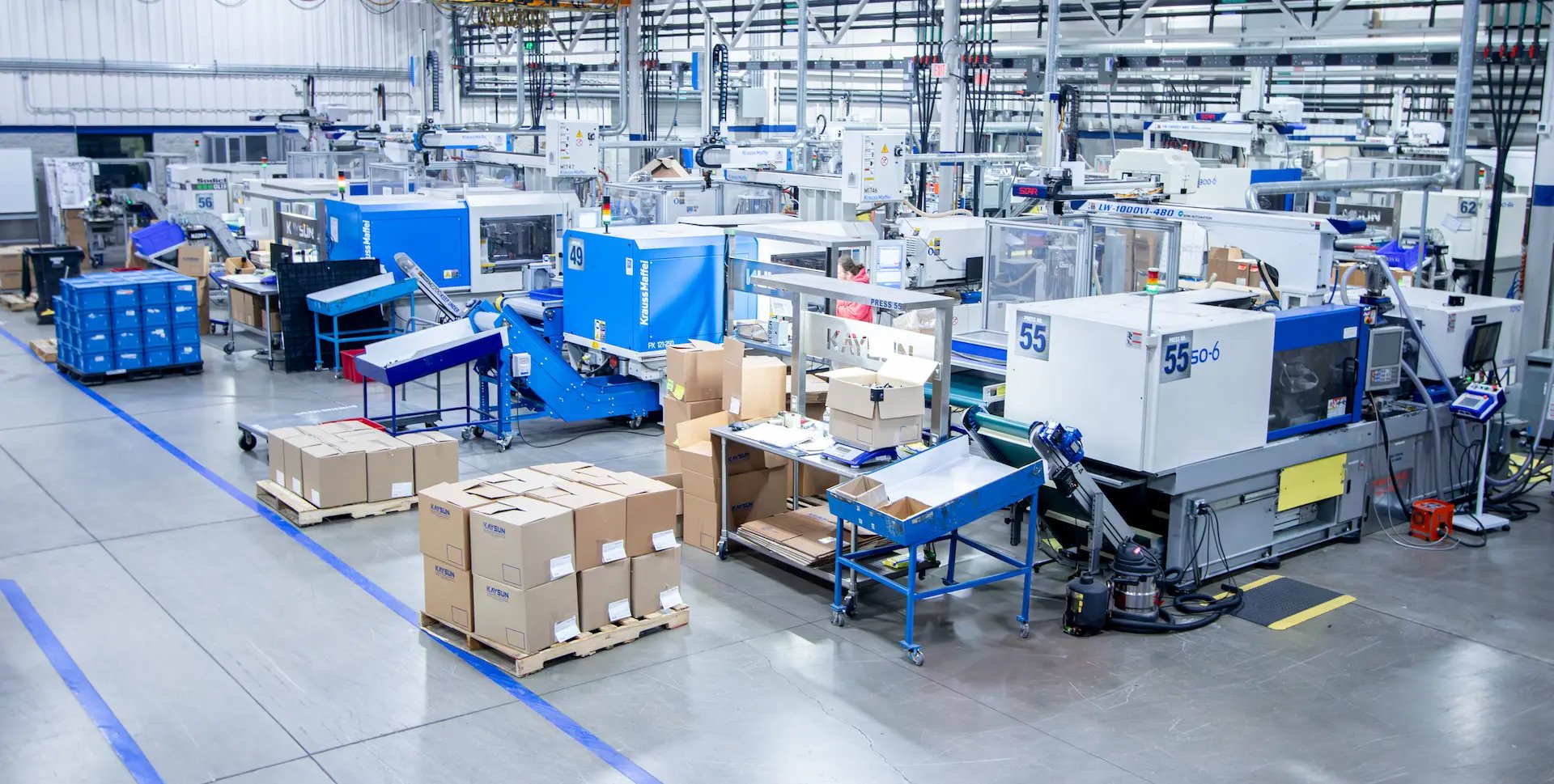
Industrial and Critical-Use Injection Molding Part Histories 3 Solutions To Complex Design And Production Challenges
Partnering with an injection molder that can solve design, engineering and materials issues is a top priority for OEMs focused on consistent product quality, safety and performance.
Our collection of Industrial and Critical-Use Injection Molding Part Histories details how Kaysun engineers helped manufacturers in three different industries develop innovative solutions to complex design and production challenges that leveraged:
-
Design for Manufacturability (DfM), mold fill analysis, materials selection, TPE/overmolding and advanced tooling to re-engineer a wearable hazardous gas detector
-
Metal-to-plastic conversion, Design for Manufacturability (DfM) and high heat thermoplastic injection molding to bring a kitchen faucet valve body into compliance with water cleanliness standards
-
Design for Manufacturability (DfM) and front-to-back automation of molding, post-production assembly and testing to prevent inconsistent compressed air distribution in a heavy truck dash control valve body
Complete the form to read more about these innovative injection molding solutions and see how they could help improve your next project!