The Basics of Value Stream Mapping for Manufacturers
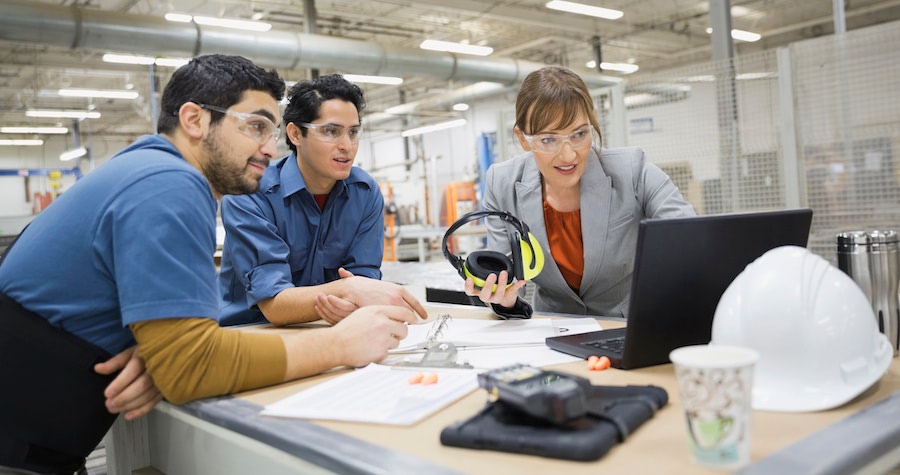
In the manufacturing world, “lean” principles reduce inventory and work in process, improve quality, boost productivity, and ultimately lower costs. Lean originated in Japan decades ago and has been readily embraced in manufacturing sectors around the world, especially the automotive industry.
With increasing global competitiveness, lean principles have never been more important for making U.S. companies competitive. One of the most simple yet effective lean tools is value stream mapping, which can be implemented within days and can reap impressive results in a short period of time.
Steps for Implementing Value Stream Mapping
Value stream mapping is a low-tech, pencil-and-paper tool that enhances communication, business planning, and overall management. It can be applied to any industry, across a wide range of departments.
What's the purpose of value stream mapping?
When done right, value stream mapping removes waste from a manufacturing process and makes it as lean and efficient as possible. The “value stream” identifies all the actions and steps that a product takes throughout a manufacturing process, starting with obtaining raw materials all the way to final delivery of a product.
The first step is to draw — on a single document — a detailed picture of all the parts of the operation to produce a "current state map" to help you visualize the situation as it exists today. It's important to map out the entire manufacturing process, including:
- Cycle times
- Down times
- In-process inventory
- Material moves
- Information flow paths
- And more
Once the value stream is identified, steps are taken to optimize and streamline the manufacturing process, resulting in the creation of a “future state map” that eliminates waste and utilizes time, talent, and equipment more efficiently.
The third and final step is implementing the process improvements, which leads to reduction of work in progress and production lead times, fewer defects, and faster responses to change requests. Results are often immediate and dramatic, adding value to your products and services that help set you apart from the competition.
A Team Effort
Lean is all about eliminating waste, or the non-value-added components in any process. A process is a process, whether it’s in a factory or a professional office building. And usually every process has some element of waste.
Value stream mapping identifies all the actions that take a product through any process — that process can be in production, procurement, facilities management, HR, administration, delivery, customer service, vehicle maintenance — you name it.
It is important that value stream mapping is embraced at all levels of the company. Management must demonstrate that every employee is encouraged to contribute to productivity by facilitating positive change. This allows employees to have more “ownership” of the company, which also results in a better understanding of the entire business operation for everyone involved.
Take a Continuous Improvement Approach
Value stream mapping is just the first step of an on-going lean experience. Lean never ends — ideally it becomes part of the corporate culture, a process, a way of thinking. Most lean consultants agree that a process is not really lean until it has gone through at least seven periods of value-stream mapping.
Any time is a good time to start to get lean. Value stream mapping is easy to understand and implement, and relies on common-sense, low-tech ideas. It is also relatively low cost — depending on your budget, out-of-pocket expenses can be as little as $200 for a few books, or tens of thousands of dollars per year for consultants, training, and related improvements.
Taking a lean approach in each phase of production results in projects done on time and on budget. Learn more about streamlining the development of complex plastic components in our eBook, 5 Steps to Get New Injection Molded Products to Market Faster.
Subscribe
TO OUR BLOG
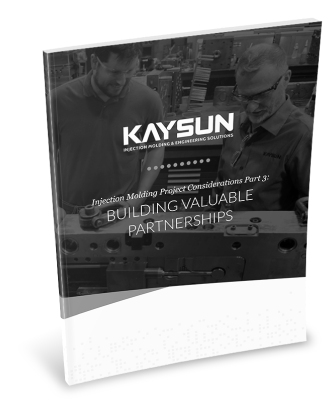
How Do Injection Molder Partnerships Influence Project Costs?
You Might Also Like...
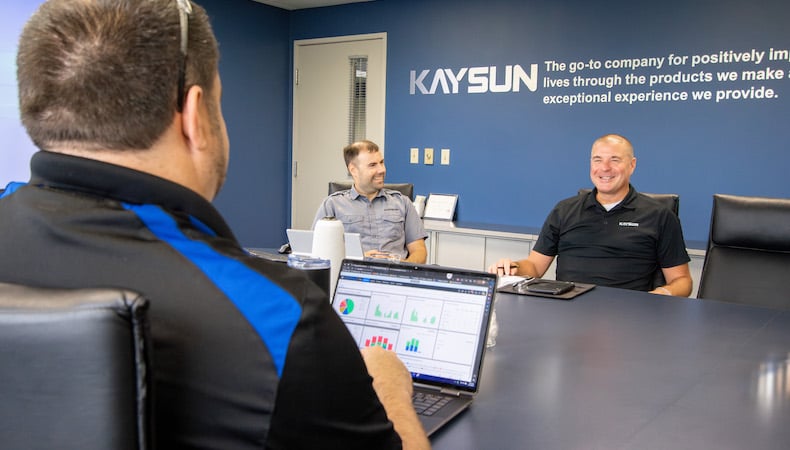
Top 3 Custom Injection Molding Trends to Watch in 2025
Despite being considered more energy efficient and producing less waste than other…
READ MORE
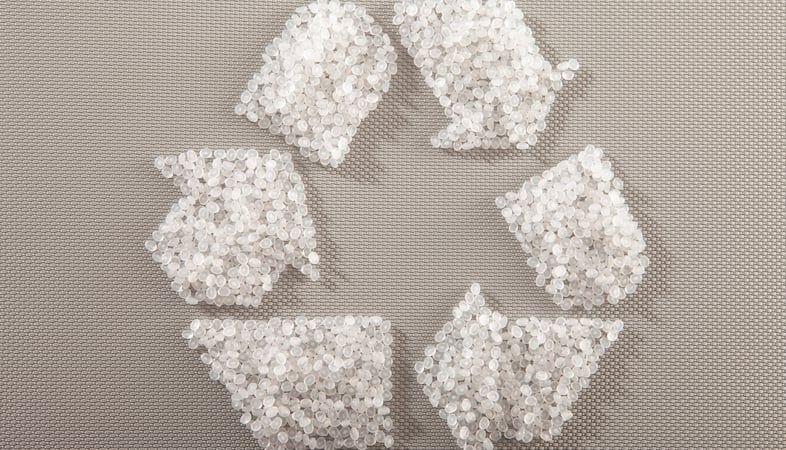
How Kaysun’s Culture of Sustainability Benefits OEMs and The Planet
Injection-molded parts and products are staples for OEMs in industries ranging fro…
READ MORE
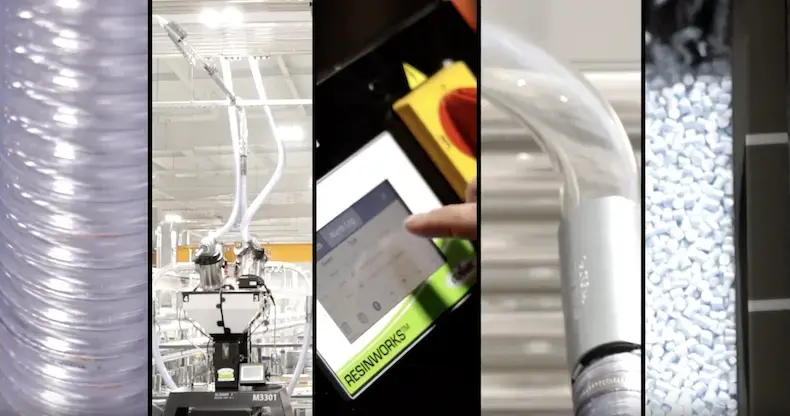
How Centralized Material Handling Streamlines Injection Molding
We consistently look for new ways to deliver timely service and top-quality parts …
READ MORE