Molding Medical Plastic Parts That Outperform Expectations
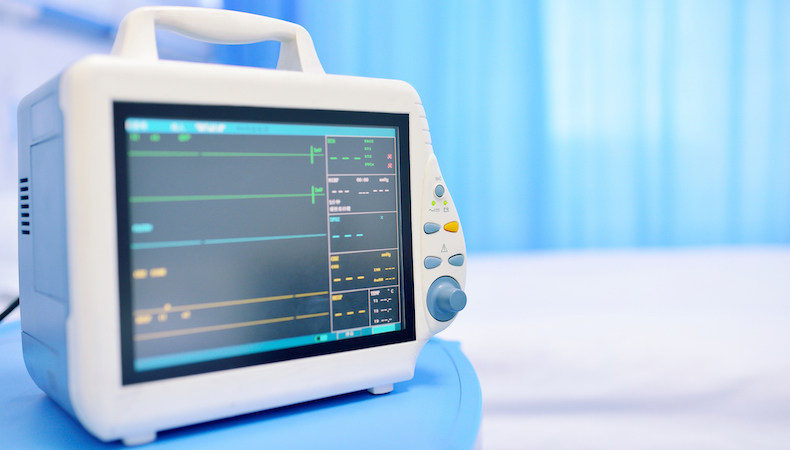
Medical plastic parts are among the most nuanced applications produced by custom injection molders. The complex nature of medical devices present unique design and engineering challenges, often starting with appropriate plastic selection.
There are a number of factors that guide plastic selection for medical applications, but when it comes to the plastic design and manufacturing specifics of your particular medical project, questions might arise as to the best choices.
Partnering with an experienced custom injection molder — especially one with MedAccred Plastics accreditation, like Kaysun — helps to ensure quality outcomes for medical plastic parts. However, familiarizing yourself with the types and grades of plastics most commonly used in medical applications is ideal for fostering meaningful communication between you and your molder while making key decisions.
Thermoset? Thermoplastic? Does It Make a Difference in Medical Plastic Parts?
Despite the many thousands of plastics available, they all fall into two main types: thermoset or thermoplastic. The terms sound similar and both are appropriate for many applications but there is a notable difference in chemical behavior during processing.
- Thermosets (e.g., liquid silicone rubber (LSR), epoxy, phenolic) harden permanently on cooling and cannot be reshaped or re-melted.
- Thermoplastics (e.g., thermoplastic elastomer (TPE), high-density polyethylene (HDPE), acrylonitrile butadiene styrene (ABS)) become plastic on heating and harden when cooling, without changing plastic chemistry. Thermoplastics can be re-melted, reused, and recycled.
Knowing this basic difference is generally helpful in understanding — and ultimately selecting — the appropriate engineering grade plastic for medical plastic parts.
Amorphous Plastic
“Amorphous” refers to a thermoplastic that has randomly oriented polymer chains and, as such, lacks a clear structure. These characteristics are advantageous in that amorphous plastics soften over a broad range of temperatures, are easily thermoformed, and bond well with adhesives and solvents. On the other hand, amorphous plastics are vulnerable to stress cracking and offer poor chemical resistance.
A high-performance amorphous plastic medical OEMs commonly use is Udel Polysulfone (PSU), which is a high-strength plastic alternative to stainless steel and glass in medical applications. Medical grade PSU is capable of withstanding repeated steam sterilization, and is highly resistant to a variety of hospital chemicals, oxidation, hydrolysis, mineral acids, alkali, and salt solutions.
Semi-crystalline Plastic
“Semi-crystalline” denotes plastics with densely packed polymer chains. Because of the orderly polymer structure, semi-crystalline plastic has good stress fatigue resistance. However, it also has a sharp melting point, difficulties in thermoforming, and poor adhesive and solvent bonding.
Polyetheretherketone (PEEK), for example, is a popular semi-crystalline plastic used in medical applications because it has excellent mechanical and chemical resistance, and can be readily sterilized by steam, gamma radiation, Ethylene oxide (EtO) and electron beam (E-beam). PEEK is also biocompatible, meaning it is readily accepted by the human body, doesn’t break down over time and can withstand X-Ray, CT and MRI scanning.
Additives and Alloys
The amorphous and semi-crystalline grade tables featured above aren’t meant to suggest that plastics selection is an all-or-nothing choice. For many applications, including medical plastic parts, non-plastic additives may be introduced to change certain characteristics to better align with need:
- Particulate fillers — mineral, silica, ceramic, carbon powder/fiber, glass microspheres/fibers, and powdered metal — can reduce costs and improve properties such as modulus, conductivity, and heat and ultraviolet light resistance.
- Reinforcing fillers — long or short glass fiber additives, carbon, stainless steel, and Kevlar fillers — improve plastics’ mechanical qualities.
Additives and alloys are particularly effective in medical applications that require consistent, long-term elimination of bacteria. For example, hip implants used to be made from metals with antimicrobial coatings. Over time, that coating would wear off. Now, ionic silver can be mixed into the plastic melt used to mold implants so the implant is continually protected by antimicrobial agents without compromising patient health or the properties of the plastics used in the implant.
The performance of injection-molded medical plastic parts and devices is of utmost importance, and plastics selection with guidance from an experienced injection molder is integral to achieving no-fail outcomes. Learn more about how project specs, plastic attributes, and molding performance influence material choices in The Ultimate Guide to Medical Device Resin Selection. Click the button below to download your copy now.
Subscribe
TO OUR BLOG
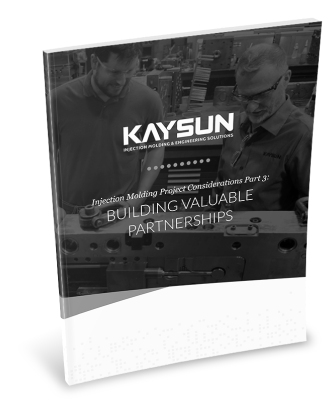
How Do Injection Molder Partnerships Influence Project Costs?
You Might Also Like...
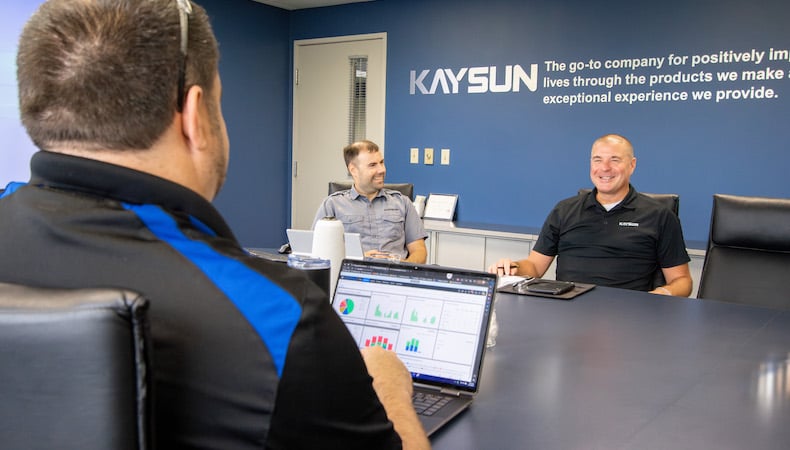
Top 3 Custom Injection Molding Trends to Watch in 2025
Despite being considered more energy efficient and producing less waste than other…
READ MORE
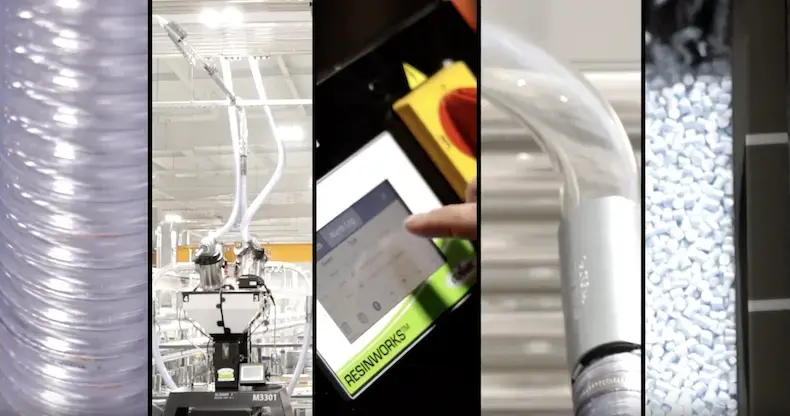
How Centralized Material Handling Streamlines Injection Molding
We consistently look for new ways to deliver timely service and top-quality parts …
READ MORE
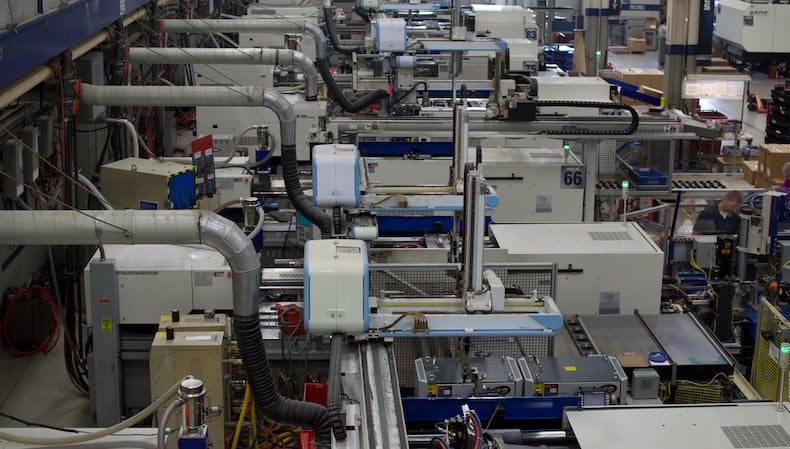
Top 14 Benefits of Injection Molding
OEMs across many industries enjoy the benefits of injection molding. It’s ideal fo…
READ MORE