The Benefits of Injection Molding for the Energy Distribution Market
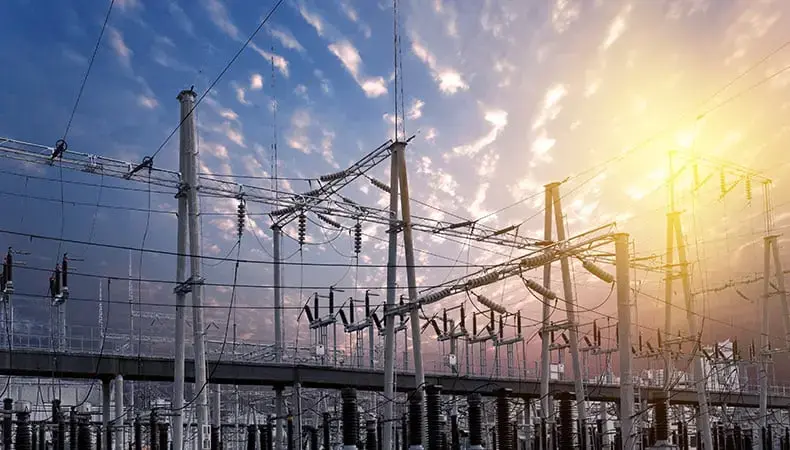
The power grid in the United States is shorting out. What began in the 1880s with some isolated power generation systems is now straining to support an estimated 7,300 power plants, and millions of miles of high- and low-voltage power lines in order to service about 200 million customer sites nationwide.1
The increasing number of rolling blackouts, prolonged outages related to natural disasters, and the looming risk of cyberattacks all point to the need for an electricity infrastructure overhaul. It’s an issue of ongoing debate in the political arena. In the meantime, energy distribution sector OEMs are actively seeking solutions to stem the impact of the current flagging power grid.
Many manufacturers are turning to their suppliers for guidance and innovation as much as for parts and products. Solutions for the energy distribution market must be versatile and reliable, which aligns with the benefits of injection molding.
The Structure and Challenges of the U.S. Power Grid
The sheer size of the U.S. power grid presents its own set of challenges for OEMs. There are three major interconnections that comprise the national electricity network. Each interconnection operates nearly autonomously to stabilize power flow and prevent failures, but the design inherently creates redundancies in need and maintenance. This puts pressure on energy distribution OEMs to readily supply key components, especially sought-after extra-high voltage fuses and current limiters.
Leveraging partnerships with custom injection molders to meet demand for these complex applications is proving beneficial for a number of reasons.
The Benefits of Injection Molding for Energy Distribution
Finding energy distribution solutions requires an injection molder that can address a number of factors, including:
- Design and engineering for complex part geometries substantiated by Design for Manufacturability (DfM) analysis
- Materials performance, which is a top priority since the amount and amperage of electricity that large fuses and circuit limiters are exposed to require proper insulation and flame retardancy
- Tooling construction that maximizes the life cycle through careful selection of the metal and/or coatings used to withstand the sometimes corrosive materials used in energy applications
- Overmolding services that align with the particular needs of high-voltage and often high-heat applications unique in energy distribution
- Regulatory agency competencies to aid OEMs in UL certification documentation and approval
The Value of Experience
Kaysun has practical experience in the energy distribution sector, and a recent challenge presented by an OEM partner brought all of our experience to bear.
Problem
A fuse required an overmolded protective outer liner, and the challenge in producing this component was twofold. First, the melt temperature of the overmolding material for the outer liner caused deformation of the fuse’s inner liner — essentially the inner liner melted and reformed during the overmolding process, which could introduce defects.
Additionally, reflection from the tooling caused thin spots in the fuse casing which impacted the performance of the fuse.
Solution
The Kaysun design, engineering, and quality control teams worked collaboratively with the OEM to develop a comprehensive solution. Switching the outer liner overmolding materials to a stiffer, specialized tungsten carbide provided consistent wall thickness that regulated the fuse’s performance and eliminated inner liner deformation concerns.
To compensate for the stiffness and potential fragility of the overmolded liner, Kaysun engineers developed a chilling system to circulate air and prevent cracking.
This type of full-circle thinking is a byproduct of the experience only a trusted custom injection molder can provide. It also demonstrates the importance of partnering with a knowledgeable molder to help guide in-demand solutions in the rapidly changing energy distribution market.
Learn more about how specialized plastics and the benefits of injection molding work together in our whitepaper, Processing High-Temperature and Engineered-Grade Resins. Click the button below to download your copy.
SOURCE
1U.S. Environmental Protection Agency, U.S. Electricity Grid & Markets, Undated
Subscribe
TO OUR BLOG
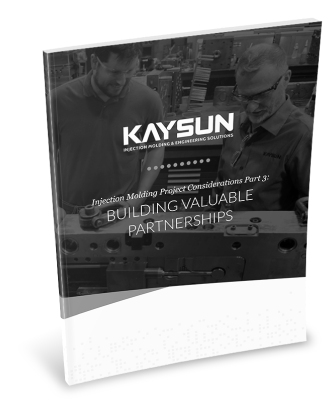
How Do Injection Molder Partnerships Influence Project Costs?
You Might Also Like...
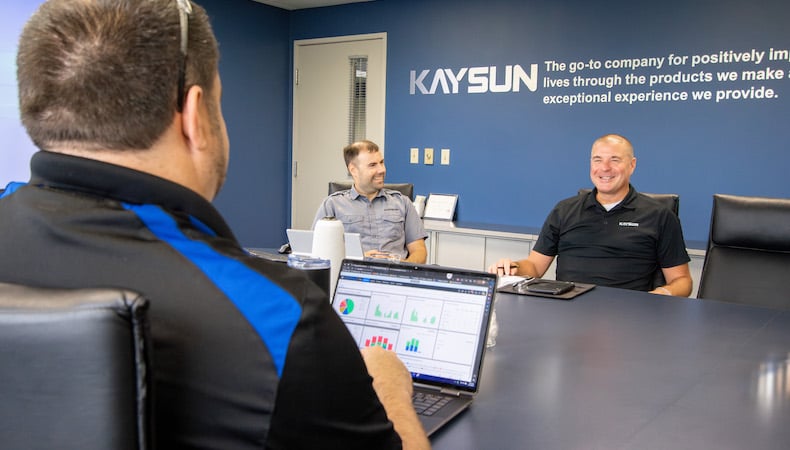
Top 3 Custom Injection Molding Trends to Watch in 2025
Despite being considered more energy efficient and producing less waste than other…
READ MORE
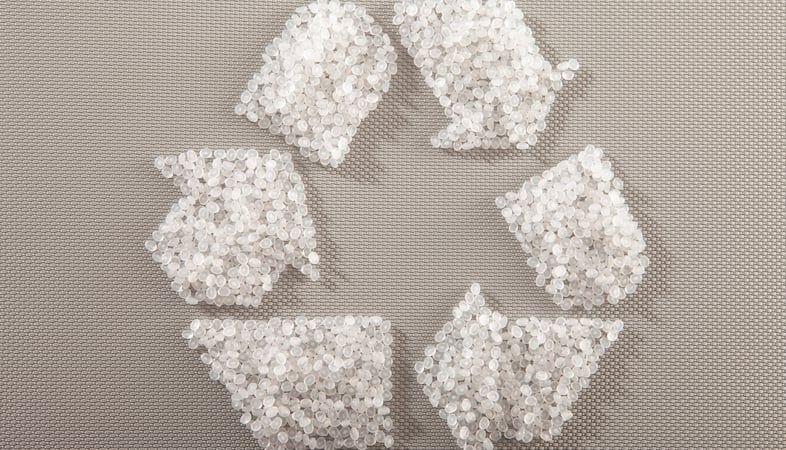
How Kaysun’s Culture of Sustainability Benefits OEMs and The Planet
Injection-molded parts and products are staples for OEMs in industries ranging fro…
READ MORE
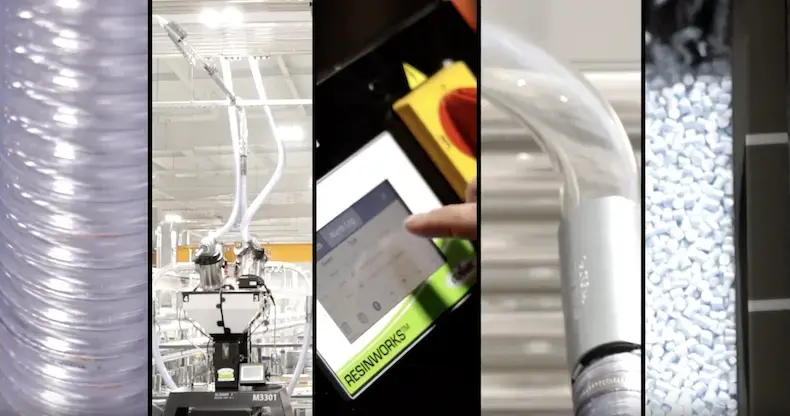
How Centralized Material Handling Streamlines Injection Molding
We consistently look for new ways to deliver timely service and top-quality parts …
READ MORE