Choose an Injection Molder With Sophisticated Assembly Capabilities
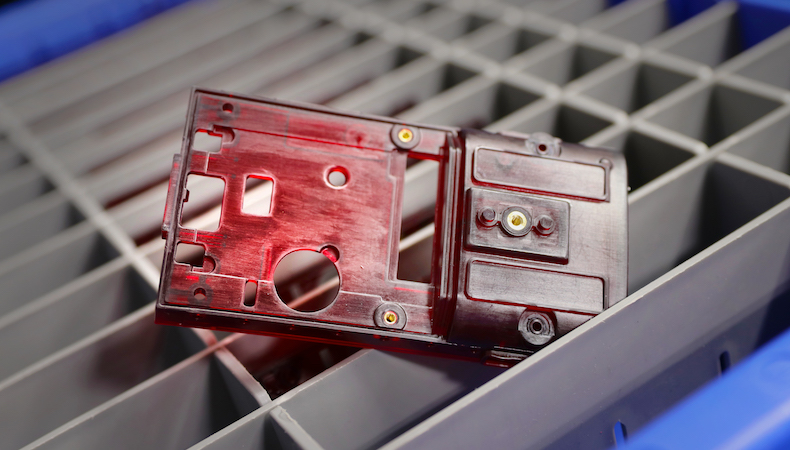
When it comes to injection molding partners, OEMs have two options: commodity or custom. In essence, the choice is that of pared-down services or comprehensive problem-solving. Both approaches have their merits, and the application often drives the decision.
However, if framed as a value-add for an OEM beyond immediate project need, custom injection molders often win the day. Their advanced capabilities and in-house services streamline supply chains — a quality and cost management win for OEMs — but there’s more. When a sophisticated process like plastic injection molding assembly is called for, custom injection molders are instrumental in buying down risk.
Plastic Injection Molding Assembly Matters During Design
Plastic injection molding assembly is a highly considered decision. How assembly impacts the finished part or component is a top priority, but its introduction into the overall injection molding process starts well before the end of the production line.
Experienced custom injection molders such as Kaysun partner with OEMs during the design phase to collaborate on solutions that keep assembly in mind. Since decisions made at this point in the process account for about three-quarters of the total final cost of the part, the implications regarding OEM cost savings are obvious.
DfM, Automation, and Metal Inserts
Moreover, a molder with design and engineering teams specially trained in the principles of Design for Manufacturability (DfM) provides opportunities to identify ways to consolidate plastic parts and simplify the molding process, including as it relates to plastic injection molding assembly. This cuts down the number of steps required to successfully manufacture a part, thereby giving OEMs another avenue to time and cost savings without introducing more risk.
Similarly, automated post-molding tasks such as adding metal inserts can keep OEM costs and risk in check. When handled by an experienced injection molding partner, the precision of automated insert molding is further aided by a thorough understanding of plastics behavior during molding. The combination ensures finished part consistency and optimal cycle times.
OEMs continue to leverage plastic injection molding assembly as a means to safely save production time and money as well as manage supply chains. Central to success is a partnership with an injection molder that balances assembly experience with efficiencies. Read our Injection Molding Guide to discover how Kaysun helps OEMs arrive at custom solutions.
Subscribe
TO OUR BLOG
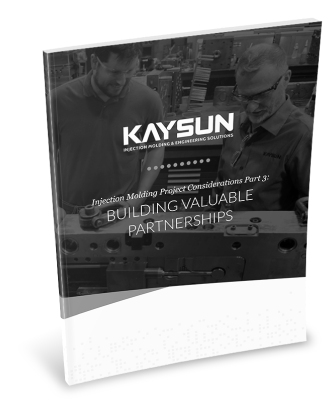
How Do Injection Molder Partnerships Influence Project Costs?
You Might Also Like...
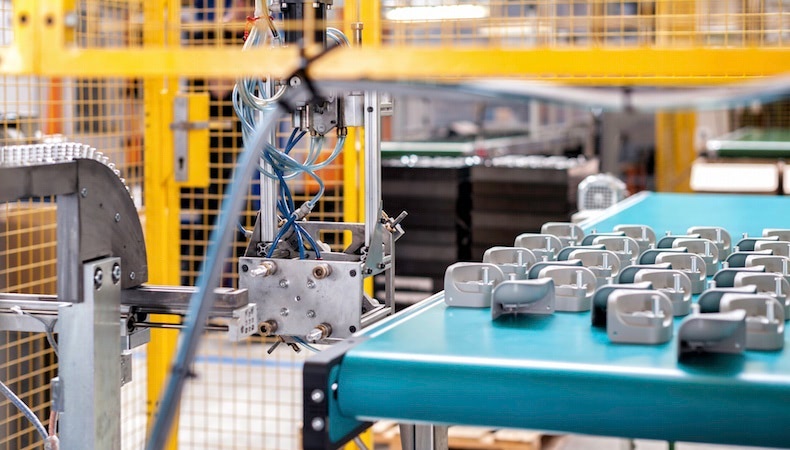
The Impact of Non-Uniform Injection Molding Wall Thickness
Shrink rates for plastic parts vary depending on the materials used and the unifor…
READ MORE
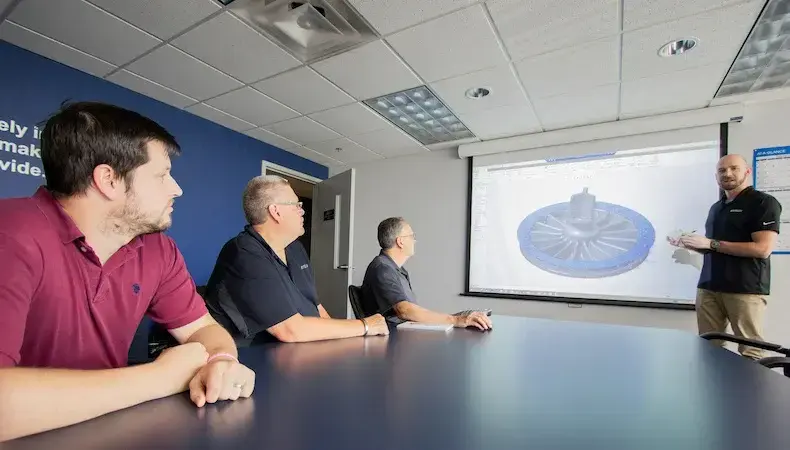
5 Engineering Factors That Improve Your Injection Molding Project
In many complex industries, decisions about which injection molder to use for cust…
READ MORE
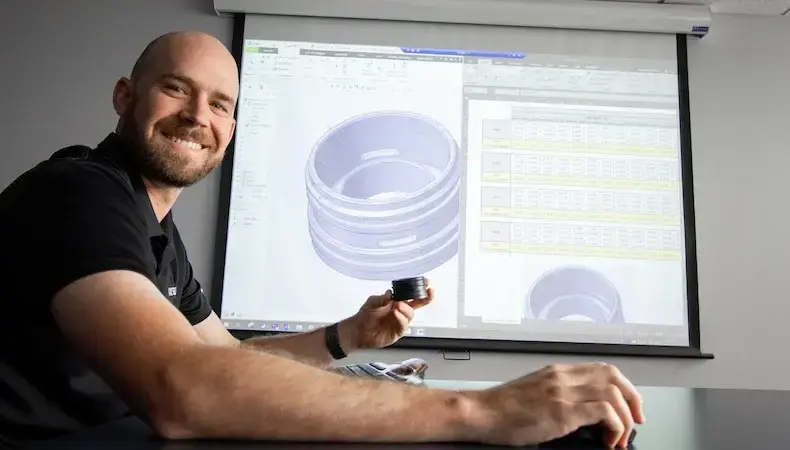
Why Continuing Plastic Engineering Education Matters to OEMs
Technologies, product needs, and customer expectations are rapidly advancing. OEMs…
READ MORE