What's More Efficient: Complex Tooling Design or Machining?
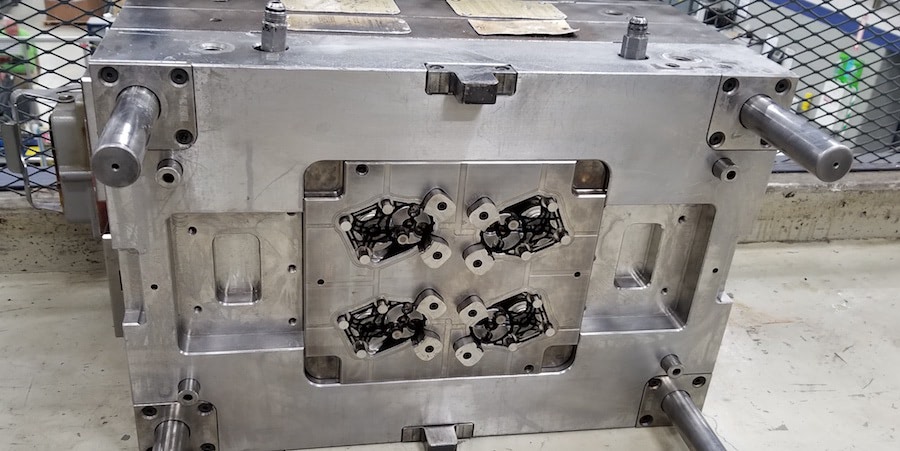
There is more than one way to produce an effective plastic injection-molded part. The question is: is complex tool design the answer or is it better to utilize machining technologies to complete the task?
Complex Tooling vs. Machining
If you're looking for the highest quality, designing a complex tool that precisely molds in the required part features is the ideal solution. However, depending on the situation, turning to machining may be a more cost-effective choice. This is particularly true when the cost of building a tool with such precision may be too high to justify the investment for the quantity desired. There is also the possibility of a tolerance issue if the precision required is better managed via machining.
Building more complex tools — those that mold in all the geometric details of a part — requires more engineering, testing, and development than simple tools. This is consequently more expensive, and such investments aren’t always justified. Take the example of defense manufacturing — production of military devices is almost always low in volume, so it may not be economical to build a highly functional yet expensive tool that will outstrip production needs. In this situation, you can build a simple tool and use machining for the required geometric features: slots, screw holes, etc. This will reduce the total cost of production for a short run.
You also can't forget about potential tolerance issues. Some polymers can’t predictably hold tolerances during the injection molding process, or even tighter tolerances — down to ten-thousandths of an inch — than the tool can guarantee. In these cases, features must be handled via machining into the molded part.
Use an Expert to Help You Decide
How do you determine your company’s best course? Have a highly capable engineering team like Kaysun perform a comprehensive cost analysis of the specific manufacturing situation. We can help you determine the optimal solution that best meets your needs, and our in-house tooling capabilities mean faster turnarounds.
Want to learn more about tooling design for injection molding, including the main stages of design, steel vs. aluminum, lifecycle costs, and more? Be sure to read our Tooling Design for Injection Molding whitepaper below.
Subscribe
TO OUR BLOG
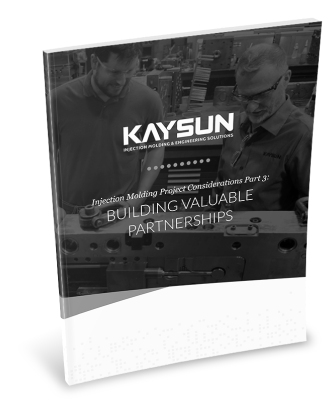
How Do Injection Molder Partnerships Influence Project Costs?
You Might Also Like...
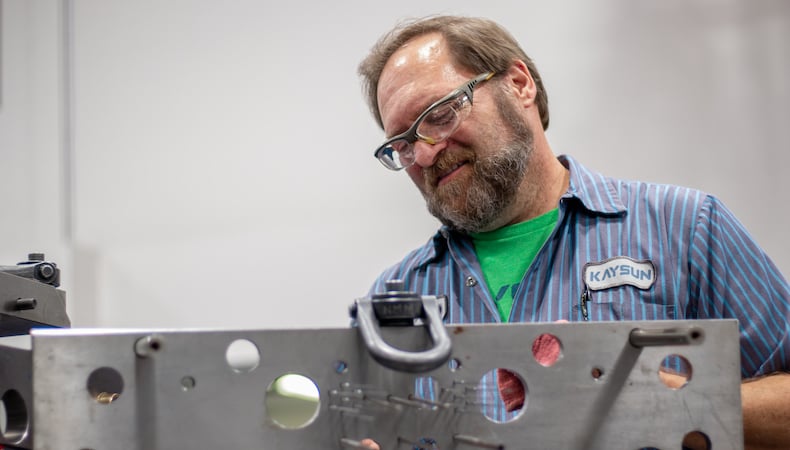
Injection Molding Quotes: 5 Tips to Help Get Tooling Right
Few things impact injection-molded part quality as much as tooling design, materia…
READ MORE
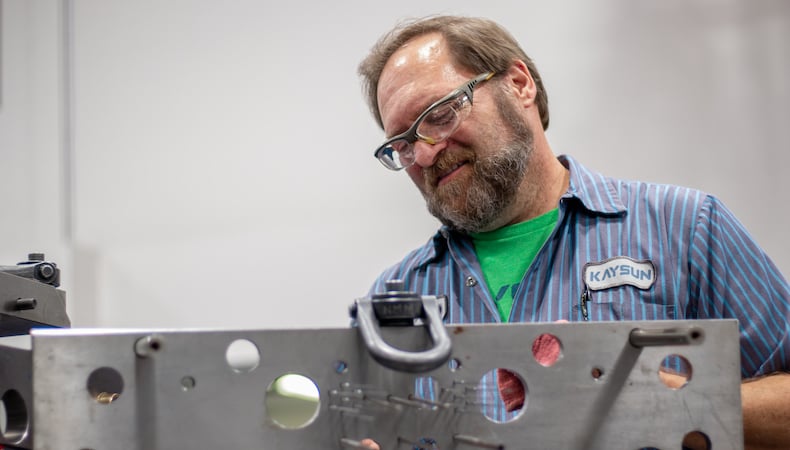
Tooling Audits & Evaluations: How Molders Help OEMs Gauge Health of Assets
When an OEM pursues an injection molding program, tooling is among the most highly…
READ MORE
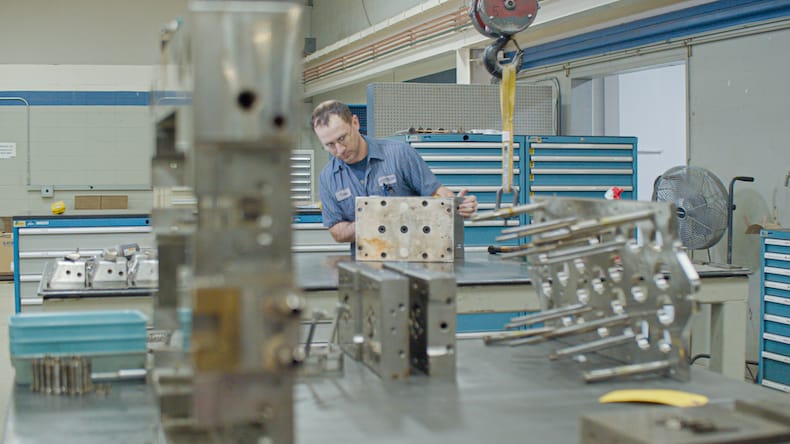
How Concurrent Design Review Aligns Injection Molding Tooling and Parts [VIDEO]
Tool design is an essential and sometimes underestimated part of injection molding…
READ MORE