Prototype Tooling: What Option Is Best for You?
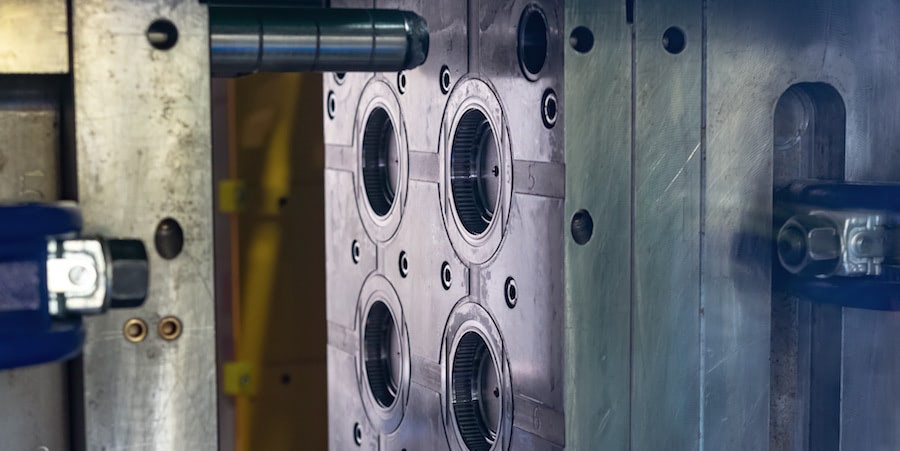
There are several prototype tooling options for your designs. The one you choose depends on what you expect to accomplish with the prototype. For example, will the prototype be subjected to testing? Does it need to be "dressed up" for presentation? Will it need to meet tight tolerance requirements?
Let's explore the most common prototyping options: SLA/SLS, urethane cast, soft tooling, and hard tooling. Which is right for your component? Read on to discover the advantages and disadvantages of each.
SLA/SLS Technology
Stereolithography (SLA) and selective laser sintering (SLS) are additive manufacturing technologies that are ideal for rapid prototyping. In SLA, an ultraviolet laser builds a solid part from a CAD pattern by solidifying and curing individual layers of a photopolymer resin. Although SLA is relatively fast, there are some size limitations, and photo-curable resins can be expensive. SLA parts can also be “dressed up” easily with paint or dye for trade shows or presentations.
SLS is similar to SLA except that it utilizes a carbon-dioxide laser to fuse together thin layers of powdered metal, plastic, glass, or ceramic to construct a solid product. An advantage of SLS over SLA is that it can make prototypes from a greater variety of materials that may have properties closer to production-intent materials.
Both processes are good for fitment exercises or early proof of concepts. Even though material options have increased over the years, SLA and SLS are still not production intent. The processes also have limitations from a functional standpoint, especially compared to higher-grade engineered resins. SLS and SLA are geared toward very low quantities but can also provide very quick turnarounds.
Urethane Cast/Mold
Urethane cast/mold is a low-volume production method that utilizes polyurethane plastic materials to produce prototypes. These products are ideal for marketing samples because they can be finished to look like hard-tooled plastic parts. Materials are limited and may not be able to deliver the same qualities that preferred production plastics can. Urethane cast/mold can be a cost-effective method of prototyping if there is a need for a higher quantity of parts at the fitment or proof-of-concept stage. Overall the process is fairly limited and becoming less common in the industry.
Soft Tooling vs Hard Tooling
Soft Tooling
Soft tooling is a very common method in the injection molding industry and provides relatively inexpensive tooling, a high number of parts, and may also allow for use of the intended production material. Soft tooling is usually built with aluminum cores and cavities.
There are several different variations or options for soft tooling, but typically tools and samples can be turned around in a few weeks. This may be an option for early prototype builds if the parts are simple, tolerances are loose, and function and fitment are not critical requirements. Soft tools, however, have limited ability for design or dimensional changes once the tooling is complete and sampled. Processing development is also limited.
Hard Tooling
For engineered parts with tight tolerances, testing requirements, and an intention for functional use, hard tooling is most certainly the best option. The upfront cost is the most expensive, and the lead time will be the longest with this option; however, it will likely save both time and money down the road.
Hard tooling will guarantee the ability to use production-intent resin and can accommodate design and dimensional changes after the parts have been sampled. Hard tooling also provides the opportunity for process development and verification early in the program timeline. Not only will this yield the best parts for testing and development, it will shorten the production approval process (typically when timing is the most critical). Hard tooling can also offer the opportunity to supply several hundred thousand parts, bridging the gap from prototype to production.
When it comes to prototyping, understanding what you need is important when considering what option to pursue. If you have a tight-tolerance part that is critical to the function of your system, cutting corners and costs in the development stage may not always save money over the long term. Be sure you are not just looking at cost or lead time when considering prototyping options, as there are many more factors involved.
To learn more about the importance of qualifying a tool in the overall scientific molding process, download our free infographic, The Process of Scientifically Qualifying a Tool.
Subscribe
TO OUR BLOG
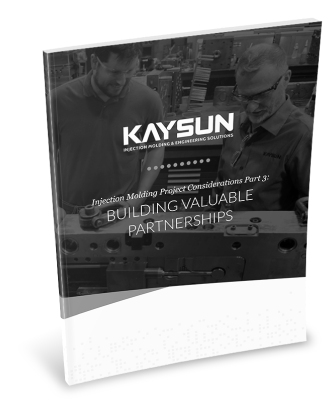
How Do Injection Molder Partnerships Influence Project Costs?
You Might Also Like...
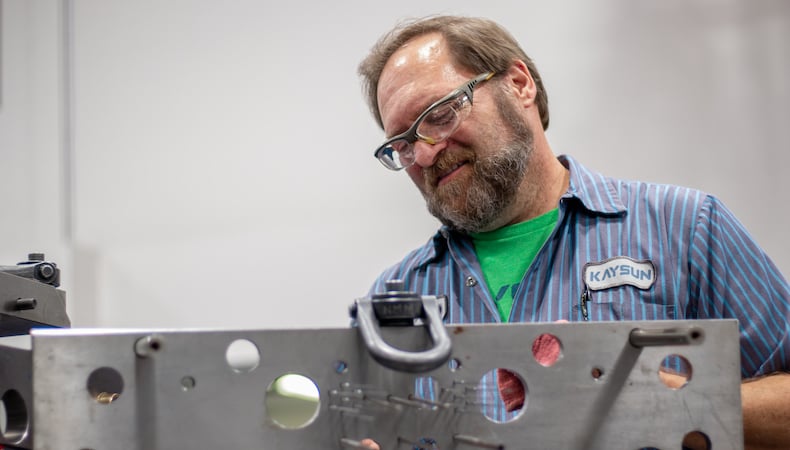
Injection Molding Quotes: 5 Tips to Help Get Tooling Right
Few things impact injection-molded part quality as much as tooling design, materia…
READ MORE
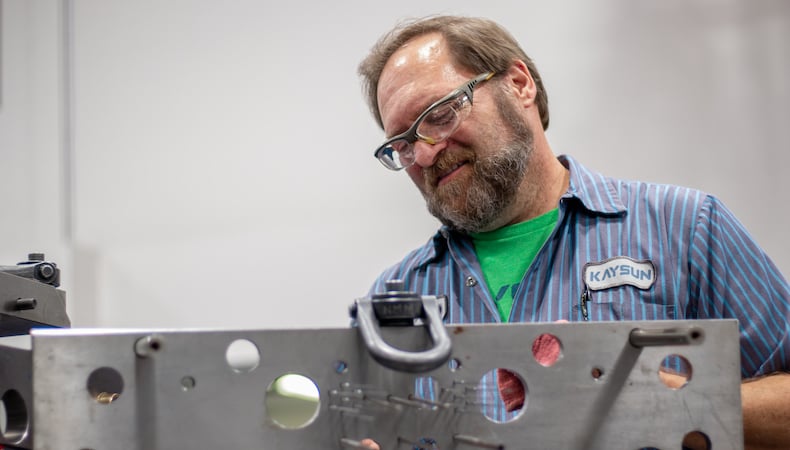
Tooling Audits & Evaluations: How Molders Help OEMs Gauge Health of Assets
When an OEM pursues an injection molding program, tooling is among the most highly…
READ MORE
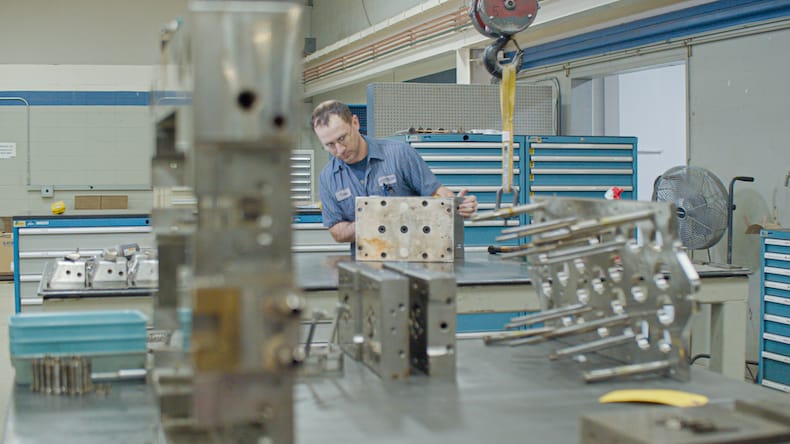
How Concurrent Design Review Aligns Injection Molding Tooling and Parts [VIDEO]
Tool design is an essential and sometimes underestimated part of injection molding…
READ MORE