How Draft Benefits Injection-Molded Part Design and Outcomes
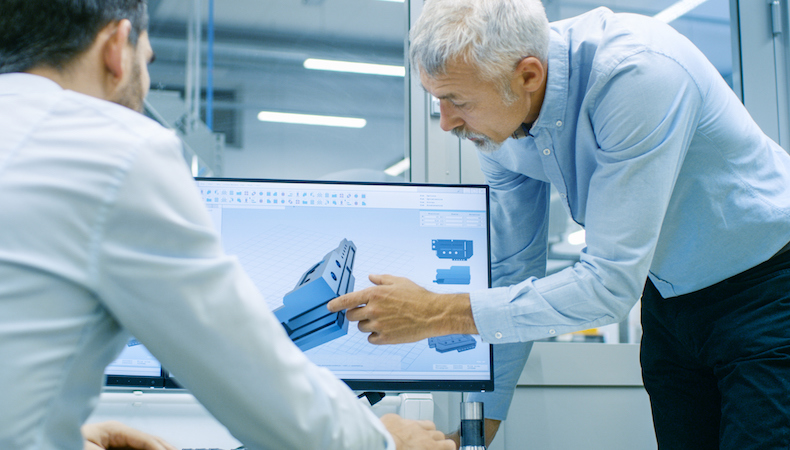
Custom injection molding is a go-to for OEMs across a range of industries because of design and engineering precision, production repeatability, and cost-effective solutions.
Injection molders understand that consistently delivering defect-free parts and products to these standards is a top priority and a true value-add to their OEM partnerships.
Quality assurance begins in the design phase. Engineers are faced with many decisions, but among the most important are those that impact the end of the injection molding process — what has to happen to ensure the plastic part ejects cleanly?
Draft: Small Detail, Big Impact
Draft angles are applied in small degrees, which may suggest they are somewhat inconsequential; however, the opposite is true. The goal is to achieve the greatest draft angle possible, but that doesn’t mean a certain degree is calculated once and used universally throughout the design. Many design properties influence how, where, and to what degree the taper will be applied including:
- Material choice
- Wall thickness and depth
- Shrink rates
- The need for controlling a part’s surface finish
Draft is so important, in fact, that engineers developed and use common draft angle guidelines. While 1 to 2 degrees is considered the norm, draft angles can drop to 0.5 degrees on vertical faces, increase to 3 degrees for shutoffs and light texture, or in excess of 5 degrees for heavy textures.
Why the specificity? The answer is twofold: Draft prevents molded plastic from sticking in the tool during ejection, and it keeps ejector pins from leaving marks when the part is ejected from the tool. Incorrect or omitted draft angles can cause costly rework due to part warpage, stresses, or breakage during plastic cooling cycles.
Undercuts: Does Draft Matter?
Undercuts — design features such as ports, latches, threads, or barb fittings that cause injection molded parts to not fully or cleanly eject — can be problematic during precision injection molding. Ideally, undercuts are avoided altogether during design but sometimes the undercut is part-critical. What then?
In some instances, the easiest solution is repositioning the parting line to essentially split the undercut. Draft plays an essential role in successfully making this change, too. By adjusting the outside draft angle, the parting line can be moved without impacting moldability or potential ejection issues.
Paying attention to how and when draft is applied during part design sets the entire project up for success. Part integrity and quality are maintained throughout the initial process and in future runs, which helps OEMs better predict outcomes and serve their customers. Learn more in our guide, Critical-Use Plastic Parts: Key Design and Injection Molding Considerations. Click the button below to download your copy now.
Subscribe
TO OUR BLOG
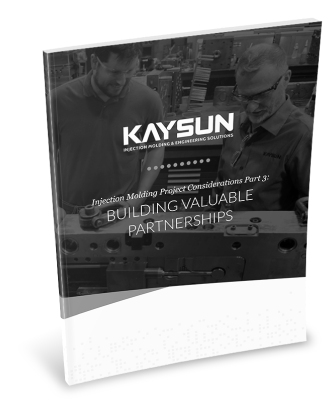
How Do Injection Molder Partnerships Influence Project Costs?
You Might Also Like...
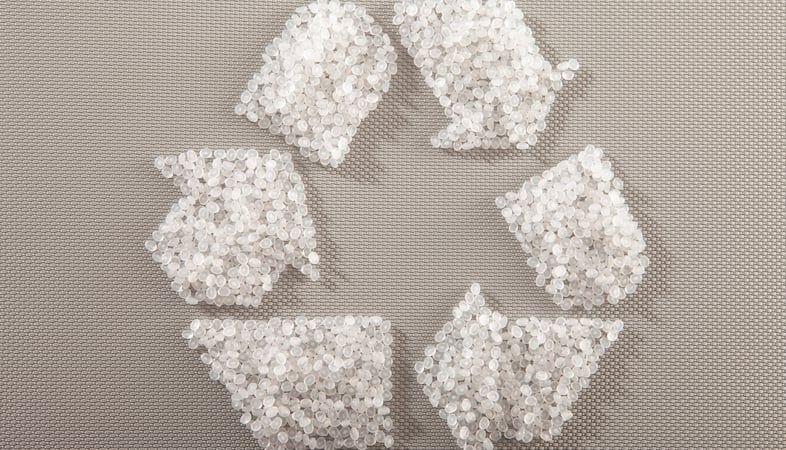
How Kaysun’s Culture of Sustainability Benefits OEMs and The Planet
Injection-molded parts and products are staples for OEMs in industries ranging fro…
READ MORE
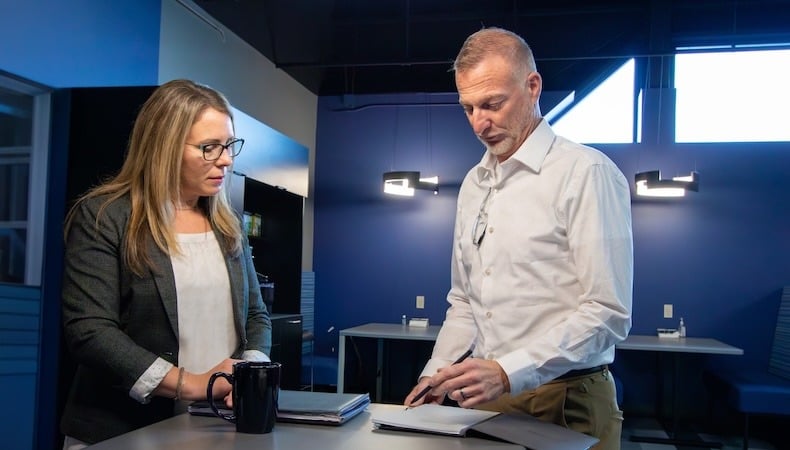
12 Common Injection Molding Questions — Answered!
Injection molding is a versatile and precise process, making it ideal for OEMs tha…
READ MORE
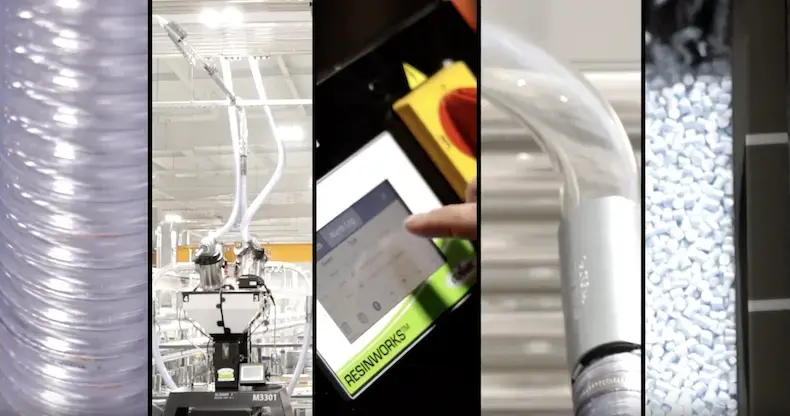
How Centralized Material Handling Streamlines Injection Molding
We consistently look for new ways to deliver timely service and top-quality parts …
READ MORE