How The Role of Injection Molders Is Redefined by the Resin Shortage
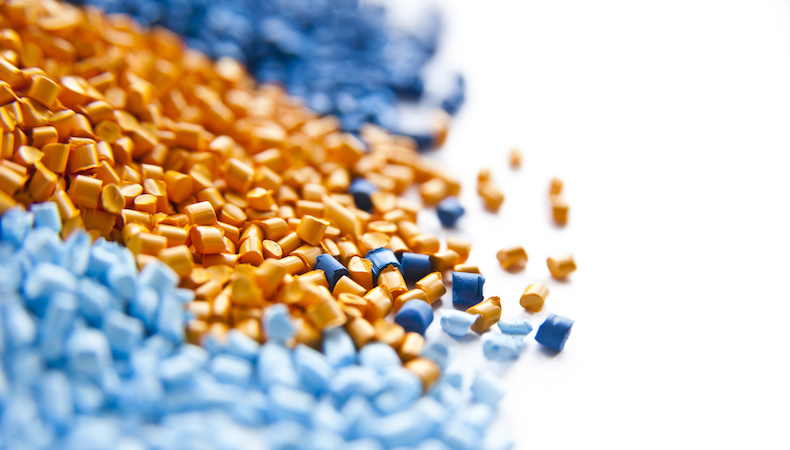
The resin shortage has injection molders and the larger plastics industry struggling to find balance. The late-February storm that blew into Texas and shut down 80% of U.S. resin production was the catalyst, but only one contributing factor.1
Industry authorities point to several reasons why resin supply and resin cost continue to fluctuate and how the ripple effect impacts suppliers and injection molders. A snapshot of current pricing illustrates the topsy-turvy landscape:
Source: The Plastics Exchange
Knowing the “whys” behind the problem is beneficial, but absorbing a 50% price increase per pound of polypropylene (PP) and 30% reduction in production capacity isn’t sustainable.1 It raises an equally pressing question: what can injection molders do about it to support customers, maintain production, and protect margins?
Injection Molders Search for Answers
A recent PlasticsToday “Plastic Possibilities” podcast tapped business consultant and supply chain expert Ambrose Conroy of Seraph for insights into the resin shortage dilemma.
Conroy frames the situation as a failure of risk management. It’s partially understandable given the statistical unlikelihood of one low probability/high impact event occurring, let alone several in succession. However, the reality is that a global pandemic, a blockage and shutdown of the Suez Canal, and a power grid-crippling U.S. winter storm all happened. And they all chipped away at the plastics industry.
The discounted risk revealed several shortcomings in what was thought to be a seamlessly integrated global supply chain, leaving injection molders and others in the industry to grapple with:
- Labor challenges: The widening skilled workers gap was already a concern. COVID-related shutdowns, layoffs, and hesitancy about potential virus spread further decimated the workforce.
- Price volatility: A limited resin supply drives up prices. Injection molders feel the pinch of resin costs from both sides as suppliers pass along increases and OEMs are reluctant to take on extra expense during uncertain times.
- Not meeting consumer demand: The pandemic continues to keep people at home. Spending less on outside experiences and services has funneled more money into product purchases — most of which contain plastic. Skyrocketing demand can be seen as a positive for the industry, of course, but it also creates pressure that further constrains a weakened supply chain.
Taken individually or on the whole, the obstacles spell trouble for injection molders. In response, many molders have undertaken initiatives to maximize assets.
Investing in technologies that offer the best OEE, developing internal staff members, and strategically shifting into additional verticals are among the most popular approaches. However, seeking alternative materials is more often the solution of choice.
The Good and Bad of Alternative Materials
Given that there are more than 25,000 engineered plastics, finding alternatives mainly to PP and PE seems like it would be easy enough. But, like so many challenges related to the resin shortage, it’s not quite that simple.
In the larger context, importing and inventorying alternative materials are hampered by container shortages. A lack of containers can tack on days, if not weeks, to shipping and port delays. Even if the resins are delivered, not all injection molders have storage capacity without the aid of containers.
Local and regional shutdowns related to COVID also complicate the issue. Countries currently shouldering more production capacity such as China and the U.S. can’t depend on other regions to come back online as anticipated. As a result, resiliency and demand are at loggerheads which interferes with finding and using alternative materials.
Declarations of force majeure often ensue for injection molders because:
- Current shortages blanket multiple grades of resin, limiting which alternative solutions may be viable
- If a certain plastic is deemed appropriate for use, there are no guarantees that the manufacturer is in a position to take on new customers to accommodate the need
- Excessive lead times — 20 or more weeks in some cases — make it impractical to fulfill orders in a timely manner
Collaborative Efforts
While the news is dire, it doesn’t mean that alternative materials are off the table as solutions for injection molders and their OEM customers. In fact, it is collaboration between the two that is leading to successful navigation of the resin shortage.
Kaysun works in tandem with our resin supply partners and customers to facilitate honest conversations around available options, production timelines, and other factors influencing outcomes. Doing so helps us set realistic expectations and maximize press schedules, as well as manage supply continuity risk and long-term resin supply viability.
Collaboration is a longstanding practice at Kaysun, and it’s proving even more valuable as the industry continues to roil in light of the resin shortage. By signing onto a project from design through production, we can address short-term problems and long-term risks associated with resins. In some cases, total delivered cost is ultimately reduced even amid resin price volatility — a win-win for OEM and injection molder alike.
Learn more in our reference guide, How Injection Molder Partnerships Influence Project Costs. Click the button below to download your copy of this valuable resource.
SOURCE
1PlasticsToday, Plastic Possibilities: Resin Production Meets the Perfect Storm, April 12, 2021
Subscribe
TO OUR BLOG
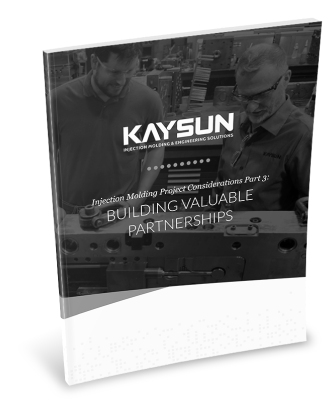
How Do Injection Molder Partnerships Influence Project Costs?
You Might Also Like...
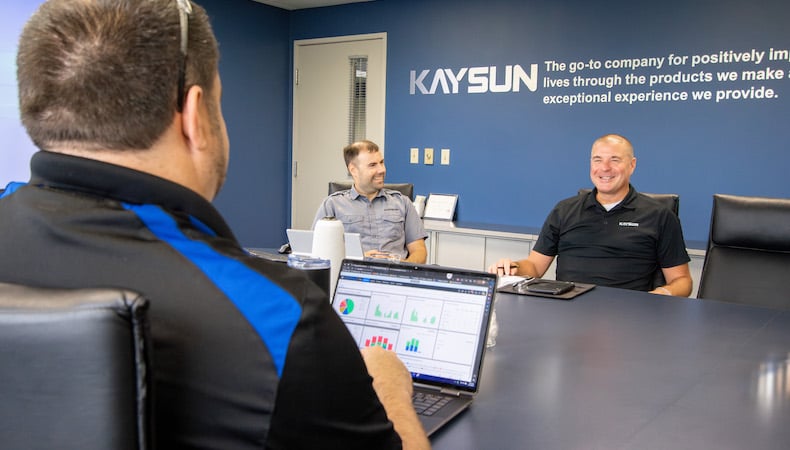
Top 3 Custom Injection Molding Trends to Watch in 2025
Despite being considered more energy efficient and producing less waste than other…
READ MORE
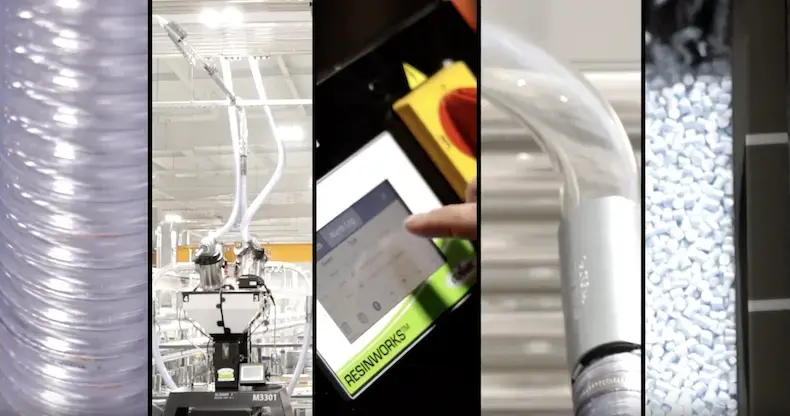
How Centralized Material Handling Streamlines Injection Molding
We consistently look for new ways to deliver timely service and top-quality parts …
READ MORE
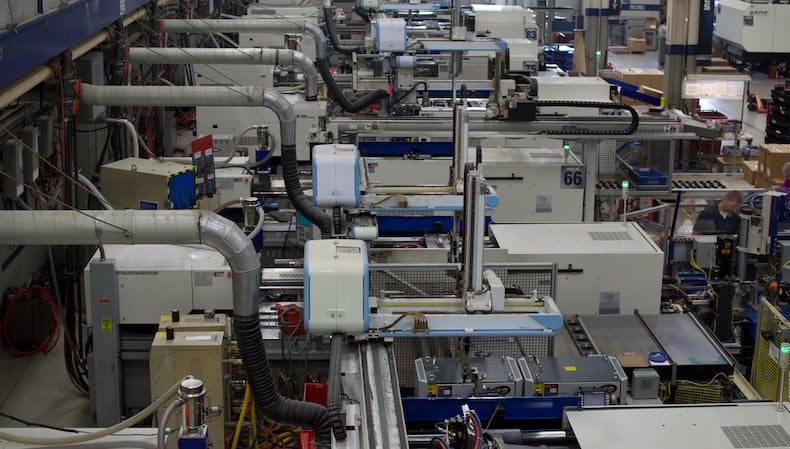
Top 14 Benefits of Injection Molding
OEMs across many industries enjoy the benefits of injection molding. It’s ideal fo…
READ MORE