How Quality Control Checks for Injection Molding Lead to Project Success [VIDEO]
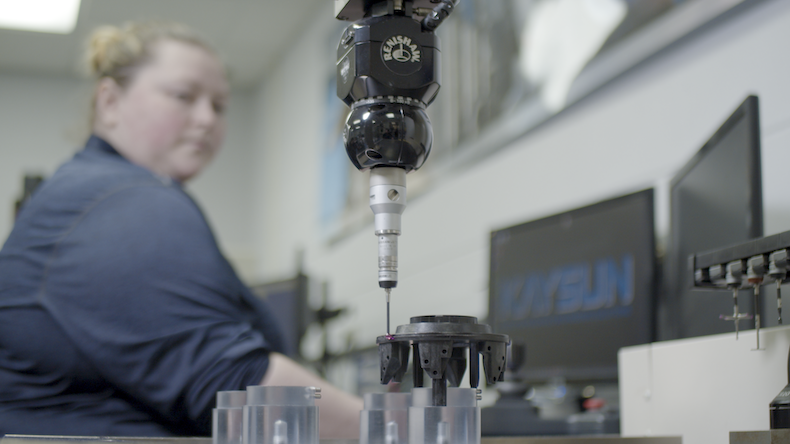
Well before the injection molding equipment is made ready for a run, experts in the in-house Quality Lab are at work gaining deep insights into the part design, thoroughly examining the part practicalities and potential pitfalls, and identifying areas for improvement. Kaysun project and quality control engineers and those of the customer collaborate to share knowledge, make adjustments, and arrive at the best possible production process, tooling, and application outcome.
The Kaysun Approach to Quality Control Checks for Injection Molding
Plastic molding quality control doesn’t stop at the successful conclusion of part design and engineering. In many ways, it has only begun. Kaysun quality control checks for injection molding are incorporated into every aspect of part production — from project start-up through its conclusion.
Inspections span departments, personnel, shifts, and production runs for around the clock quality control and production support. Kaysun blends in-house expertise and advanced data-driven technologies such as the IQMS quality system to ensure we hold ourselves accountable to the top priority: consistently meeting customer expectations, needs, and satisfaction levels.
In this short video, members of the Kaysun Quality Control team explain how quality control checks for injection molding projects are administered, and what makes the Kaysun approach so robust:
Kaysun In-House Quality Lab [VIDEO TRANSCRIPT]
Kaysun has a very structured procedure for advanced quality product planning. Our cross-functional team supports tooling and injection molding process development, and the quality aspects they entail for our customers.
Our APQP procedures and processes start out with a review of the tooling design, both with our customer and with the tool building shop. On first shots, we apply extremely comprehensive scientific molding methods to make sure we have the best possible process. We then continue into first inspections, documentation, and preparation for a production run.
Our project and quality engineering teams work closely with our customers’ design and quality engineers. Clear communication is essential. We all need to understand the expectations of how to measure the components and where to measure the components based on the solid model or drawing we’re working with for a given project.
After completing our installation qualification (IQ) and operational qualification (OQ) process, we’re ready to go into a pilot production run. Our team makes sure everything is documented, all the books are ready, and the tool is ready before turning it over to the production team. We continue the pilot runs, collect all the data, and summarize findings. From the summary we go through and we do a gate three to decide if it’s ready to launch into production.
The meticulousness of plastic molding quality control is mutually beneficial. Kaysun verifies the robust process behind running a specific tool day in and day out, and our customers know their deliveries are met with conforming products that align with their customer needs.
Quality control support goes across the entire process from start-up of the product to the end. We are there to continuously analyze and measure the parts to ensure that what production is making meets the specifications of the customer. This really gives Kaysun the ability to approach part inspection in any fashion that’s needed to meet customer requirements.
As a result, we know immediately whether something is in specification or not. Kaysun’s IQMS quality system is really the backbone of how we run the production floor and perform in-process inspections. A lot of times we move things into the production area from development so we can overlap processes, discuss the project, and work together on it.
Kaysun’s quality control has two quality technicians per shift. We cover all three shifts in support of production. We do inspections at regular frequencies at start-up and in-process to meet customer needs.
The Necessity of Plastic Molding Quality Control
By nature, quality control is a very detailed and structured procedure. The attention to detail, expert analysis, and dedicated process management aren’t capabilities all custom injection molders can offer — and fewer still have proficiencies in-house as Kaysun does.
As you partner with an injection molder, quality control needs to be top of mind. Mediocrity in this area could lead to unnecessary risk and expense in processes, production, and outcomes. Is Your Molder Delivering Defect-Free Parts? explores common part failures that occur when comprehensive Design for Manufacturability (DfM) and scientific molding principles are not used and quality is largely left to chance. Click the button to download your copy of this valuable white paper.
Subscribe
TO OUR BLOG
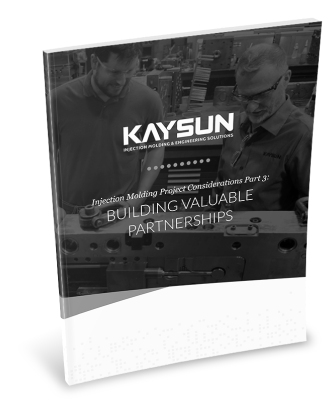
How Do Injection Molder Partnerships Influence Project Costs?
You Might Also Like...
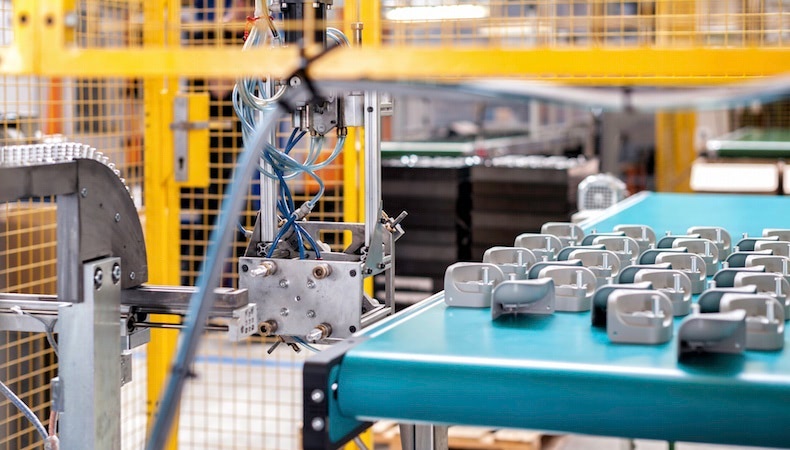
The Impact of Non-Uniform Injection Molding Wall Thickness
Shrink rates for plastic parts vary depending on the materials used and the unifor…
READ MORE
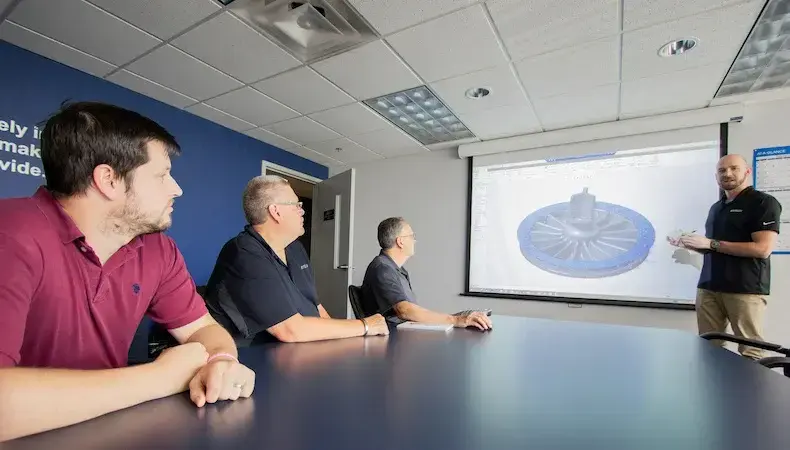
5 Engineering Factors That Improve Your Injection Molding Project
In many complex industries, decisions about which injection molder to use for cust…
READ MORE
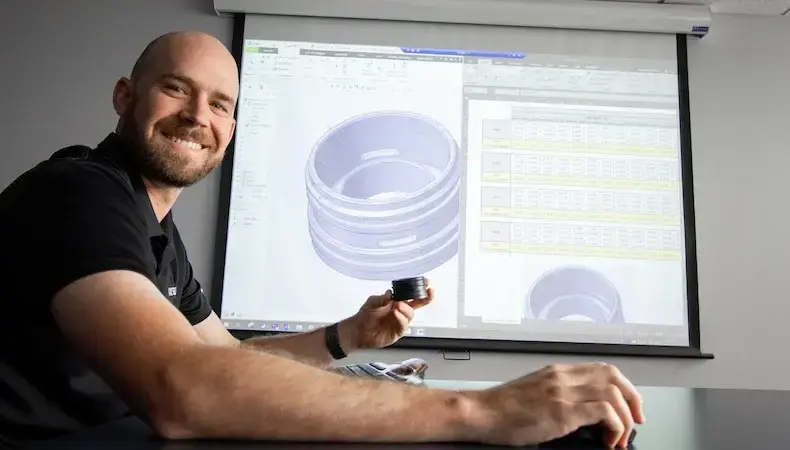
Why Continuing Plastic Engineering Education Matters to OEMs
Technologies, product needs, and customer expectations are rapidly advancing. OEMs…
READ MORE