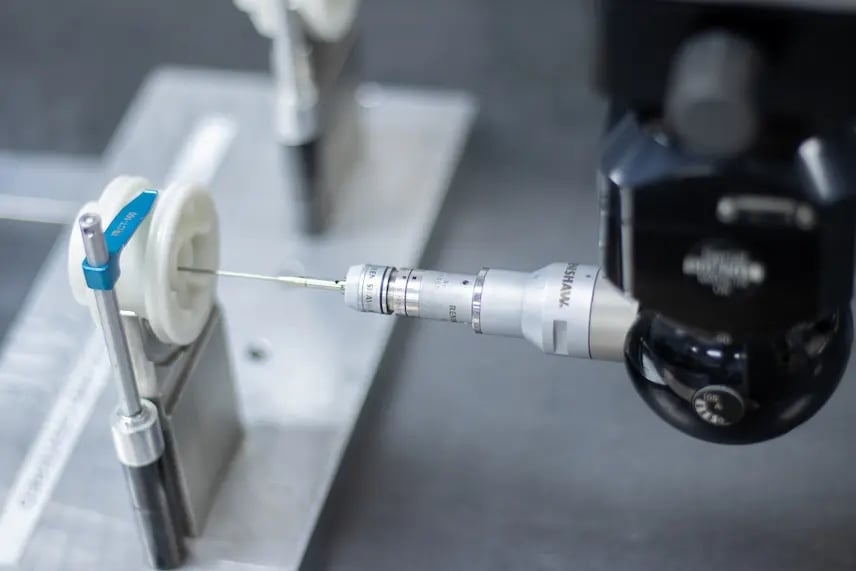
6 Steps to Improved Program Flow: How Injection Molders Impact Outcomes
A full-service custom injection molder that is committed to rigorous due diligence can help optimize molding processes and outcomes through:
- Consolidation of injection molder capabilities, functions, and supplier relationships
- A familiar project process flow that uniformly captures critical program information and data pertaining to expectations, testing, qualification, and results
- Repeatable production that helps prevents costly modifications or inspection delays that would otherwise add weeks to a program timeline and negate ROI
Kaysun has developed a 6-step Framework That Adds Value While Keeping Programs and Partnerships On Track
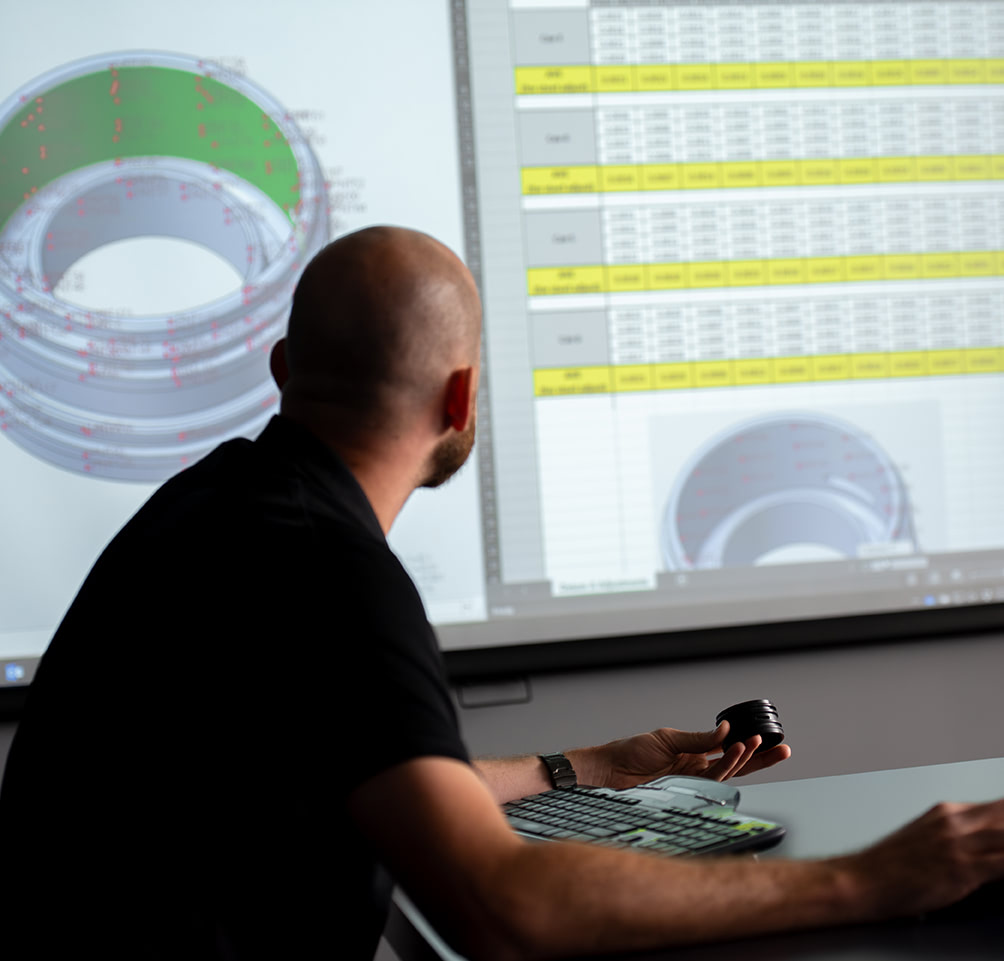
STEP 1 Design Feasibility Review
An experienced injection molder starts at the beginning, asking the fundamental question:
Can the design be produced?
To get the answer, Kaysun systematically dissects the design.
Desired part tolerances are compared against industry standards and any prior data gathered on similar parts.
Materials are verified or substituted to ensure full compatibility and optimal part performance.
The part design is thoroughly reviewed to authenticate part moldability as it relates to wall thickness uniformity, adequate draft to eject/ejecting parts from tools, and proper undercut management to alleviate part trapping.
Step 2 DfM With Moldfilling Analysis
Design for Manufacturability (DfM) with moldfilling analysis is a comprehensive study used to find practical solutions to program impediments that could jeopardize successful outcomes.
On-screen 3D design simulation that facilitates:
- Visualization of how a material will fill the mold and any potential issues (e.g., trapped air or misaligned flow fronts)
- Quality prediction of mechanical properties using color-coded outputs to identify part quality and potential failure mechanisms
- Warp/shrink studies to determine how parts react after ejection
- Design adjustments based on analysis results, using iterative cycles until both the customer and injection molder are satisfied
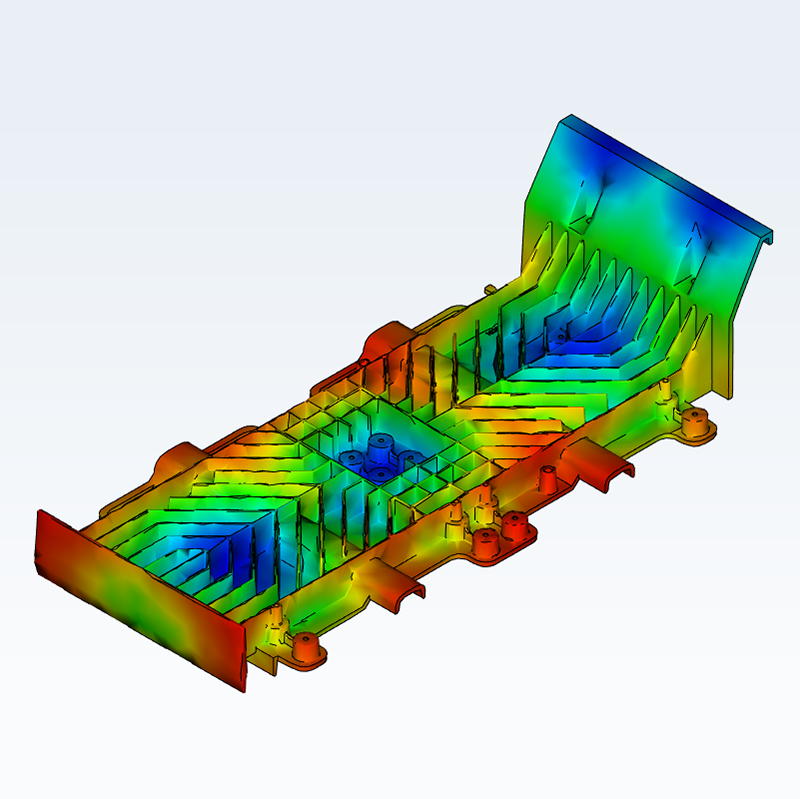
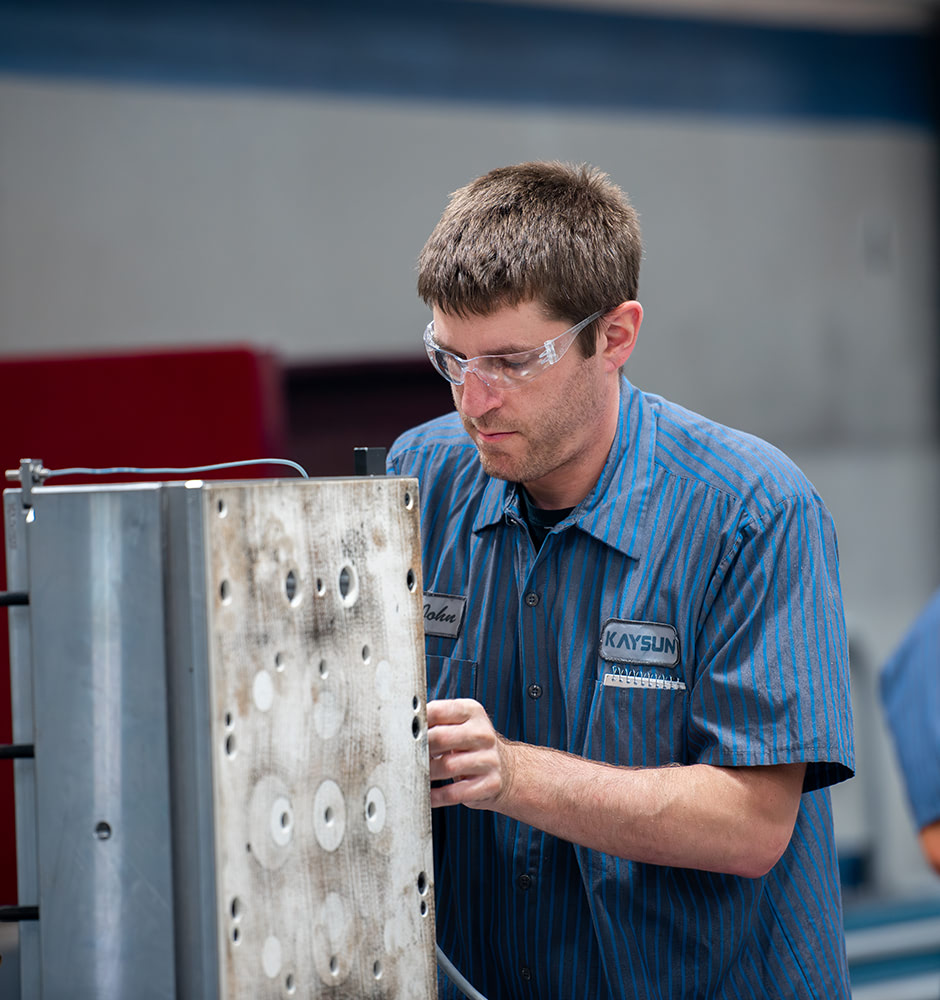
Step 3 Tool Design & Build
Tooling is one of the largest investments in an injection molding program, warranting dedicated consideration. Kaysun has a network of toolmakers to collaboratively build, quality, and refine tools:
Kaysun develops and provides design direction to the toolmaker that details steel-safe dimensions, gate location, cooling, strategic insert location/materials, ejection design, and surface finish.
Kaysun is responsible for reviewing and approving the toolmaker’s design and sharing it with the customer.
Using equivalent measurement methods and inspection report data, Kaysun and the toolmaker independently verify critical part dimensions in the tool and eliminate redundancies.
Kaysun and the toolmaker collaborate on monitoring the physical tool build, sharing timely information and scheduling physical inspections to ensure specifications are met.
Step 4 Establish Scientific Molding Process
An injection molder experienced in tool design and process optimization employs scientific molding methodologies that ensure injection molding process repeatability and precision.
Scientific molding ensures repeatability in production. Design of Experiments (DOE) — a specific applied statistics exercise within the scientific molding process — reduces cost by establishing an optimized molding process that allows for identification and correction of tooling problems prior to production.
A certified master molder leverages scientific molding and DOE to develop the optimal injection molding production process that incorporates RJG pressure-sensing technologies, documentation of intended molding equipment, and electronic data gathering/application that ensures process repeatability and part reliability.
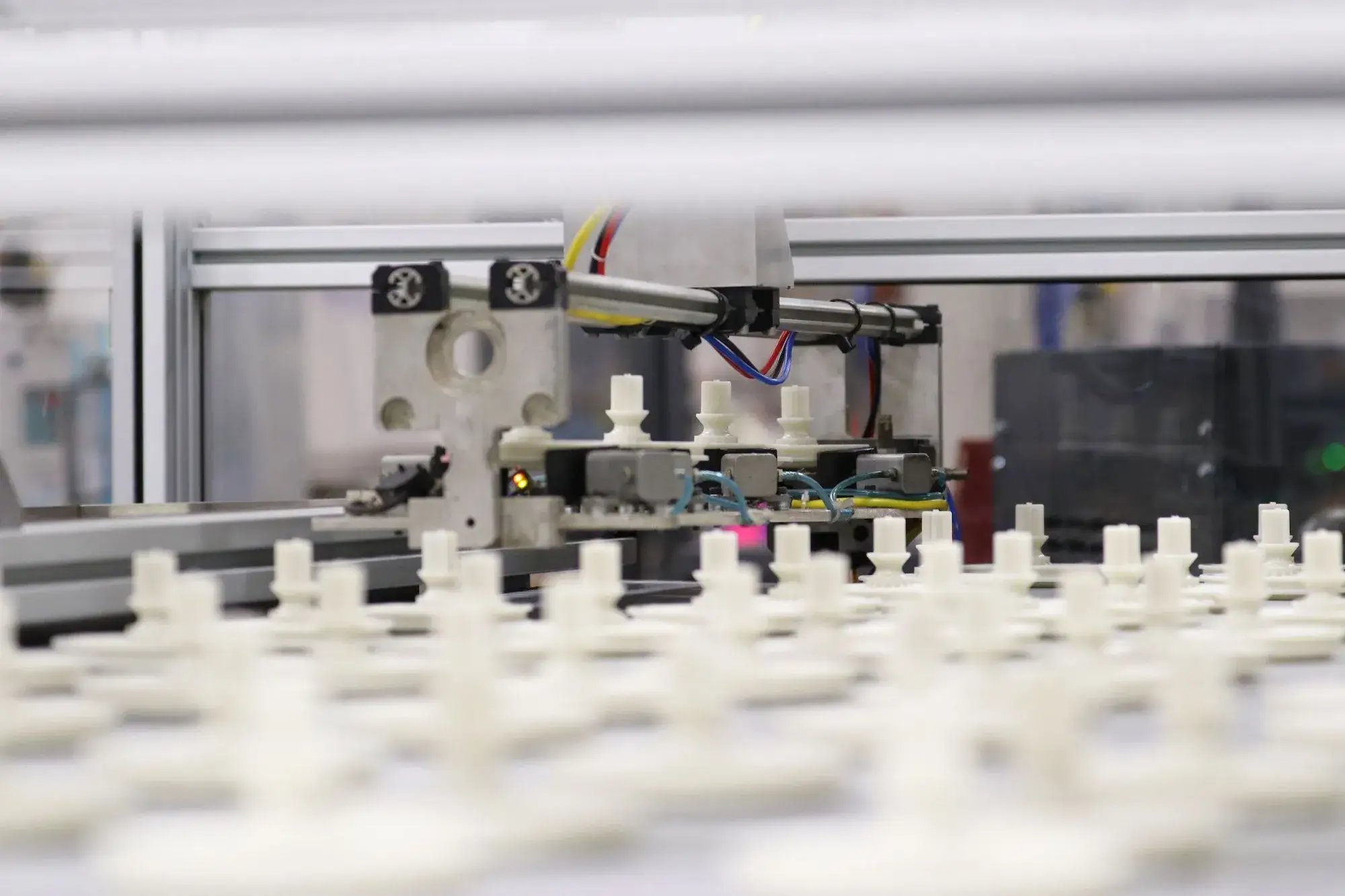
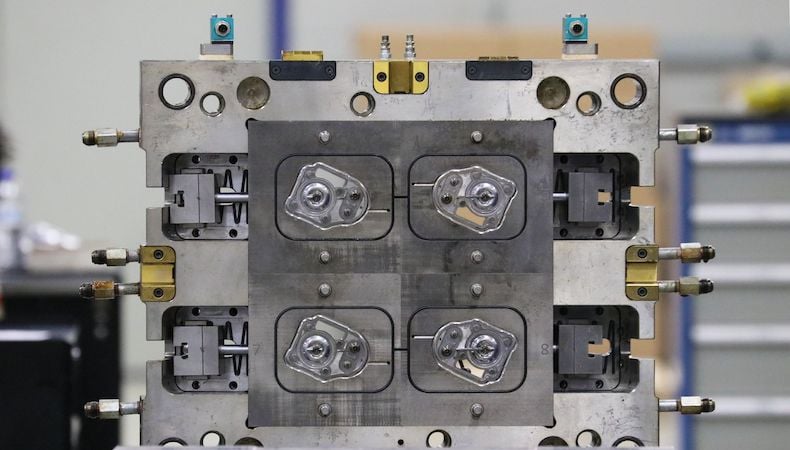
Step 5 Adjust Tool Steel & Qualify Part
Once the tool is received from the toolmaker and the optimal process has been determined, Kaysun conducts a first run of the part to determine whether the part meets specifications.
Measuring first-off parts against desired dimensions may require iterative sampling and tool adjustments to compensate for actual activity. Few molders can accomplish refinements in-house but those that can, like Kaysun, provide time- and cost-saving efficiencies:
When tooling and product samples meet specifications, Kaysun prepares and submits a part qualification package to the customer. The package contains essential information about the part and program that can be referenced should quality/performance issues arise, or an in-house review is conducted. Once the customer approves the qualification package, injection molding production begins.
Step 6 Maintain Optimized Process
As a full-service custom injection molder, Kaysun provides value at every touchpoint. An optimized molding process built in partnership with Kaysun and around scientific molding provides several key, ongoing advantages:
- Electronically stored and controlled molding process that ensures qualification and consistency across all production runs
- In-tool pressure sensors that provide real-time feedback to machine controllers that systematically mitigate risk before it causes costly problems or setbacks
- A control plan that measures and electronically stores critical capability data on a continuous basis
- Responsive, specialized customer service to strengthen and add value to Kaysun customer relationships
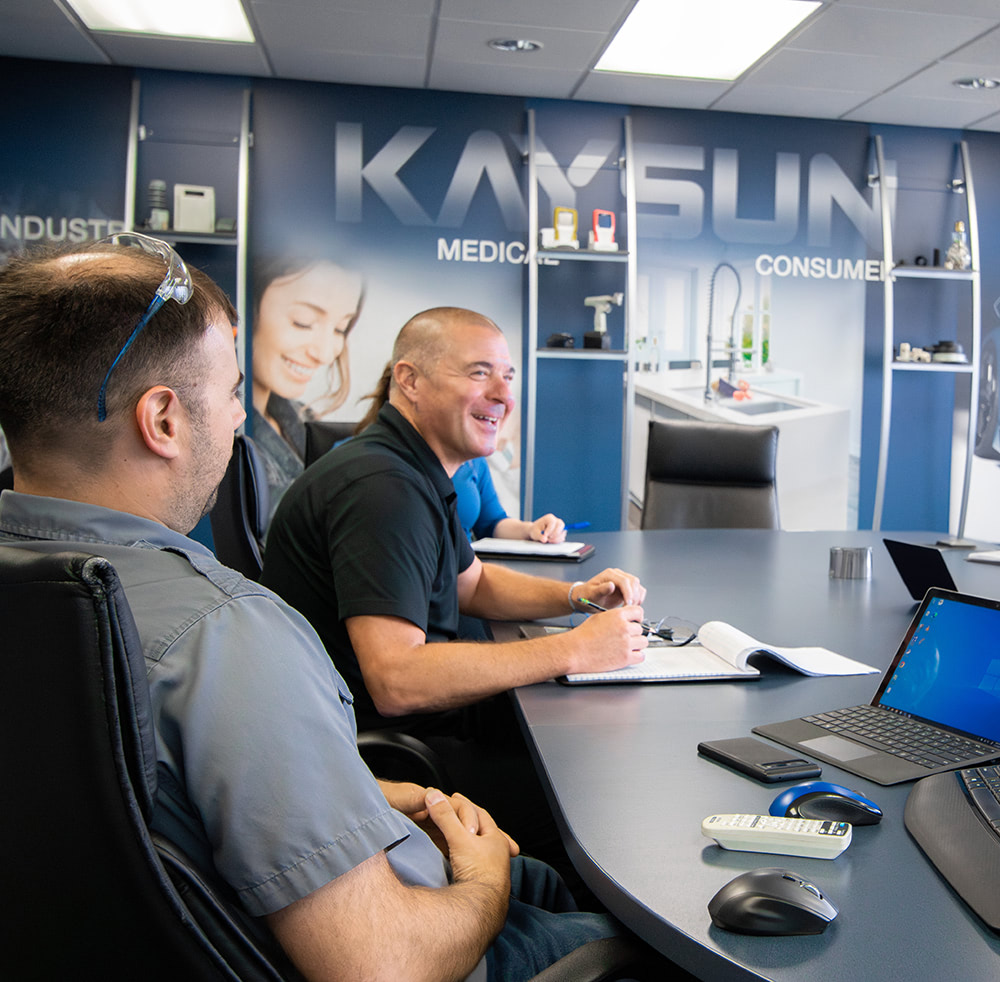
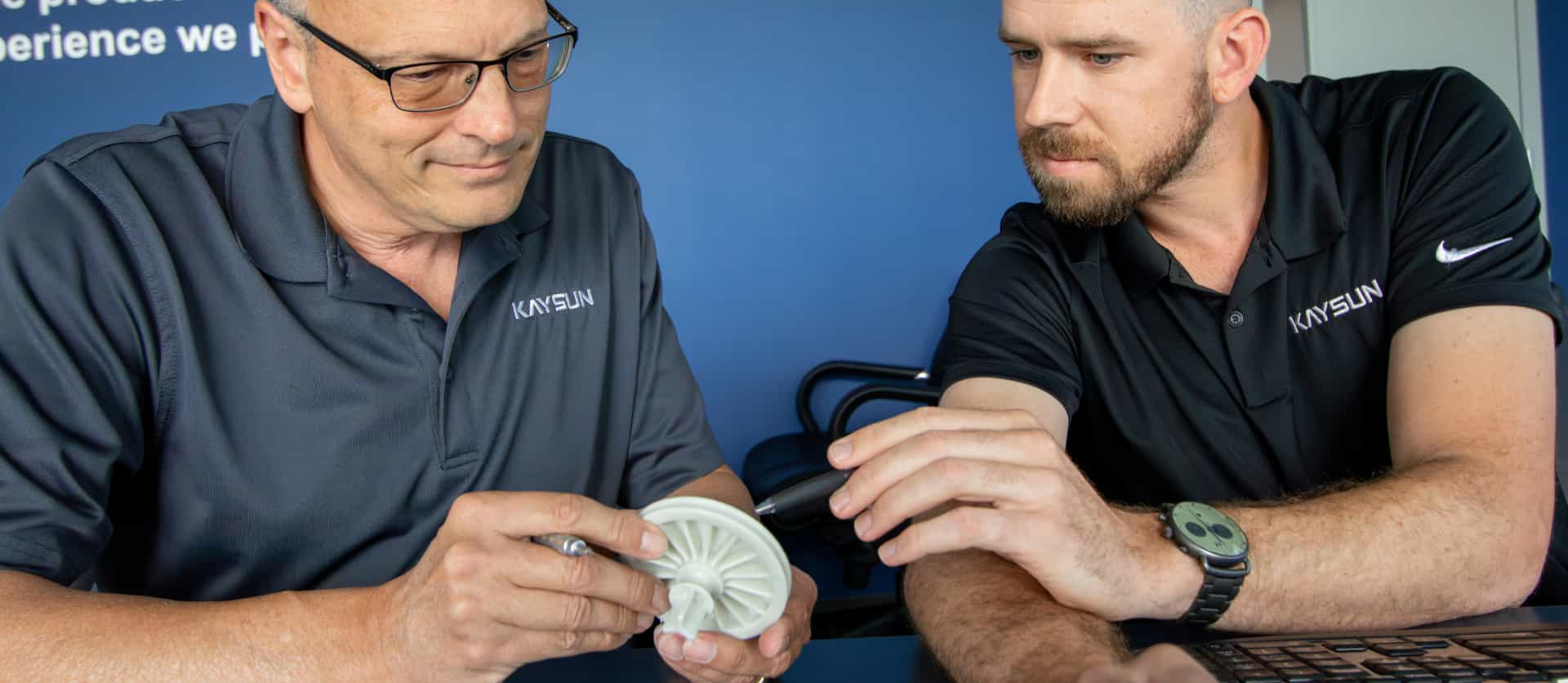