3 Engineering Support Services Your Injection Molder Must Offer
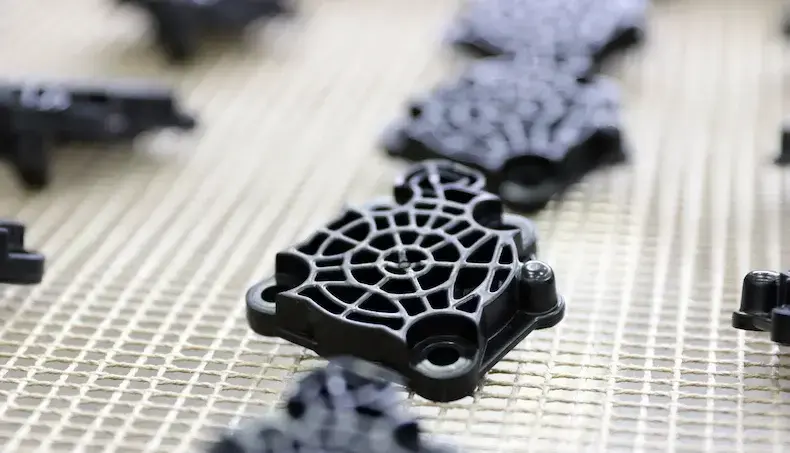
There’s no denying that pandemic-related, weather-influenced, and manmade disruptions have caused chaos within the plastics industry. For OEMs, finding injection molding solutions during these turbulent times is problematic. Finding knowledgeable molders to take on complicated design, engineering, injection molding, and other challenges that less skilled molders can’t handle is equally as difficult.
The latter is an ongoing frustration for OEMs. Oftentimes, the limitations of commodity molder aren’t revealed until plastic part defects evidence themselves. Or, perhaps the molder openly acknowledges inexperience with certain advanced skills and refuses the job. Either way, it puts the OEM in a precarious position.
Everything from engineering complex plastic parts through production requires confidence and capabilities that only experience can provide. That’s why Kaysun is the preferred custom injection molding partner for OEMs across industries.
Applying Knowledge, Leveraging Technology
The Kaysun production line has state-of-the-art injection molding technologies, capable of producing sophisticated, high-quality plastic parts. But simply having the equipment doesn’t guarantee success.
Custom injection molding doesn’t start at the production line. It encompasses an entire process. In-house design, testing, manufacturing, and assembly capabilities underpin Kaysun quality.
These robust engineering support services also give our partners peace of mind. Simply put, there’s a greater likelihood that their most daunting design, engineering, injection molding, and related challenges will be solved:
- Design for Manufacturability (DfM): In broadest terms, Design for Manufacturability (DfM) — also known as Design for Manufacturing — is the process whereby specially trained engineers consciously and proactively design parts to optimize all facets of manufacturing, including injection molding. DfM aligns engineering and production in the initial design phase so potential problems can be identified and resolved before they result in costly rework.
- Resin Selection Support: With 25,000+ engineering resins available, narrowing down thousands of options to a handful of suitable choices doesn’t happen by chance. Collaboration with a molder practiced in materials science and behaviors helps align resins with the function, environment, exposure risk, and performance expectations.
- Metal to Plastic Conversion: When left to experienced custom injection molders like Kaysun, metal to plastic conversion can be a powerful solution for decreasing part weight and lowering costs without sacrificing tight tolerances or performance. This commitment to quality is particularly attractive to OEMs that have encountered problems with other molding vendors that resulted in additional machining costs, recalls, and risk of potential litigation.
Working with a competent injection molder is one thing. Having a true partner that can eliminate the struggle and worry of potential injection molding missteps and elevate outcomes is another.
At Kaysun, we pride ourselves on supporting our customers with engineering services that help define, work toward, and achieve exceptional outcomes. See how we were put to the test when a belt tensioning pulley assembly presented metal-to-plastic conversion opportunities. Click the button below to download the Gates Corporation Case Study now.
Subscribe
TO OUR BLOG
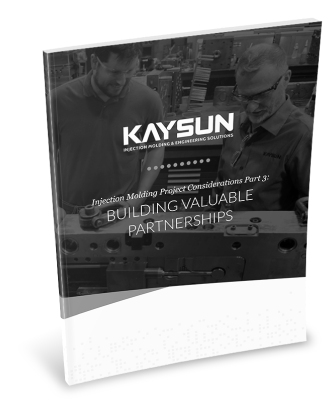
How Do Injection Molder Partnerships Influence Project Costs?
You Might Also Like...
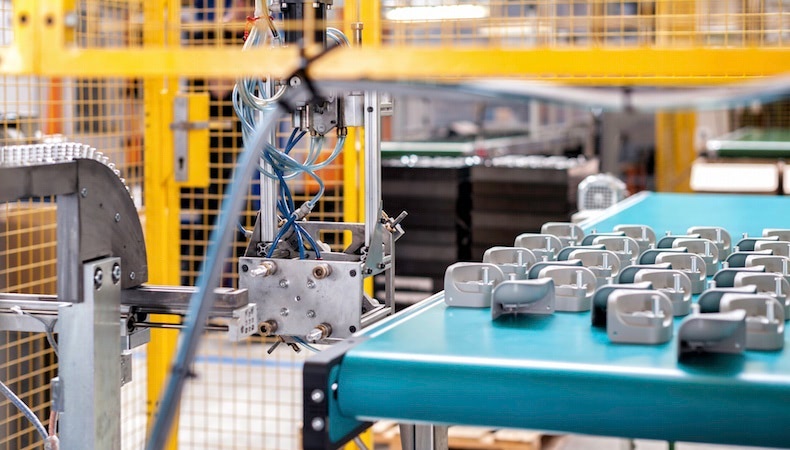
The Impact of Non-Uniform Injection Molding Wall Thickness
Shrink rates for plastic parts vary depending on the materials used and the unifor…
READ MORE
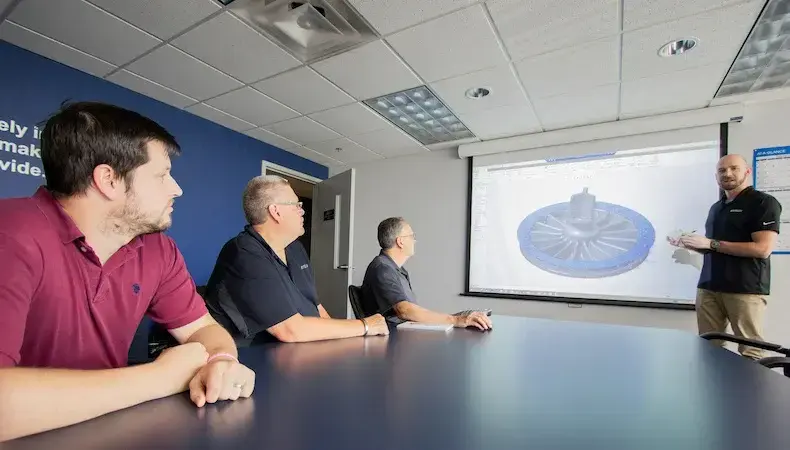
5 Engineering Factors That Improve Your Injection Molding Project
In many complex industries, decisions about which injection molder to use for cust…
READ MORE
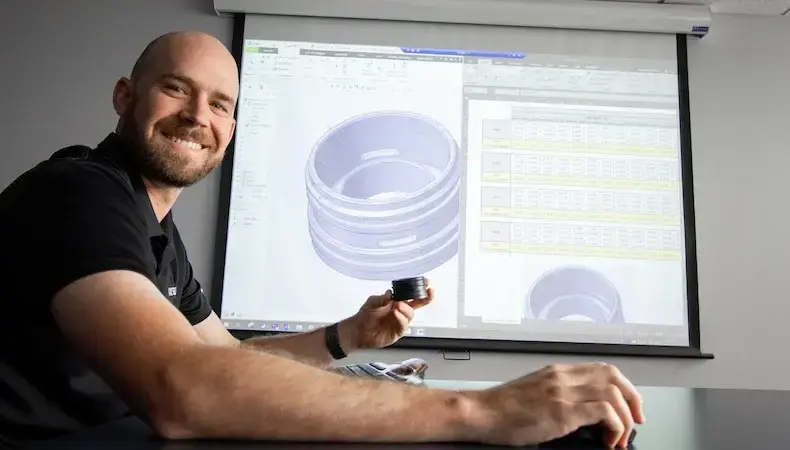
Why Continuing Plastic Engineering Education Matters to OEMs
Technologies, product needs, and customer expectations are rapidly advancing. OEMs…
READ MORE