5 Ways Prototype Tooling Speeds up the Production Process
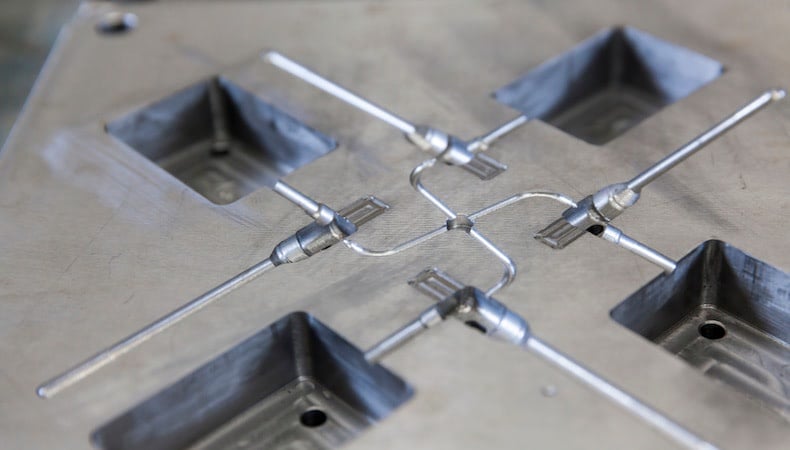
A surprising number of projects are completed without using a prototype tool. The general idea is that prototype tooling is an extra, unnecessary step that increases cost and decreases development and production times.
Actually, the opposite is true. Custom injection molding done without a prototype tool typically leads to a series of required production tool adjustments that are both costly and disruptive. The perceived savings of skipping prototype tooling quickly evaporate, and the higher risk of part defect introduces the possibility of incurring legal expenses and other related costs.
Depending on the complexity of the application, prototype tooling generally accounts for about 20-40% of overall production tooling costs. It's not an insignificant investment, but one that's well worth it when you consider the advantages.
The elements of prototype TOOLING
Prototype tools are constructed from softer tooling materials and are usually simplified to a single-cavity prototype instead of multi-cavity production. The prototype design gives OEMs a glimpse into an application's possibilities. Working with an experienced custom injection molder to understand the nuances through the lens of prototype injection molding helps verify information prior to decision-making:
1. testing different plastic materials
Prototype tooling is intentionally designed to accommodate low-volume production. Therefore, any plastics up for consideration can be efficiently performance-tested and comparisons assessed without a major financial investment. Having the luxury of physically evaluating materials is a major advantage in making a final selection.
2. Confirming part geometry feasibility
This is the perfect opportunity to see if the part fills properly without defects (voids, weld lines, flow marks, burning, sinks). If there are problems, it is relatively simple to revise the prototype tool with cuts or welds.
Likewise, adding or removing wall thickness, ribbing, or radii may be necessary to perfect part geometry for production. With prototype tooling, new dimensions can be applied, tested, and verified.
Unlike final production tools that are built to last a long time, the main goal of the prototype tool is to gather data.
3. Optimizing gate locations
Gating allows the material runners to interface with the tool cavity, making their location and design pivotal in molded part quality.
An injection molder experienced in Design for Manufacturability (DfM) analysis can provide the insights needed to properly place gates, and also guide prototype tool welds and cuts for appropriate gating adjustments. Doing so within the realm of prototype injection molding eliminates the cost and lost time in modifying the production tool. Moreover, it maintains production tool performance and lifespan.
4. evaluating complex part geometries
Tooling components like lifters and slides that are used to form undercuts in production tools are very complex and expensive, making it impractical to include them in a prototype mold. However, to test these features during prototype injection molding, hand-loaded inserts can be used in place of actual lifters, slides, and other challenging geometries.
5. reducing production time
Overall, it is quicker and cheaper to make changes to a prototype tool compared to the production tool.
Kaysun has the resources and experience to design, create, and revise prototype tools in-house — a competitive advantage in the industry. The information learned during prototype injection molding will:
- Lead to a final design that requires far fewer revisions to the production tool
- Save time and money on the back end of the project
- Optimize cycle times and reduce overall production costs
WHAT ABOUT RAPID PROTOTYPING AND ADDITIVE MANUFACTURING?
There is a keen interest in rapid prototyping and additive manufacturing these days — however, prototypes made using these processes lack access to the valuable production data gathered from prototype tooling, such as ideal gate locations, fill rates, cooling rates, etc.
The focused results from prototype tooling give engineers the information they need to identify and correct any part design or production challenges well before a production tool is made or the first batch runs. The time and cost savings are further augmented by a production process that maximizes manufacturability and speed to market, as detailed in our eBook, 5 Steps to Get New Injection Molded Products to Market Faster.
Subscribe
TO OUR BLOG
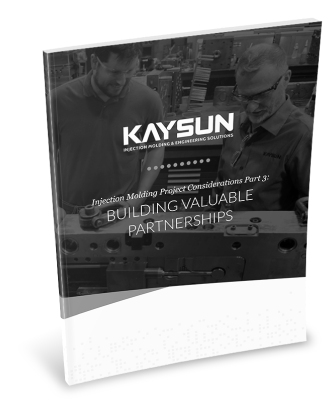
How Do Injection Molder Partnerships Influence Project Costs?
You Might Also Like...
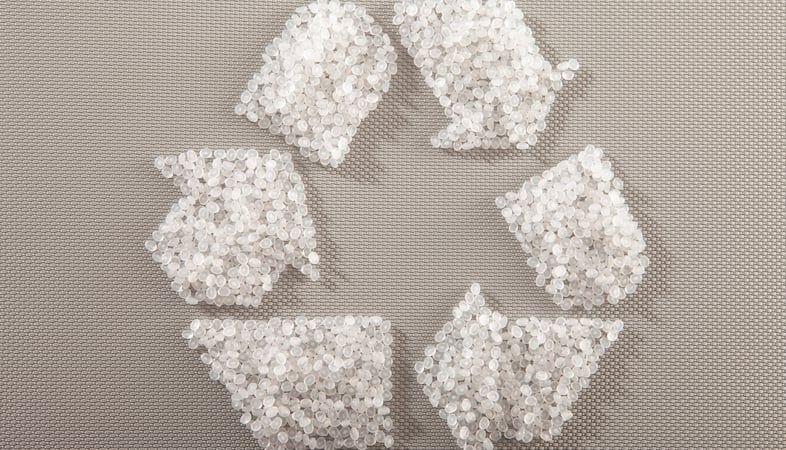
How Kaysun’s Culture of Sustainability Benefits OEMs and The Planet
Injection-molded parts and products are staples for OEMs in industries ranging fro…
READ MORE
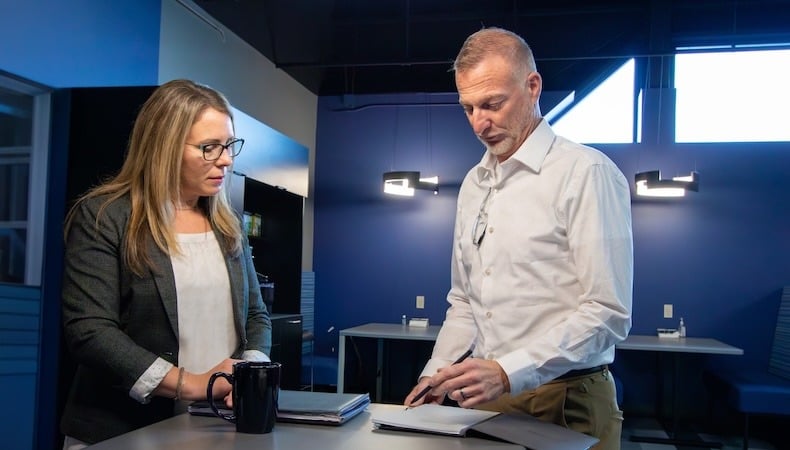
12 Common Injection Molding Questions — Answered!
Injection molding is a versatile and precise process, making it ideal for OEMs tha…
READ MORE
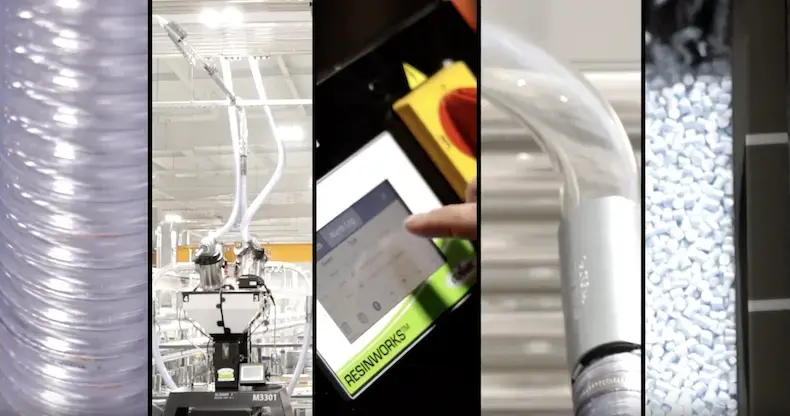
How Centralized Material Handling Streamlines Injection Molding
We consistently look for new ways to deliver timely service and top-quality parts …
READ MORE