Green Energy from Plastic? OEMs, Eco-Initiatives, and the Future
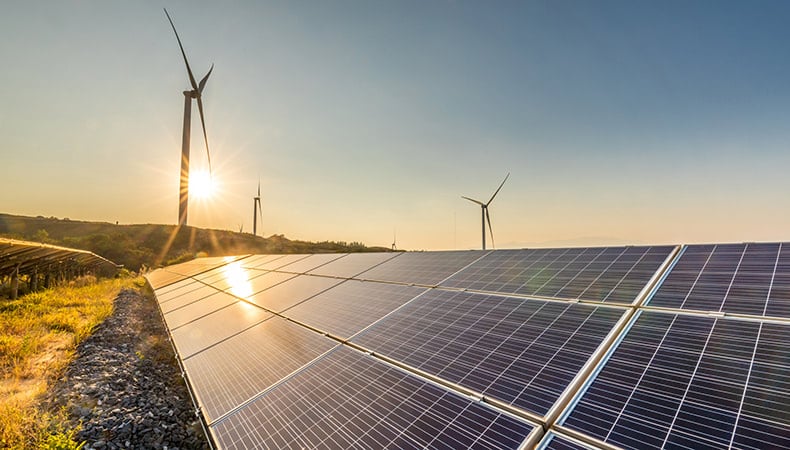
Nearly half of all plastic ever manufactured has been made since the year 2000. In a scant two decades, production went from 250 million tons to 448 million tons1 and the race is on to shift the burgeoning over-reliance on plastic to ways that promote plastics’ use as a green energy source.
Isn’t Recycling Enough?
In light of environmental sensitivities and crises worldwide, recycling plastic is top of mind for Americans — yet only 9% of plastic is recycled in the USA, which is well behind Europe and China at 30% and 25% respectively.2 Even with these arguably lagging percentages, recycled plastic is central to transforming one plastic product into another, and also a key player in energy savings since the act of recycling plastic takes 88% less energy than making plastic from raw materials.3
But not all plastics are recyclable — and that’s where industries have an opportunity to advance initiatives that convert plastics to fuels, and champion green energy production and use.
Plastics, Industry, and Green Energy
Plastics are comprised of materials that, in their natural state, are generally tapped as energy sources: natural gas, oil, coal, and plants. As technologies and capabilities advance, there are concentrated efforts being made to revert non-recyclable plastics to these energy sources on a molecular level.
Pyrolysis — the process of heating non-recyclable plastics without using oxygen — makes energy recapture possible. It melts plastic, vaporizes the melt into gases, then cools and condenses the gases into other forms of oil, fuel, and petroleum-based products for uses across a variety of industries.
The prevalence of injection molded plastic parts and components have many OEMs incorporating plastics into their complex designs. The automotive industry, for example, recently underwent a regulatory revamp wherein lightweighting is pivotal for compliance which largely transitioned metal-to-plastic conversion from an option into a mainstream manufacturing process. Also, automotive OEMs are turning to injection molded plastic parts to better address the unique needs of electric vehicles as the public continues to embrace this eco-conscious transportation choice.
Such large-scale use of plastic spurs certain green energy initiatives on the part of OEMs. Sustainability comes to the fore in how regrind is handled — a standard process for optimizing materials usage by carefully combining scrap plastics and primary materials to produce injection molded parts at a reduced cost and lower draw on natural resources.
An emerging trend is the use of regrind as a fuel source within different industries. For example, many large manufacturing facilities, such as paper mills, are increasingly burning plastic regrind pellets to power their systems in an eco-smart fashion. In other cases, pre-regrind scrap plastic is sold to secondary buyers for repurposing into everyday plastic items that benefit and beautify communities. Kaysun supports scrap plastic recycling and our ongoing initiatives have brought plastic park benches, playground equipment, and other outdoor accessories to our surrounding area.
As OEMs lean into initiatives surrounding green and perhaps eventually clean energy from plastic, it’s important to weigh environmental considerations with part needs when assessing project materials. Learn what to look for in our eBook, Resin Selection for Industrial Applications. Click the button below to access your copy now.
SOURCES
1National Geographic, Fast facts about plastic pollution, December 20, 2018
2National Geographic, Here’s how much plastic trash is littering the earth, December 20, 2018
3Recycling Coalition of Utah, RCU Website Home Page, Undated
Subscribe
TO OUR BLOG
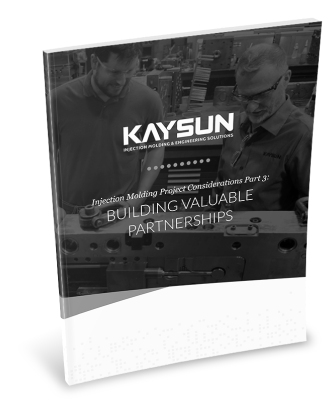
How Do Injection Molder Partnerships Influence Project Costs?
You Might Also Like...
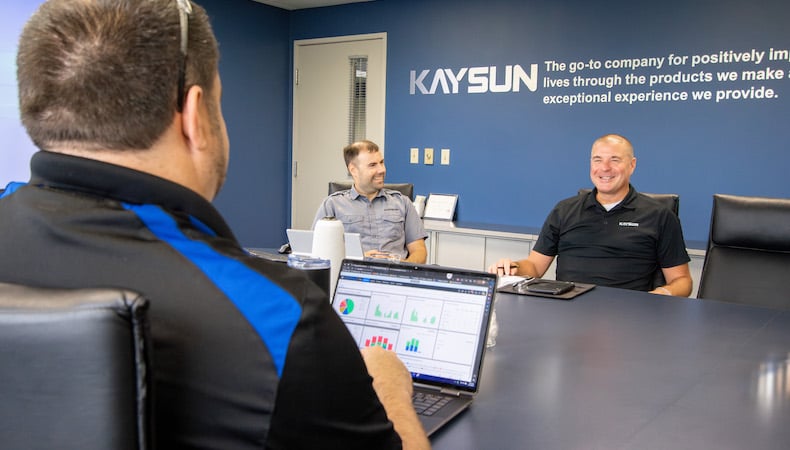
Top 3 Custom Injection Molding Trends to Watch in 2025
Despite being considered more energy efficient and producing less waste than other…
READ MORE
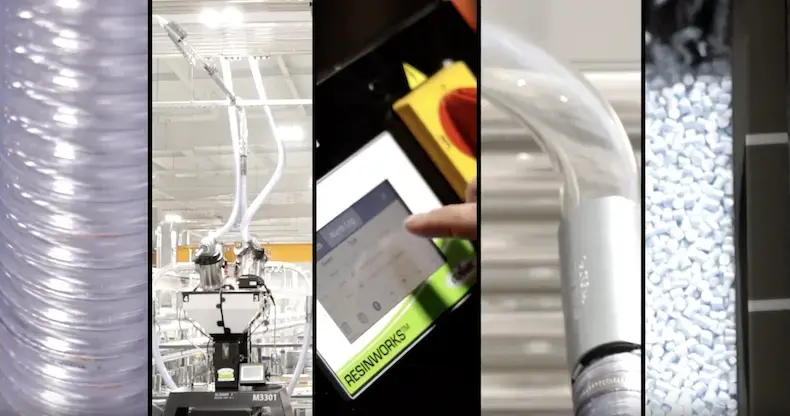
How Centralized Material Handling Streamlines Injection Molding
We consistently look for new ways to deliver timely service and top-quality parts …
READ MORE
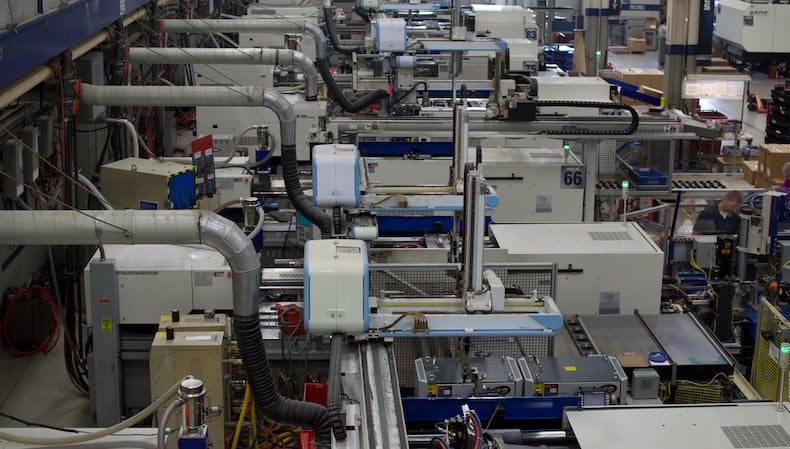
Top 14 Benefits of Injection Molding
OEMs across many industries enjoy the benefits of injection molding. It’s ideal fo…
READ MORE