The Future of Medical Injection Molding – 2018 and Beyond
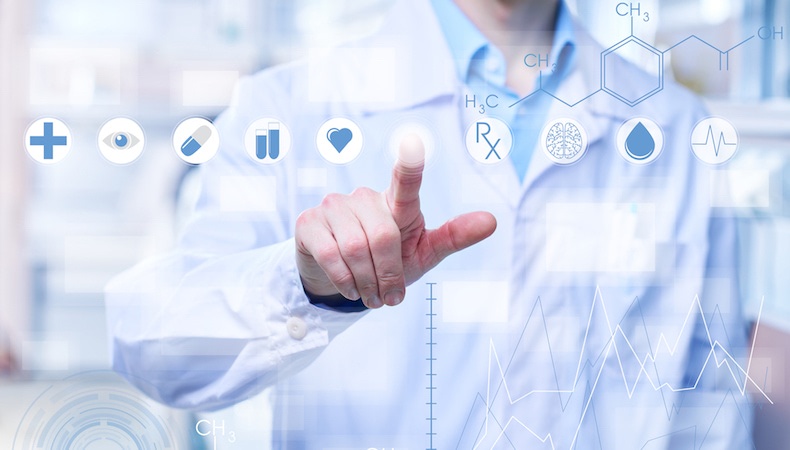
Advancements to polymers and injection molding technologies have contributed to widespread adoption of plastics in the medical industry. All segments of the medical industry have embraced the benefits of plastics, and are looking to incorporate more plastic in their designs in 2018 and beyond. Low cost plastics, for example, have enabled the creation of disposable plastic instruments, syringes, gloves and gowns that, in turn, help reduce the spread of infections within the hospital environment. Plastics have also replaced glass in a variety of laboratory consumables, improving lab safety while reducing consumable costs.
Likewise, high performance polymers contribute to the longevity and friction-free movement found in current generation artificial joints. Handheld medical devices and instruments also use plastics to reduce device weight, improve functionality and/or lower device cost.
The current plastics revolution in the medical industry shows no signs of slowing down, as ongoing research into innovative polymers, improved processing techniques, and novel post-processing technologies are expanding the possibilities for plastics' use in medical devices and components.
An Ever-Changing Process
Injection molding processes continue to evolve. At the design stage, rapid prototyping allows molders to create physical prototypes to verify form, fit and function before finalizing the mold design. Advancements in mold simulation software give molders a detailed look into mold filling and helps to identify issues early in the design phase.
Advancements in control technologies improve repeatability and gives better control over process variables, which translates into precise molding of even the most intricate parts. Together these molding technology advancements shorten product development time, reduce development costs and open the door to a range of new applications.
The Growth of Polymer Science
Polymer science continues to be an exciting area of development in the field of medical injection molding. New materials and additives increase stability, reduce shrinkage and introduce other properties that improve performance in molding applications. Additionally, the mechanical strength of polymers continues to evolve, allowing them to be viable substitutes for metals in a range of applications.
Beyond the physical properties of the materials, next-generation polymers are being formulated to incorporate unique functional properties, such as antimicrobial materials in injected molded plastics that inhibit bacterial growth on the molded part.
Pharmaceutical Plastic Research
Another growing area of research for injection molders is pharmaceutical plastics. These plastics are suitable for ingestion or implantation, and provide a controlled release of medicine into the host. Bioresorbable polymers, for example, can dissolve or remain in the body, help support bone/tissue growth, or be used in the manufacture of dissolvable stents.
Internet of Things (IoT)-Integrated Medical Devices
Given the steady growth of the in-home medical device sector and new advancements in medical technology, injection molded plastic medical devices play a key role in IoT-enabled med tech today. From things like telemedicine to wearable or portable medical devices that collect personal data and notify a doctor or family member in the case of an emergency, monitoring patients from home has become much easier thanks to today’s IoT integrations. As more people look to self-managed care, the need for internet-connected medical devices and wearables will only grow, along with the need for high-quality plastic designs.
Post-Molding Processes
The development of various post-molding processes further expands the suitability for plastics' use in the medical industry. Processes like ultrasonic welding and laser micro-machining continue to evolve and are compatible with a range of medical plastics. These secondary operations simplify assembly of complex plastic components and provide new possibilities for device designers.
The future for medical injection molding is bright. At Kaysun, we understand the needs of the industry and maintain a strong commitment to the medical device field, as evidenced by our MedAccred Plastics accreditation and deep experience in designing and processing parts with a variety of medical grade polymers.
Our whitepaper, The Importance of Scientific Molding in Medical Device Manufacturing, details how an experienced injection molder like Kaysun can improve upon an existing medical device or component, or help bring a new product to market in an industry that demands quality, precision, and performance. Click the button below to access your copy now!
Subscribe
TO OUR BLOG
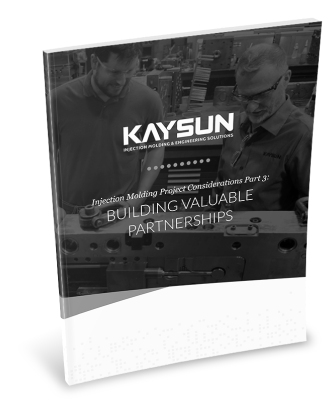
How Do Injection Molder Partnerships Influence Project Costs?
You Might Also Like...
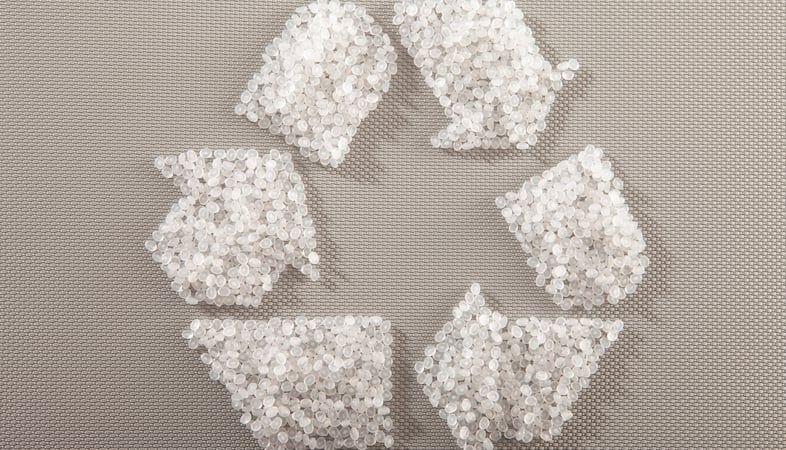
How Kaysun’s Culture of Sustainability Benefits OEMs and The Planet
Injection-molded parts and products are staples for OEMs in industries ranging fro…
READ MORE
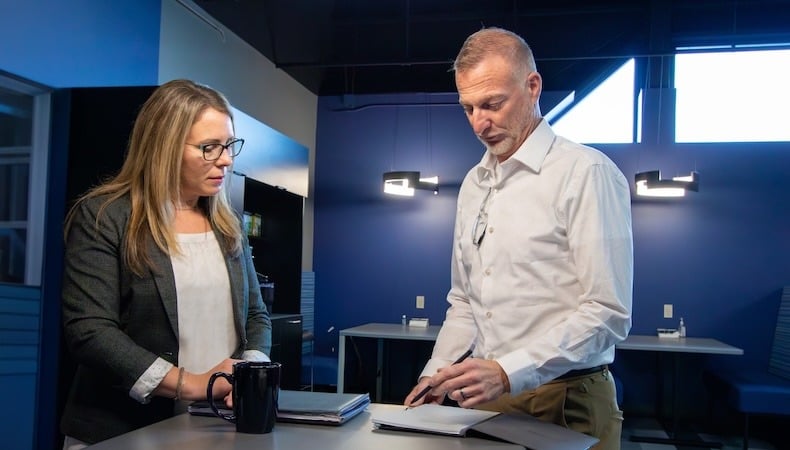
12 Common Injection Molding Questions — Answered!
Injection molding is a versatile and precise process, making it ideal for OEMs tha…
READ MORE
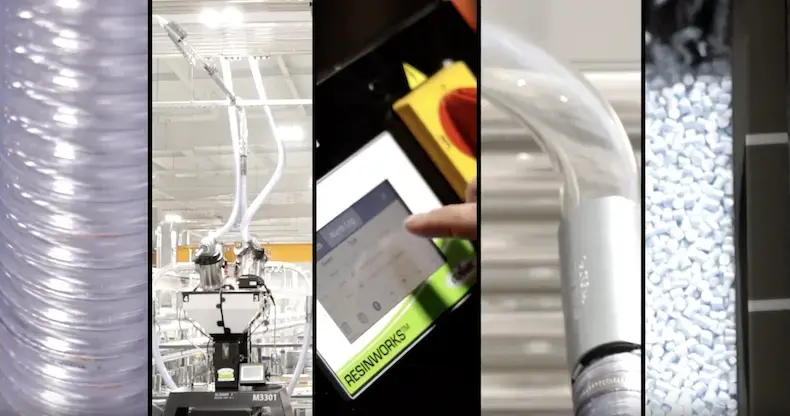
How Centralized Material Handling Streamlines Injection Molding
We consistently look for new ways to deliver timely service and top-quality parts …
READ MORE