5 Reasons Why Medical Device OEMs Need Full Service Injection Molders
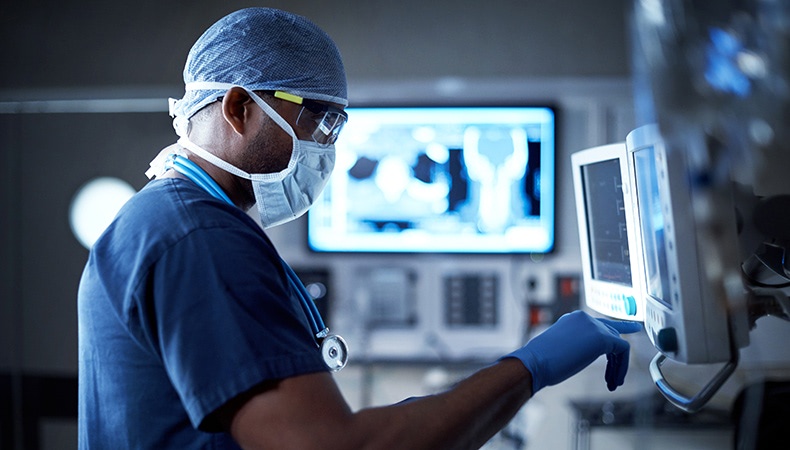
Given the promised speed and generally low price points, commodity injection molders are attractive to OEMs in many industries. However, deals struck with these molders — overseas and domestically — can pose potential problems in communication and quality, among other issues.
1. Upfront design and engineering support
Expert plastics engineers come alongside your team to identify design improvements that increase manufacturability, reduce tooling and production costs and ensure repeatability of complex medical component production. Plus, upfront design support from injection molding engineers aids in anticipating and executing design adjustments before tooling and sampling — a critical step in reducing the number of required design-build-sample iterations and getting product to market faster.
2. Secondary processes
Often, medical devices require overmolding for improved touch, shock absorbency and seal compatibility, or perhaps machining, sub-assembly or welding is needed. A full service molder offers one-source access to these types of services in addition to production, simplifying vendor management and alleviating space and labor concerns at your manufacturing facility.
3. Communication
Full service molders proactively facilitate and manage conversations and documentation to reduce lead time and prevent assumptions from being made about how modifications impact timelines, component design and other product-related outcomes. This is in stark contrast to commodity molders, where time zone disparity, shipping time and variance in standard units of measure could prevent clear, consistent directives.
4. Plastic Part Quality
Tight tolerances, critical-use reliability and warrantied lifetimes are essential for medical device performance, and a full service molder can test and evaluate plastic parts and device assembly components for adherence with strict and consistent quality measurements, whereas commodity molders may not have these capabilities.
5. Supply chain management
Sub-assembly is common in medical devices, which can make juggling vendors difficult. As with secondary processes, full service molders are capable of sourcing items to facilitate assembly in order to reduce the number of steps in your supply chain.
At first blush, commodity injection molders appear to offer cost-effective solutions, but they can leave medical OEMs paying the price. An experienced complex injection molder like Kaysun provides a full service solution for medical devices of unquestionable quality, repeatability and value. For more on choosing the right vendor for critical-use injection molded parts, read The Ultimate Guide to Medical Parts Manufacturer Selection. Click the button below for your free copy.
Subscribe
TO OUR BLOG
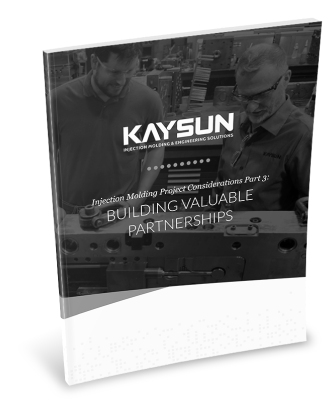
How Do Injection Molder Partnerships Influence Project Costs?
You Might Also Like...
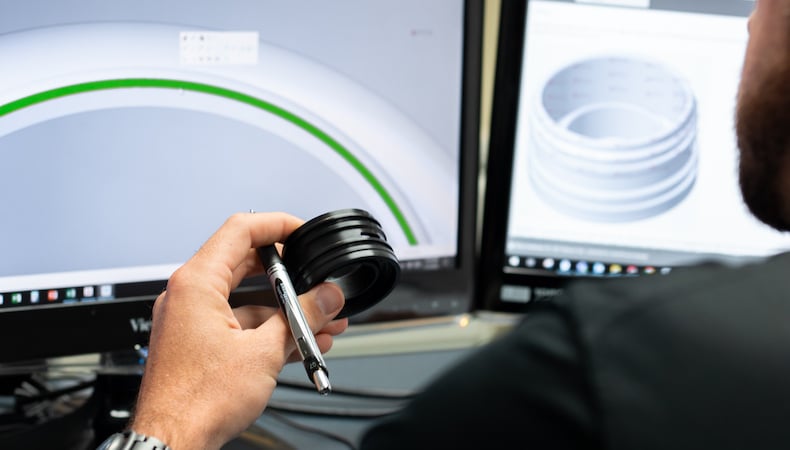
How RJG Master Molder I/II Defines Injection Molding Excellence
In custom injection molding, quality and precision are both an expectation and a g…
READ MORE
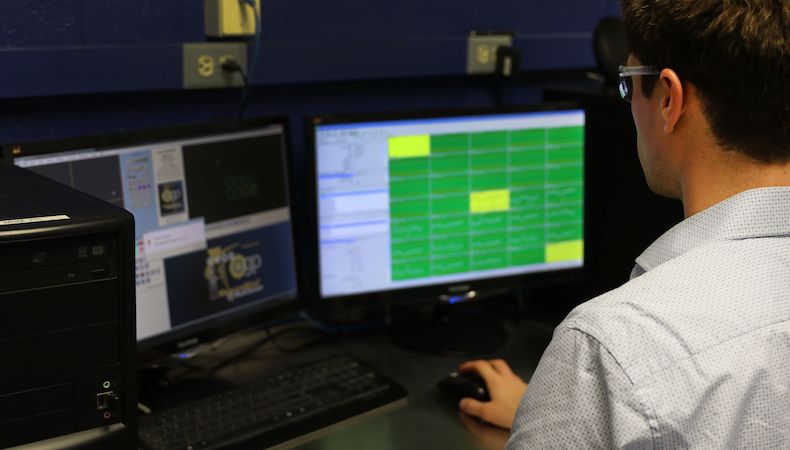
How Today’s Manufacturers Benefit from Scientific Injection Molding
As technologies and demand rapidly increase the competition in many industries, th…
READ MORE
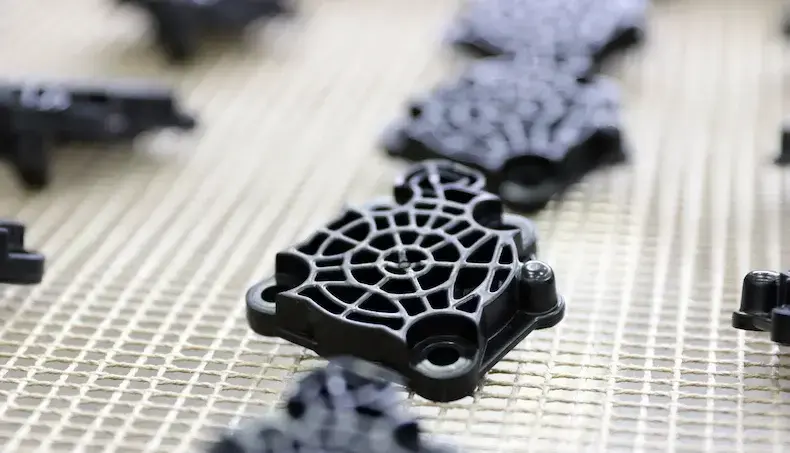
3 Engineering Support Services Your Injection Molder Must Offer
There’s no denying that pandemic-related, weather-influenced, and manmade disrupti…
READ MORE