Hand Loads: Cost Effective Solutions for Complex Plastic Parts
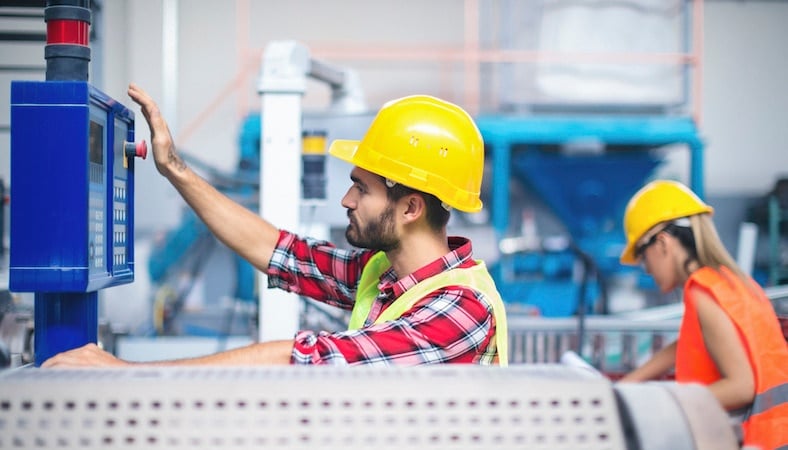
It seems old-fashioned to load anything by hand these days, especially in a high-tech industry like injection molding. However, “hand loads”—mold inserts that are physically placed into a mold and then removed when the part is finished—are essential for the production of certain parts.
A Simple Approach to Complex Geometries
Hand loads are used to create complex geometries—like undercuts and threads—that can’t be formed in the line of draw, and are primarily used in these scenarios:
- A very low-volume application where it is not practical to spend extra money on automatic lifters, slides or unscrewing mechanisms
- The part geometry is so complex it cannot be formed using automatic lifters, slides or unscrewing mechanisms
Injection molders employing hand loads in these situations offer simple solutions to complex design challenges—ideal opportunities to exceed client expectations for design and production. While some injection molders view hand molds as outmoded, the reality is that they play a vital role in:
- Forming very complex geometries
- Eliminating the need for secondary operations, thereby speeding up the production cycle
- Reducing production of scrap and probability of rework
- Decreasing overall project costs
Take, for example, a part Kaysun produced for the automotive industry. The very complex part requires two angled air channels, and the initial concept was to drill out the channels as a post-mold operation. Instead, we used hand load inserts to create the channels, eliminating machining altogether, which reduced costs and improved quality.
Practicalities and Best Practices
Hand loads are practical complex injection molding solutions when these best practices are implemented:
-
Always build multiple hand loads to allow for proper cooling between cycles, maintaining production cycle times and backups if a hand load gets damaged
-
Utilize small rare-earth magnets to fully seat and hold hand loads in place to minimize the chance of damage due to accidental shifting
-
Create hand loads from soft steel (P-20) to prevent damage if an insert is accidentally closed upon during molding
-
Use a low-pressure mold close to minimize potential damage
-
Design larger hand loads with gripping features so they can be held more easily, and not as likely to be dropped and damaged
-
Build an extraction fixture for hand loads having complex geometries
Potential Challenges
It's important to note that hand loads require extra labor for installation and removal. While this may skew the cost/benefit analysis, it may also be the only way to meet the customer’s needs.
Another concern is that using too many hand-loaded inserts per project can change molding process/cycle times which, in turn, can affect part-to-part consistency and possibly result in bad product, high scrap rates and more shorts of filling variations. Every effort must be made with hand loads to keep the molding cycle as consistent as possible.
Remember that hand loads are an extension of the mold, and precise temperatures must be maintained for molding and part consistency. Using water or air to pre-cool or a heating fixture to pre-heat hand loads to a constant temperature that matches the mold temperature improves consistency of cycle times. You may also consider making several sets of hand molds so they can be swapped out during production to maintain the appropriate temperatures and cycle times.
Despite the extra care that is required with hand loads, they can be the best solution for efficiently producing complex parts and/or low-volume runs at lower cost. Learn more about how injection molders impact outcomes in our SlideShare presentation, The ROI of Improved Project Flow. Click the button below to access your free copy.
Subscribe
TO OUR BLOG
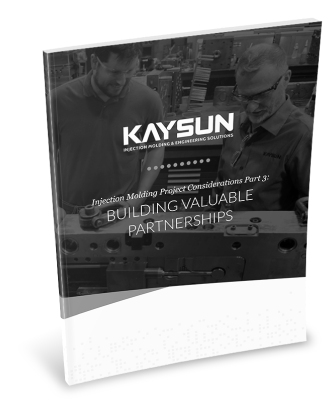
How Do Injection Molder Partnerships Influence Project Costs?
You Might Also Like...
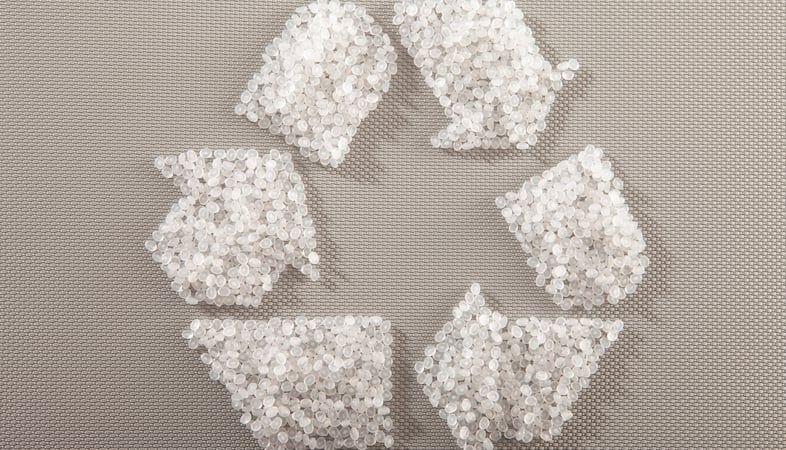
How Kaysun’s Culture of Sustainability Benefits OEMs and The Planet
Injection-molded parts and products are staples for OEMs in industries ranging fro…
READ MORE
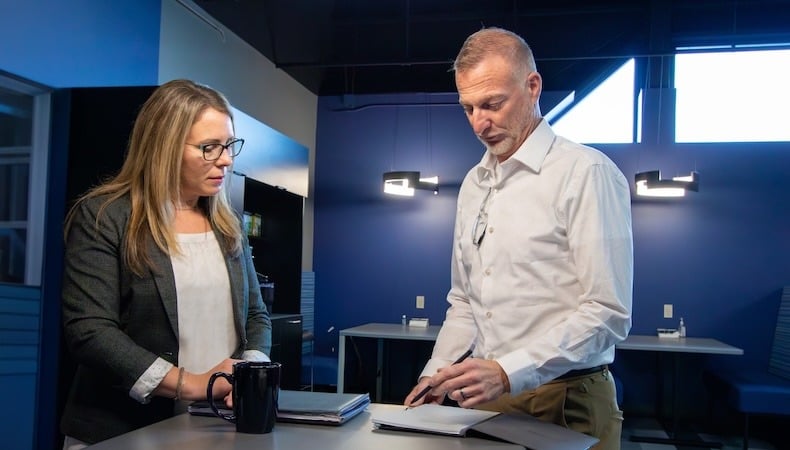
12 Common Injection Molding Questions — Answered!
Injection molding is a versatile and precise process, making it ideal for OEMs tha…
READ MORE
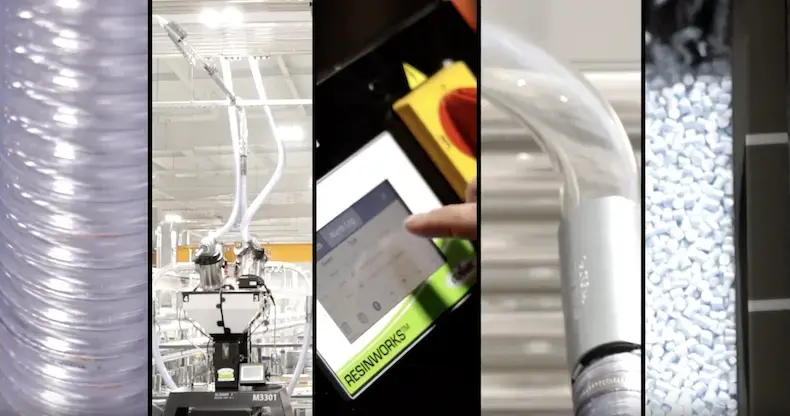
How Centralized Material Handling Streamlines Injection Molding
We consistently look for new ways to deliver timely service and top-quality parts …
READ MORE