Are Commodity Injection Molders a Value-Add for Medical OEMs?
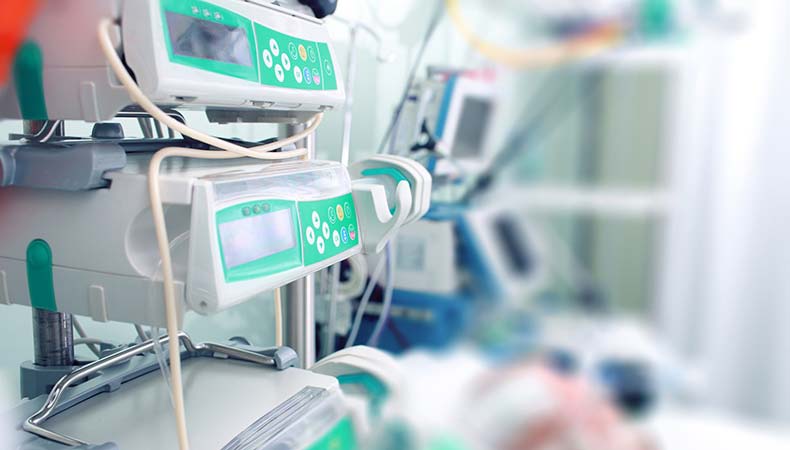
Price point is rarely, if ever, synonymous with value, yet it’s not unusual for OEMs in competitive industries like medical and healthcare equipment to base vendor relationships solely on the bottom line. It’s also not unusual for those short-term gains to turn into expensive long-term losses.
For medical device and equipment manufacturers, there is inherent risk in using commodity injection molders for such critical-use products. On top of risking their reputation by using injection molded plastic parts of lesser quality and functionality, there are stringent regulatory protocols like ISO 7 or ISO 8 clean room and ISO 13485 that commodity molders are not certified or equipped to handle.
Compliance — or lack thereof — is an imperative aspect of a commodity molder partnership that medical OEMs need to consider, but it’s not the only one. There are also potential hidden costs that they may have to absorb to correct oversights in the following critical areas:
Design and Engineering
Tight tolerances, sometimes within +/- .001 inches are necessary for proper quality and functionality in complex medical device components. However, consistently achieving them often means making adjustments in the design phase to compensate for the impact of production and assembly processes. With commodity injection molders, you may not have this level of design input, resulting in ill-fitting components or poorly performing devices that require production re-runs or worse, need costly repairs — all of which equates to time and money you can’t afford to waste.
Injection Molding Materials
Like design, having little or no control over the supply chain is a very real possibility with commodity injection molders. This not only compromises your ability to leverage supplier expertise to streamline processes and speed time to market, it can also jeopardize product quality. For medical devices, proper attention must be given to specialized coatings like antimicrobial surfaces, or overmolded grips that can withstand frequent handling and the harsh chemicals used for sanitizing in medical environments. Any deviation in the chosen resin(s) increases the risk of product defects and, ultimately, costly warranty claims.
Secondary Operations
Often, complex medical devices require additional assembly or finishing work like welding, painting or buffering. If done poorly, or without appropriate design, it can cause small components to break or may introduce irregularities in wall thickness that cause short- and long-term component failure. In addition, if your injection molded plastic parts require multiple changeovers, there is the very real danger of damage or defect caused by machine mounting and additional handling.
Transportation
If your plastic components can’t get to their desired destination on-time and defect-free, there’s no value in a commodity molder partnership. Paying for expedited delivery in addition to product rework to get exactly what you need for your medical device negates any savings that initial low price point suggested.
Intellectual Property Protection
This is particularly important if you choose to partner with an overseas commodity injection molder — you may be unknowingly giving up your legal rights afforded in the United States to registered and trademarked designs and products. Some overseas markets disregard these protections and may produce lesser quality items from plagiarized designs for mass distribution, putting downward pressure on price points — and your company’s long-term profits.
The disparity between price point and the actual cost of the considerable risks that medical device OEMs assume in working with a commodity molder reinforces the true value of partnering with an experienced complex injection molding partner that can contribute scientific molding, engineering/design support, and other expertise to help ensure successful outcomes.
To learn more, read our latest resource specifically for engineering and advanced sourcing professionals: The Ultimate Guide to Medical Parts Manufacturer Selection. Click the button below to access your free copy!
Subscribe
TO OUR BLOG
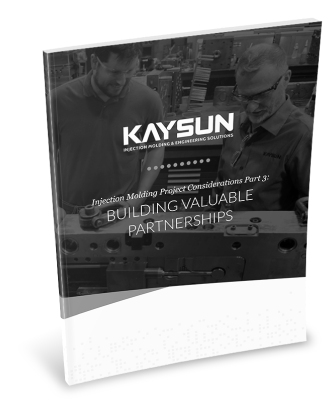
How Do Injection Molder Partnerships Influence Project Costs?
You Might Also Like...
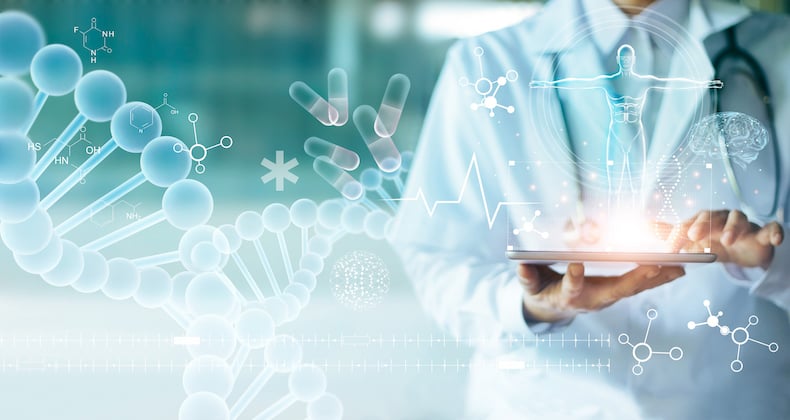
How MD&M West 2024 Keeps MedTech Professionals Ahead of the Curve
MD&M West is one of the largest and most respected medical device trade shows …
READ MORE
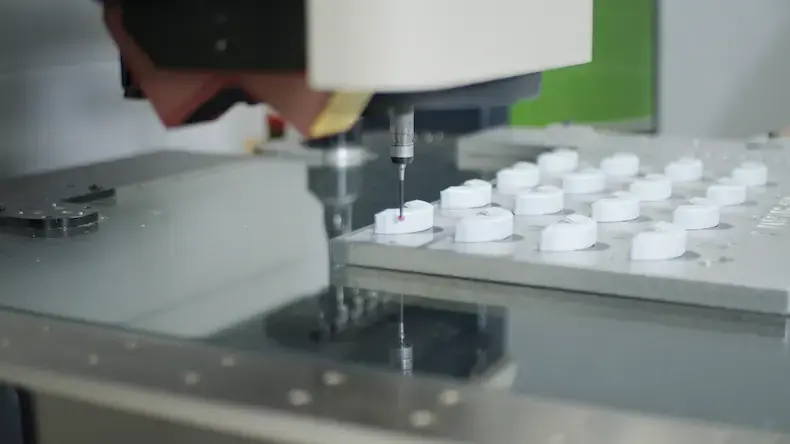
How MedAccred Accreditation Helped Kaysun Enhance Processes & Quality Systems
When you operate at the top of your game, reach higher. Kaysun had already shown i…
READ MORE
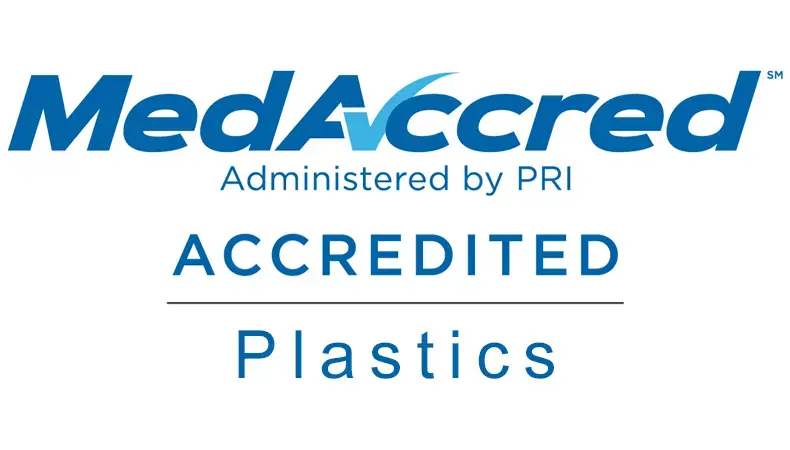
Why Ongoing MedAccred Accreditation Matters to Medical Manufacturers
Kaysun's commitment to excellence is well documented through its certifications, i…
READ MORE