How Automotive Manufacturers Should Evaluate Custom Injection Molders
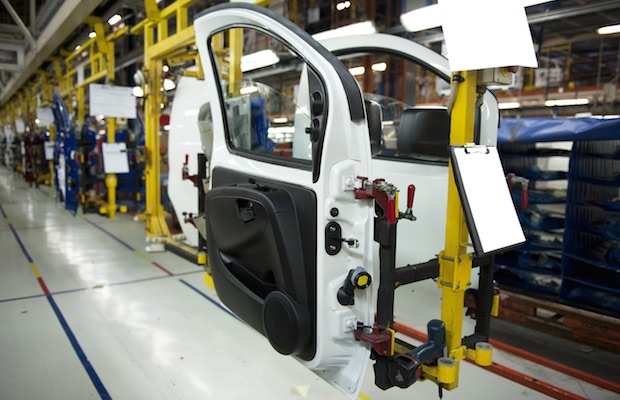
Braking, cooling, fuel delivery systems and the powertrain are all critical systems in automobiles that must consistently perform. Therefore, finding and partnering with an injection molder for these applications takes on added importance for a manufacturer.
Objectively evaluating potential custom injection molding partners requires asking some targeted questions to determine qualifications, specializations and if their expertise aligns with your needs.
Is the Molder Certified and Experienced?
IAT16949:2016 is the quality management system standard for the automotive industry. This certification demonstrates a molder’s commitment to quality and willingness to hold themselves to the highest standards in automotive engineering, manufacturing, continuous improvement and customer relationships.
In addition to certification, a molder must have a proven track record in automotive parts manufacture. Key measures of their experience include a deep understanding of what impacts part performance and quality such as:
- Moldability, including expert knowledge of specific resins for automotive components
- Dimensional requirements and tolerances
- Functionality of finished parts, specifically as it relates to working within certain design constraints to deliver sufficiently robust components
Will the Molder Conduct Design for Manufacturability Studies?
Molders in tune with the automotive industry understand the premium manufacturers place on time. Precision in component design, fit and function is non-negotiable, and for a molder to deliver otherwise means wasted time and money in costly retooling and product re-runs.
Saving you time and consistently producing quality parts is the focus of a molding partner that conducts comprehensive design for manufacturability studies.
Assessments like mold flows verify design and materials performance or, conversely, reveal areas for improvement. For example, mold flow analysis can identify improper gate locations in the part design. Knowing about needed corrections at a point when adjustments can be made without considerable impact on time or cost is invaluable.
A review of design prints is beneficial in determining feasible dimensions and tolerances before an automotive component reaches the mold process. It eliminates the time and frustration of addressing trapped steel or other moldability issues on the line, where resolving problems could delay progress by up to a month – a huge detriment to any manufacturer.
Does the Molder Specialize in Metal-to-Plastic Conversion?
A true custom injection molding partner is forward thinking. In addition to efficiently producing parts you already make from plastic, they will proactively identify opportunities to convert metal parts to plastic for reduced vehicle weight and cost.
To do so requires that the molder possesses expert knowledge of metal-to-plastic conversion for two important reasons: not all metal parts are suitable for adaptation, and those that are typically require design adjustments to ensure the resulting plastic parts won’t fail. For example, if a die cast metal piston is designed with pinholes, the new plastic component needs to have bigger holes for heavier pins to accommodate uniform wall thickness and consistent manufacturability.
Kaysun can confidently answer “yes” to every one of these questions, and we welcome the opportunity to be your automotive supplier. Contact us today to discuss your needs, or learn more in our new Designing for Critical-Use Automotive Applications eBook. Click the button below to download your free copy.
Subscribe
TO OUR BLOG
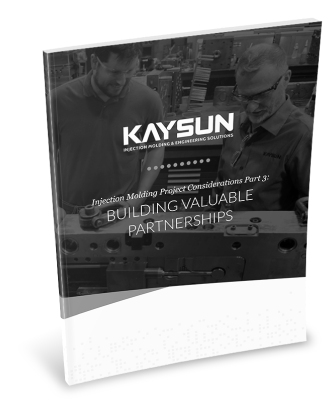
How Do Injection Molder Partnerships Influence Project Costs?
You Might Also Like...
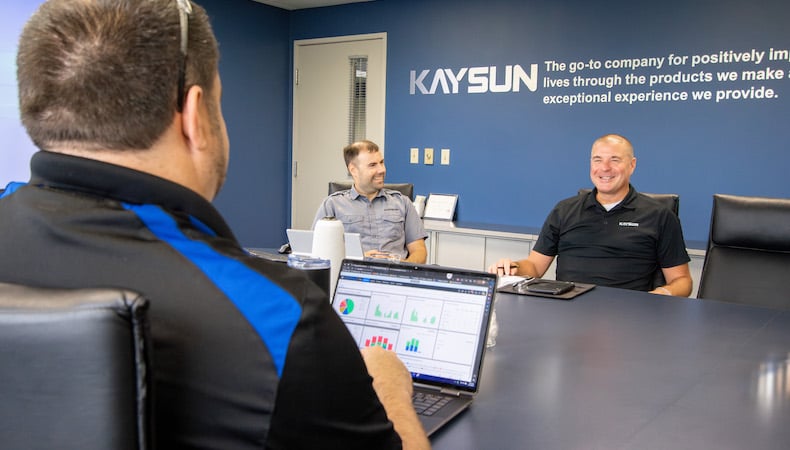
Top 3 Custom Injection Molding Trends to Watch in 2025
Despite being considered more energy efficient and producing less waste than other…
READ MORE
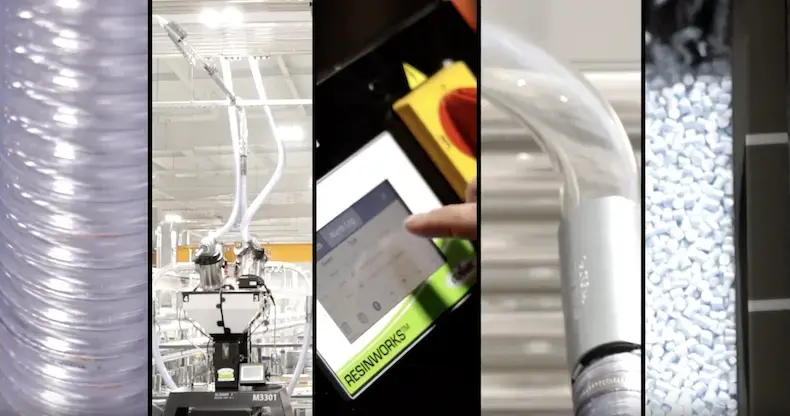
How Centralized Material Handling Streamlines Injection Molding
We consistently look for new ways to deliver timely service and top-quality parts …
READ MORE
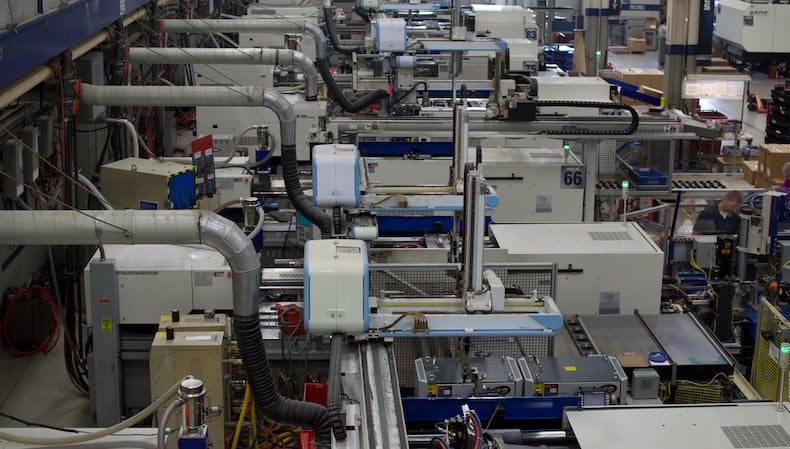
Top 14 Benefits of Injection Molding
OEMs across many industries enjoy the benefits of injection molding. It’s ideal fo…
READ MORE