4 Ways Reshoring Strengthens an Automotive OEM's Supply Chain
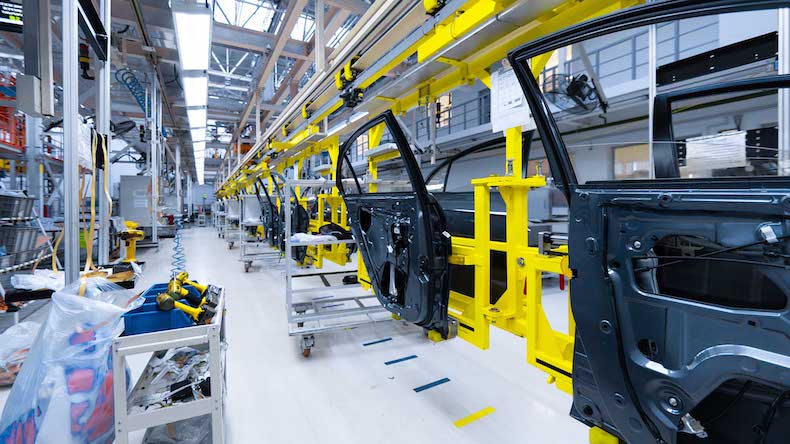
With a stunning 75% of automotive manufacturers reporting business interruption caused by the COVID-19 shutdown of non-essential businesses, many are taking a hard look at the impact of supply chain globalization1. More specifically, automotive OEMs are either proactively reshoring or planning to reshore to protect their supply chains — and businesses — from the political and economic fallout created by the pandemic.
The practicalities of reshoring are counterbalanced by hesitation around the cost of doing so. The auto industry is facing major hurdles as slashed auto sales and production stoppages mount, and OEMs are leery of transitioning to what has historically been a more expensive mode of manufacturing versus offshoring.
However, as supply chain partnerships continue to break under the strain of the pandemic, automotive OEMs are assessing the price they pay for upfront offshore savings. Parts shortages, production line shutdowns, product defects, and transportation delays are common — and costly.
Reshoring to a U.S. supplier for custom injection-molded automotive components lends itself to providing a skilled, trustworthy supply chain that is responsive to manufacturers’ needs in four key areas:
1. Parts Availability
Automotive manufacturers must inventory custom injection-molded plastic parts to fulfill vehicle orders and stock replacement parts. Offshoring puts consistent production at risk because of the increased potential for logistical snags, time zone miscalculations, and quality-impaired components.
Conversely, domestic custom injection molders dramatically shorten the supply chain by removing the complications of international commerce. Defect-free plastic parts are produced faster, and are reliably delivered to automotive OEMs when — or before — they’re needed.
2. Production Line Efficiencies
Perhaps the single biggest obstacle to efficient offshore production is the language barrier. Reliance on basic English might get a project up and running, but miscommunication typically ensues when colloquialisms don’t translate to easy explanations and actionable steps, or written product requirement documents cannot be properly reviewed.
The same holds true for cultural gaps, wherein the concepts of speed and timeliness often aren't universally aligned. As a result, productivity is skewed and critical deadlines missed.
Reshoring to proven U.S. suppliers effectively negates these risks on the production line and throughout the entire manufacturing process.
3. Defect-Free COMPONENTS
Injection-molded parts that serve pivotal automotive functions or are intricate in design can be easily compromised without consistent oversight and quality control. Any defective parts are potentially hazardous, but those manufactured abroad present additional costly dilemmas for the manufacturer such as:
- Are the parts reworked in the U.S., or returned to the country of origin?
- If returned, can the project absorb additional shipping cost and time?
- Who is responsible for product liability and litigation?
On the other hand, domestically produced automotive components remain under manufacturer quality assurance standards. Course correction, when necessary, is efficiently accomplished because resolving product defects doesn’t result in a host of additional issues.
4. Efficient Logistics
Transoceanic shipping and varying time zones automatically increase product lead time. This is inefficient in itself without factoring in adverse weather, customs complications, and other delay-inducing delivery hurdles.
Working with suppliers closer to home minimizes wait time and shipping obstacles, allowing automotive manufacturers to quickly respond to customers’ demands. Also, domestic shipping costs are generally lower due to distance and required mode of travel.
We're living in unpredictable times, and the abundance of caution exercised in the automotive industry reflects it. Reshoring is a practical and increasingly popular solution for automotive OEMs in need of custom injection-molded parts and a domestic supply chain that consistently fulfills that need.
Exploring Reshoring: Insights for Manufacturers details the many facets of reshoring and identifies how they impact key areas within your operation. Click the button below to download your copy of this valuable guide now.
SOURCE: 1Assembly Magazine, Thomas Survey: Two-Thirds of Manufacturers Likely to Reshore as a Result of Pandemic, June 23, 2020
Subscribe
TO OUR BLOG
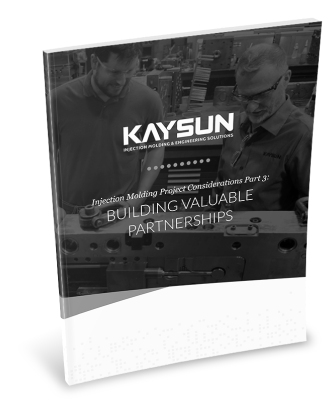
How Do Injection Molder Partnerships Influence Project Costs?
You Might Also Like...
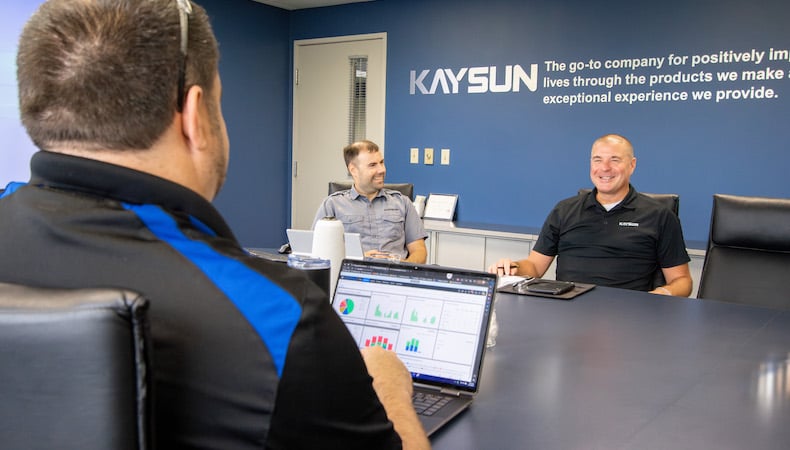
Top 3 Custom Injection Molding Trends to Watch in 2025
Despite being considered more energy efficient and producing less waste than other…
READ MORE
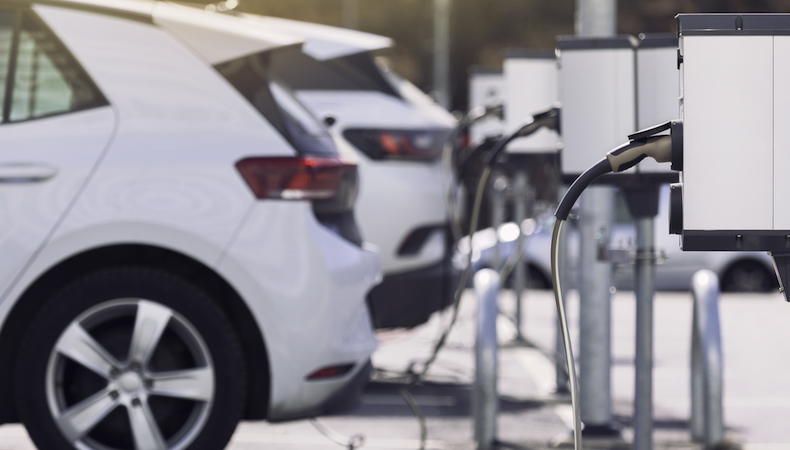
Gas or Electric: Do Vehicle Power Sources Impact Automotive Plastics Selection?
Environmental protection and the legislation surrounding it have heightened people…
READ MORE
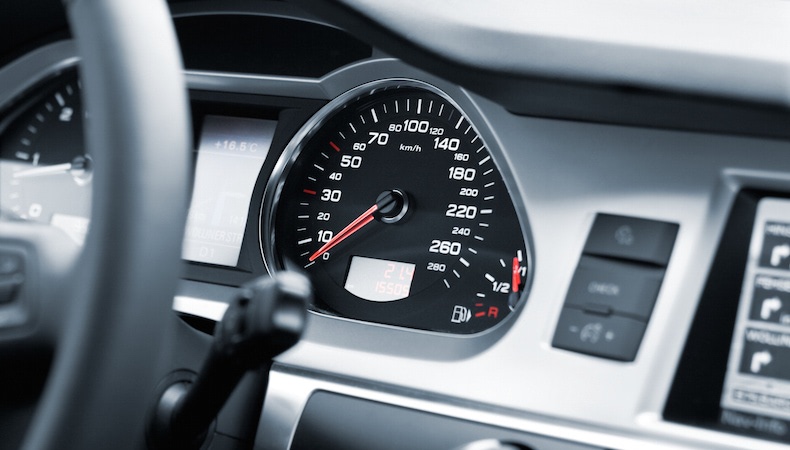
4 Automotive Plastic Parts Trends That Are Redefining the Industry
By 2024 the need for automotive plastics, parts, and innovations will push the val…
READ MORE