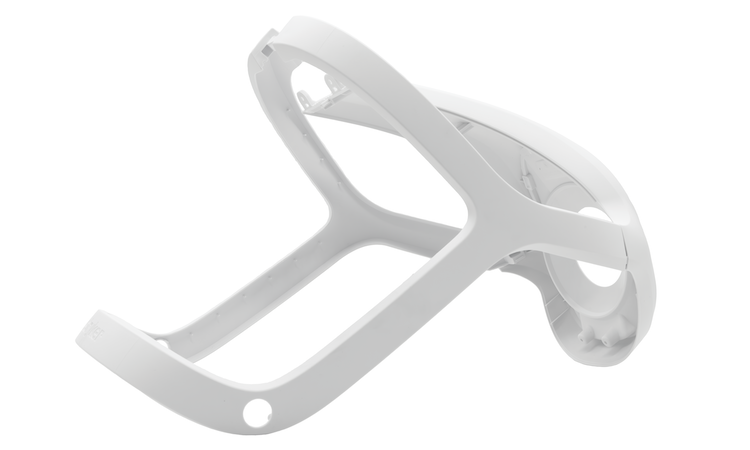
Stryker Turns to Kaysun for Steri-Shield® 8 Helmet Solution
When Stryker set out to develop its next-generation Steri-Shield® 8 Personal Prote…
READ MORE
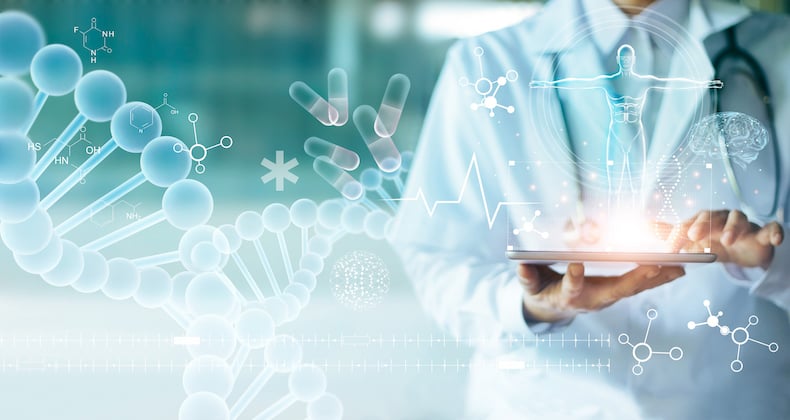
How MD&M West 2024 Keeps MedTech Professionals Ahead of the Curve
MD&M West is one of the largest and most respected medical device trade shows …
READ MORE
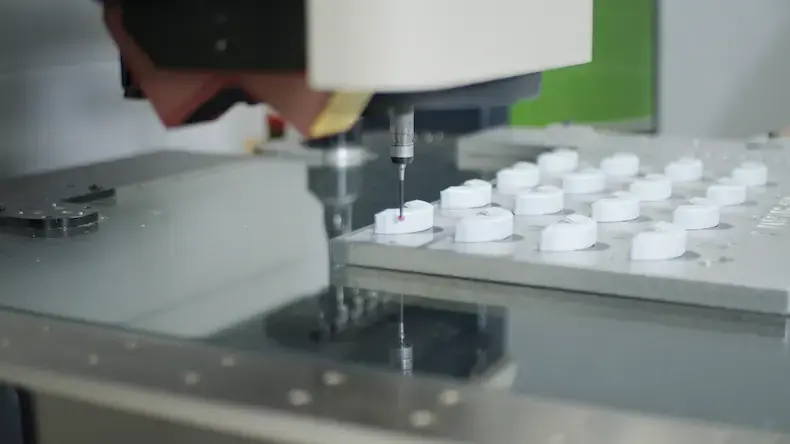
How MedAccred Accreditation Helped Kaysun Enhance Processes & Quality Systems
When you operate at the top of your game, reach higher. Kaysun had already shown i…
READ MORE