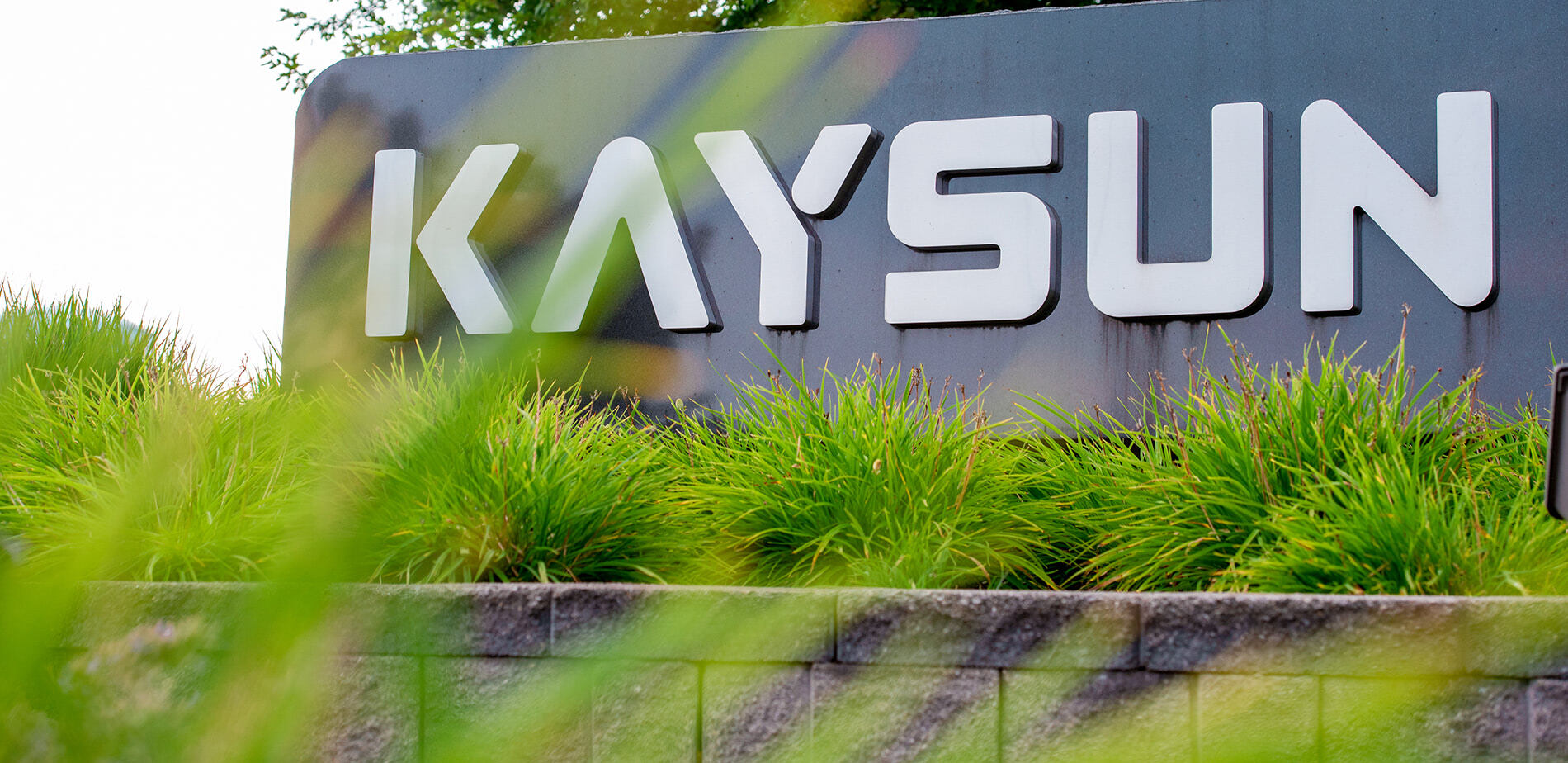
Injection Molding Sustainability: A Partnership Checklist
5 Criteria for a Sustainability-Focused Injection Molder Partnership
Finding an injection molder committed to sustainability isn’t blind luck. A molder that demonstrates experience and excellence in the following areas typically signals greater potential as an eco-conscious partner.
Energy Efficiency & Carbon Footprint Reduction
Injection molding is inherently energy-intensive. What is the molder doing to mitigate the impact?
- Advanced equipment: Electric presses generally consume less power than traditional hydraulic machinery, making them an ideal solution for increasing energy efficiency without compromising part quality.
- Facility energy management: Molders that invest in renewable energy sources, LED lighting, and climate control optimization demonstrate a heightened awareness of the need for energy conservation.
- Carbon footprint transparency: Sustainability-focused injection molders manage greenhouse gas emissions and other carbon-reduction activities.
Materials Management
Injection molders that take a holistic approach to materials sustainability can help OEMs make meaningful contributions to eco-friendly outcomes. Does the molder think about — and beyond — resin recyclability?
- Expanded choices in resins: Molders with the knowledge and flexibility to explore more sustainable materials provide a greater range of opportunities for OEMs.
- Closed-loop recycling: Systems that include plastic scrap regrind and reuse automatically minimize waste and improve overall sustainability.
- Product life cycle: Molders may have end-of-life product initiatives that involve take-back programs to ensure proper recycling vs. landfill degradation.
Process Optimization & Waste Reduction
Waste reduction best practices aren’t solely reserved for post-production. How does the injection molder proactively optimize processes to address waste reduction?
- Design for Manufacturability (DfM), scientific molding, and other design optimization methodologies: Applying advanced engineering to optimize materials use and reduce defects and scrap is integral to waste management.
- Advanced tooling: Using hot runner systems to eliminate sprue and runner waste and applying mold fill analysis to reduce defects are viable steps toward material waste reduction.
- Lean manufacturing and automation: Prioritizing production efficiencies reduces material waste and unnecessary energy use.
Integrated Technologies
Innovation doesn’t exist in a vacuum. How does the injection molder embrace and apply forward-focused technologies to streamline production and maximize more sustainable outcomes?
- Internet of Things (IoT): Real-time monitoring, analytics, predictive maintenance, and robotics autonomy refine existing innovation and leverage new solutions.
- Artificial Intelligence (AI): Expanding solutions by working more efficiently through artificial intelligence reduces labor burdens while controlling quality and output.
- Regulatory compliance: Technologies often amplify certifications representing adherence to regulatory standards and global sustainability guidelines/laws.
Corporate Commitment to Sustainability
Without the support of the entire team — from management to production floor — sustainability could be reduced to an aspirational corporate talking point. What steps is the injection molder taking to actively incorporate sustainability into facilities and practices?
- Sustainability goals and reporting: Injection molders that identify sustainability objectives and publish reports at a regular cadence demonstrate accountability.
- Employee engagement: Injection molders with teams that adopt a “green” mindset and foster eco-friendly practices are committed to sustainability for the long term.
- Industry thought leadership: Injection molders that actively participate in sustainability coalitions, industry partnerships, community energy projects, and other activities in support of eco-advancements demonstrate dedication beyond required compliance.
Kaysun’s Sustainability Promise
Sustainability is a core part of Kaysun’s business philosophy and daily operations. We’re proud to be leaders in sustainable injection molding practices, and we’re dedicated to finding new ways to continue to reduce environmental impact and help our customers do the same.
Key Sustainability Initiatives
We’ve undertaken several key sustainability initiatives that have advanced our earth-first efforts, including:
- Installing a Central Material Handling System (CMHS) that supports more sustainable production by reducing the number of dryers and energy used, and optimizing material handling for less spillage and waste
- Partnering with renewable fuel and power producers to convert waste to clean energy. Kaysun regrind is part of the 40% of recycled plastic in fuel pellets utility companies use to generate electricity instead of burning coal!
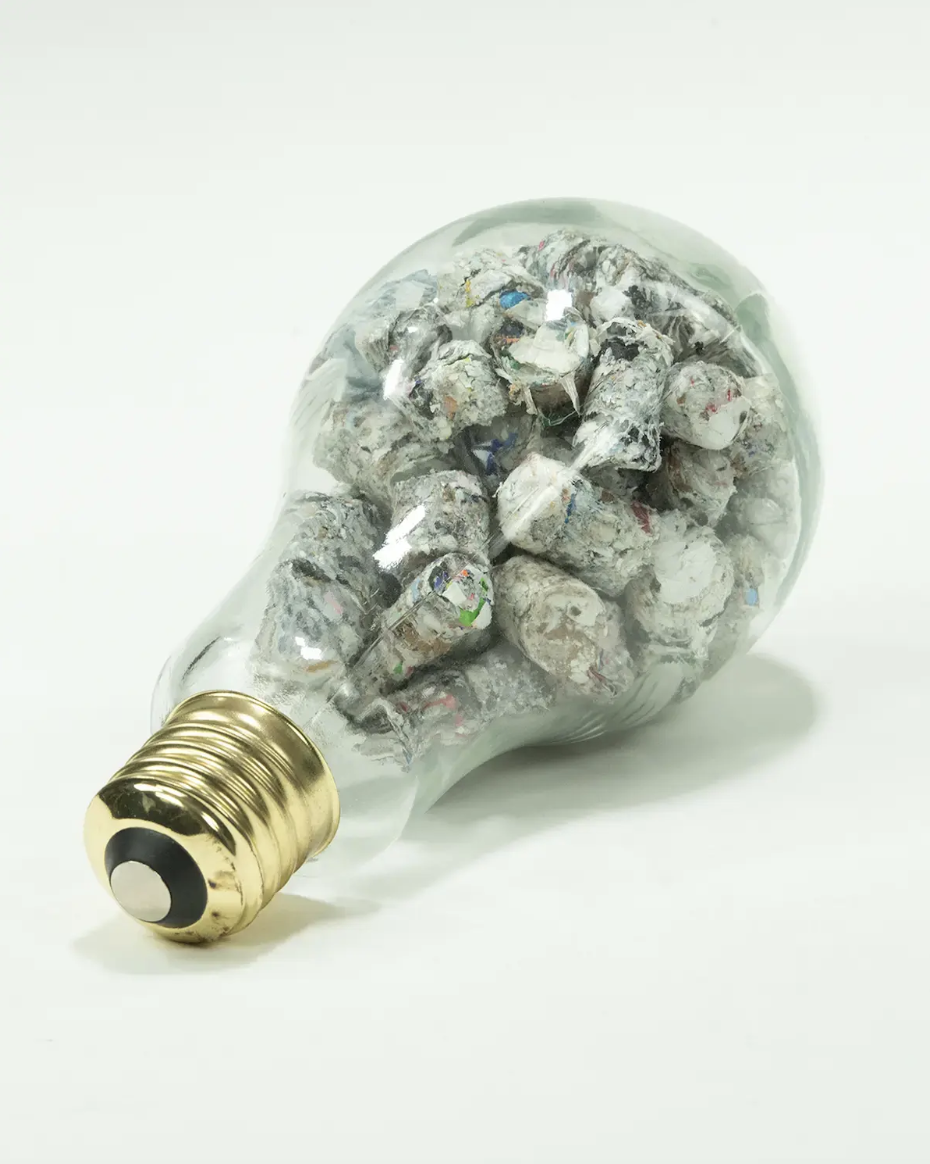
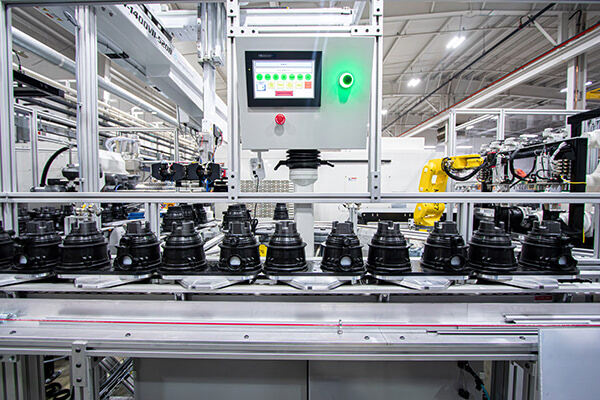
Future Sustainability Goals
- Further reductions in energy consumption through targeted conservation efforts
- Expanding waste reduction strategies to focus on zero-waste operations
- Integration of advanced technologies to ensure consistent, cutting-edge sustainable injection molding
Kaysun has diverted 3 million pounds of plastic waste from landfills — and counting!
0
LBS
Measurable Results
Visit our Sustainability Culture page to get more statistics and info on our landfill diversion achievement and future goals, energy conservation efforts, and internal initiatives!
By choosing Kaysun as your injection molding partner, you’re assured of top-quality complex parts and shaping a more sustainable future for your industry and our planet.
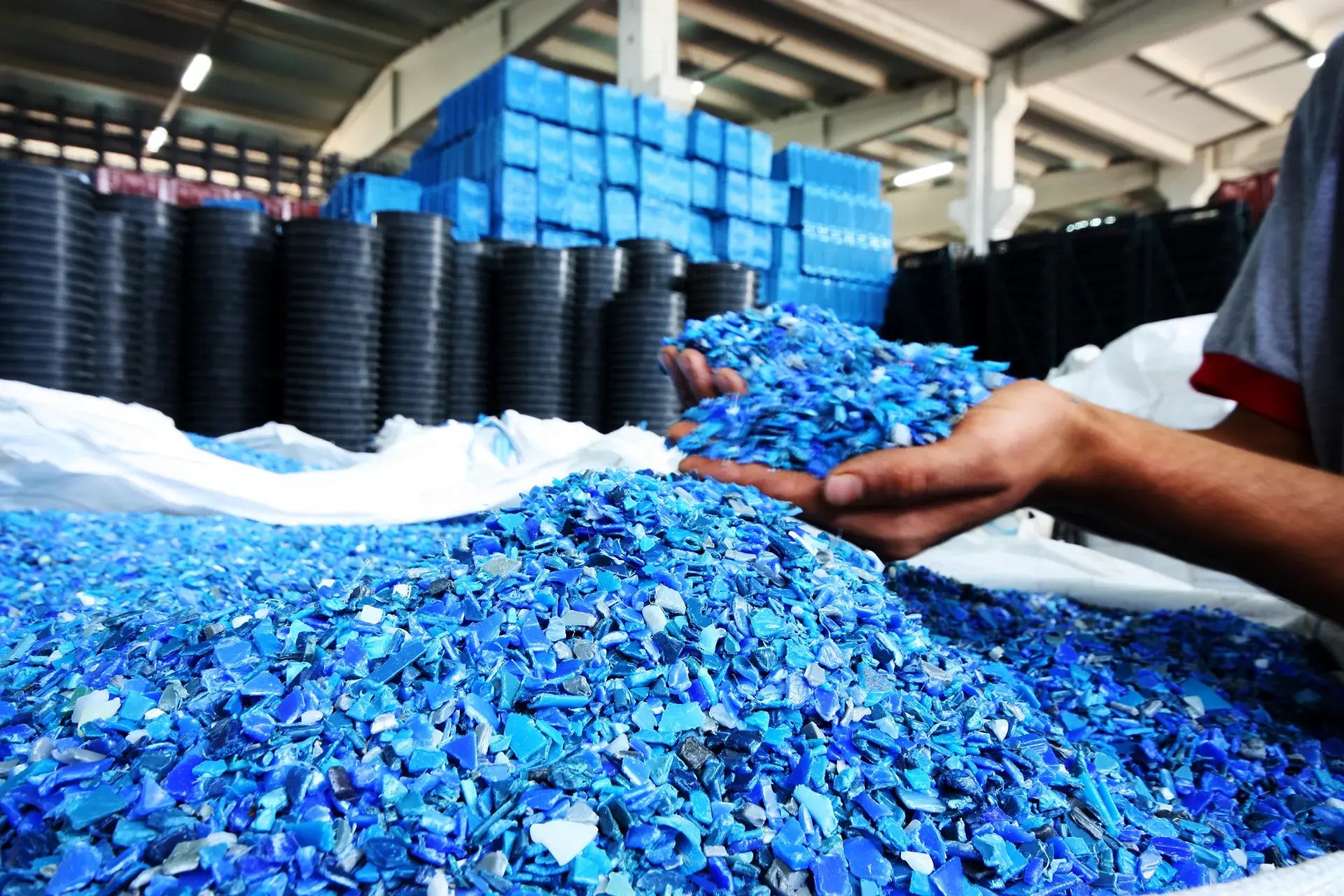