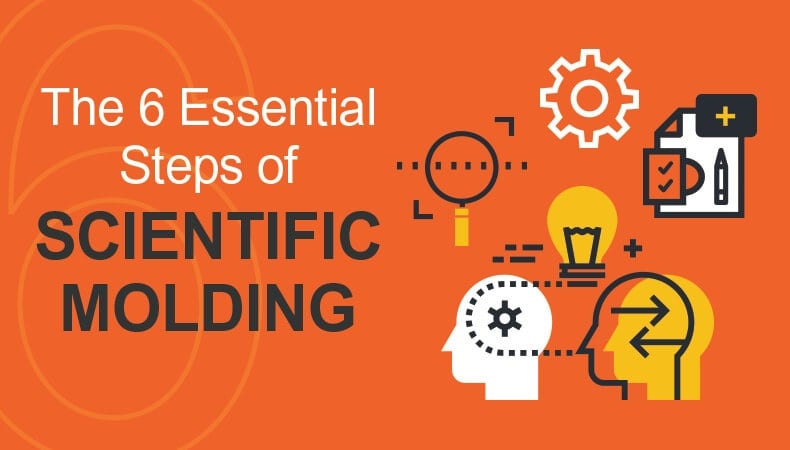
The result? Consistent, high-quality injection-molded plastic parts and devices that meet end-user expectations and drive competitive advantages for OEMs across many industries.
6 essential steps of THE scientific molding PROCESS
While thorough, comprehensive, and unique to each complex application, scientific molding can be broken down into six steps for highly specialized engineers to follow.
SCIENTIFIC MOLDING PROCESS steps, explained
- Review and recommend. Upon review of the initial part design and its complexity, the molder recommends scientific molding to the OEM if appropriate. Applying scientific molding principles requires that engineers possess specialized knowledge and training. Not every injection molder has this skillset or the necessary equipment and, therefore, cannot provide scientific molding options to OEMs.
- Design part and tooling. Scientific molding is dependent upon data. To accurately gather information throughout the process, both the part and tool must be designed by specially trained engineers to accommodate scientific molding sensors.
- Build tool. After part and tool design is completed and initial specifications approved, the first iteration of the tool is constructed. This tool is rigorously tested to reveal preliminary functional errors so necessary refinements can be made.
- Establish process window. Testing the tool is at the heart of the scientific molding process. A series of hypotheses and tests — known as a Design of Experiments (DoE) — is conducted to determine key parameters (flow rate, mold temperature, melt temperature, filling pressure, packing pressure, etc.). In turn, these key parameters produce optimal injection molding outcomes when consistently applied to the molding procedure (the process window).
- Move to production and monitor. Once the process window is established, final dimensional adjustments are made and full-scale production may begin. The process window is closely monitored and remains constant during production.
- Maintain. Proper machine and tool maintenance (cleaning surfaces and sensors, etc.) prolongs tool life, ensures adjustments are minimal, and is critical to preventing downtime or defective parts.
Experienced engineers — like those on the Kaysun team — are integral to a successful scientific molding process. They are trained to adhere to these six essential steps and have the expertise to optimize the process window for your specific project.
For another visual guide on the process of scientifically qualifying a tool, click below!