Using DfM During Product Development to Control Part Costs and Quality
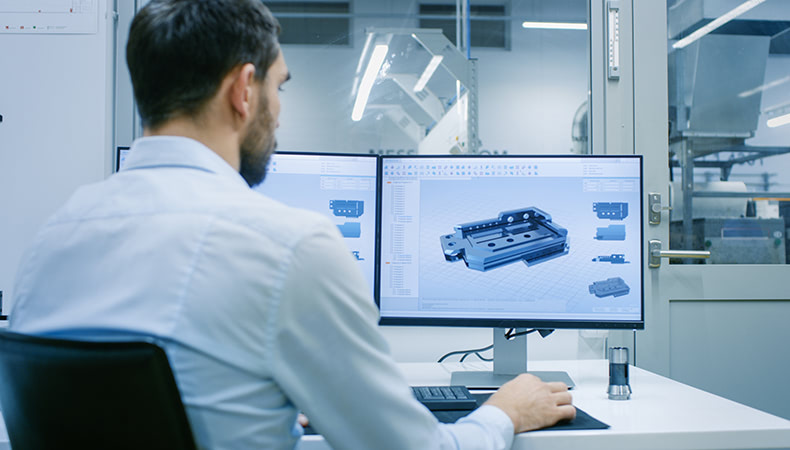
It’s generally accepted that roughly 80% of a part’s total cost is determined during the design/development phase, and cannot be reduced – or is extremely difficult and expensive to change – once the design is finalized. However, by utilizing a Design for Manufacturability (DfM) approach and the specialized expertise of a plastics engineer, deliberate design decisions can be made to help manage/reduce total part and production costs.
Focus on Product Development
Product development is an area where the value of partnering with an injection molder with experience in DfM really shines. Specially trained DfM engineers come alongside the design team to evaluate the processes necessary to optimize all facets of manufacturing for a particular project, with in-depth scrutiny of:
- Potential moldability issues within the part design
- Part design modifications to simplify tooling
- Opportunities for appropriate materials substitutions to enhance part quality and/or reduce overall costs
Further, since DfM is based on project-specific details, the production and cost efficiencies are “real world” and can be readily applied to a project. Questions are answered upfront about:
- Tolerances
- Functionality
- Tooling
- Materials performance
- Potential operational constraints
DfM and Injection Molded Plastic Parts and Components
For injection molded plastic parts and components, DfM is instrumental in informing design decisions well before they impact project quality and costs, including:
- Less reliance on secondary operations, such as assembly or finishing
- Minimizing wall thickness whenever possible
- Using gates designed for insertion into the thickest part wall with minimal to no trimming
- Incorporating adequate draft to ensure proper release from the mold
- Accommodating generous radii at part geometry intersections to enhance melt flow and reduce stress
Designing a part with a focus on manufacturability is a proven strategy for reducing costs, preventing rework and improving time to market. The relationship manufacturers choose to pursue with an injection molder will dictate how well DfM is integrated into the process, and the level of collaboration between the two will define success.
Kaysun is committed to true partnerships, and we lend our expertise to every phase of a project including the most expensive part — tooling. Learn more in our eBook, Tooling Design for Injection Molding. Click the button below to access your copy now.
Subscribe
TO OUR BLOG
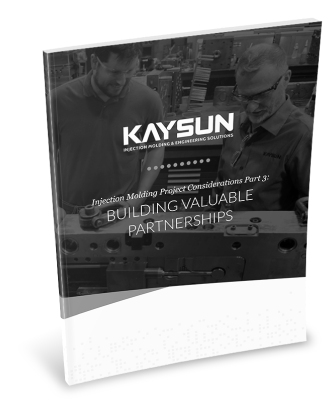
How Do Injection Molder Partnerships Influence Project Costs?
You Might Also Like...
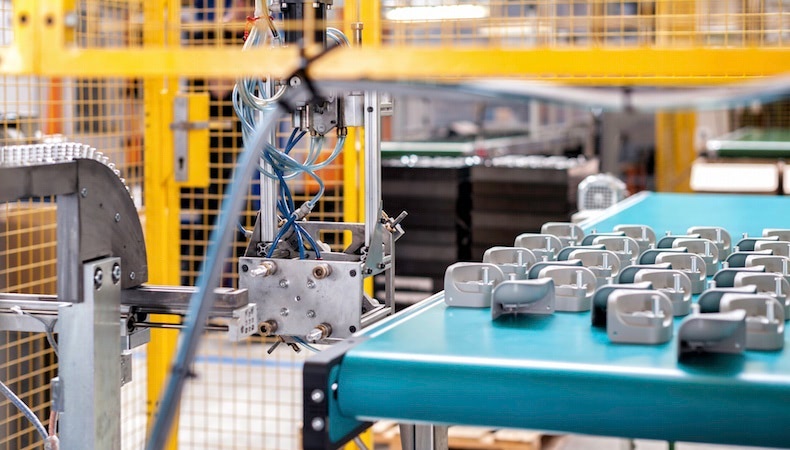
The Impact of Non-Uniform Injection Molding Wall Thickness
Shrink rates for plastic parts vary depending on the materials used and the unifor…
READ MORE
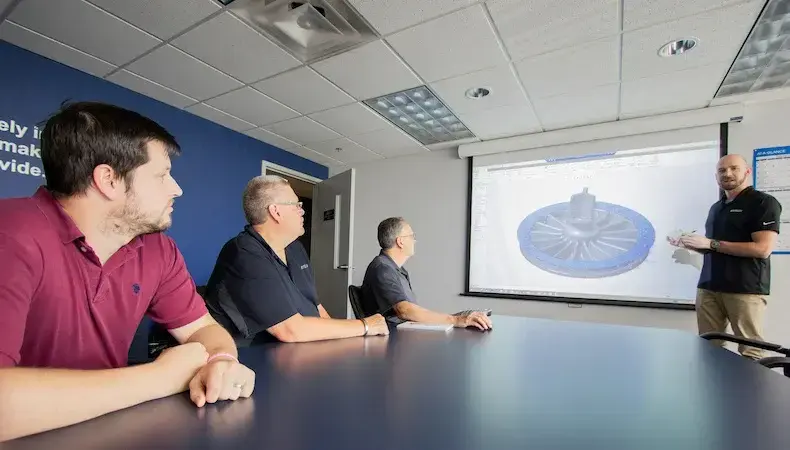
5 Engineering Factors That Improve Your Injection Molding Project
In many complex industries, decisions about which injection molder to use for cust…
READ MORE
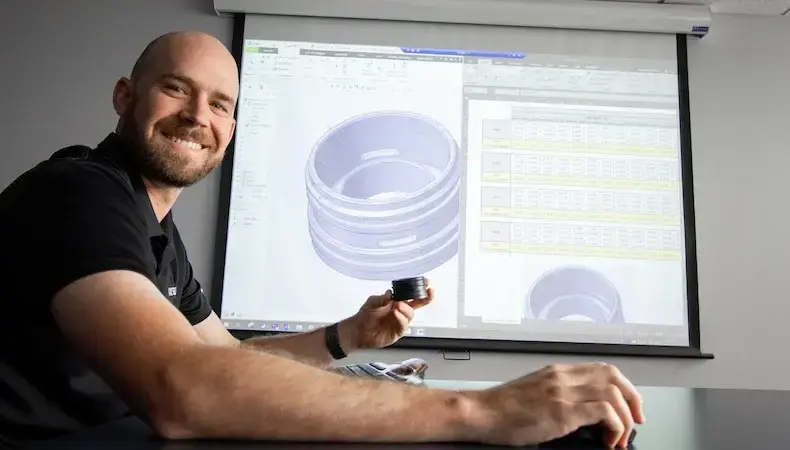
Why Continuing Plastic Engineering Education Matters to OEMs
Technologies, product needs, and customer expectations are rapidly advancing. OEMs…
READ MORE